Augusta Metal Recycling Facility Receives Green Light for $760M Bond Authorization
By:Admin
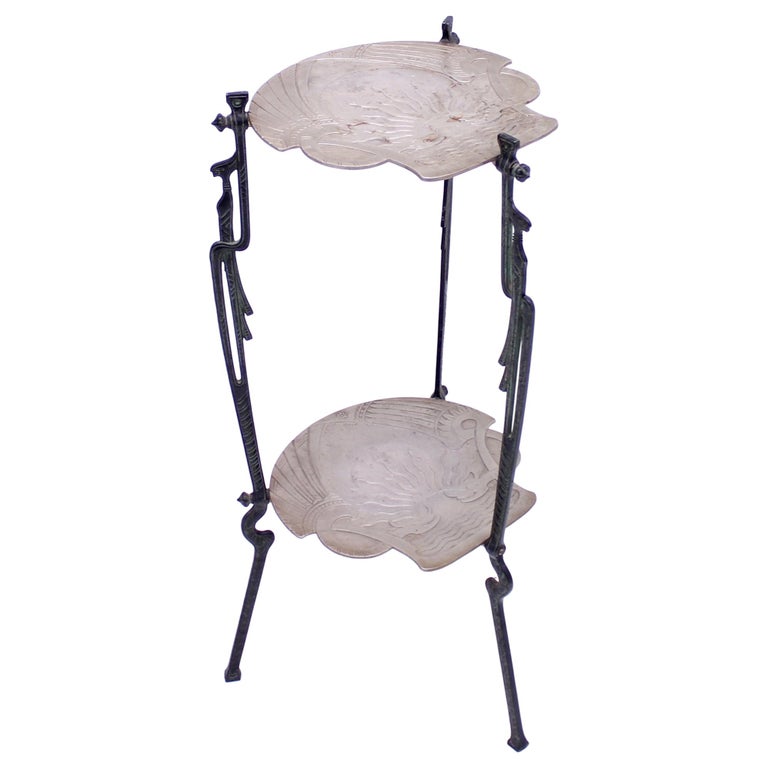
Introduction (approx. 100 words)
In recent news, an Augusta metal plant has been granted authorization for $760 million in bonds, marking a significant step towards establishing a state-of-the-art metal recycling and secondary smelting facility. However, it faced criticism from the Savannah Riverkeeper regarding air permit issuance. In this blog, we will dive deep into the implications of this development, shedding light on the potential of metal secondary recycling, and highlighting the positive impact it can have on sustainability and the environment.
Understanding Metal Secondary Recycling (approx. 250 words)
Metal recycling is a crucial aspect of the modern industrial landscape, contributing to both environmental conservation and economic growth. Secondary smelting facilities play a pivotal role in the recycling process by converting scrap metal into reusable material, reducing the industry's reliance on virgin metal production. By doing so, these facilities contribute to a circular economy while minimizing waste generation.
Facility Overview and Importance (approx. 200 words)
The recently authorized metal recycling and secondary smelting facility in Augusta will serve as a beacon of sustainable industrialization, demonstrating the tremendous potential of such operations. With an investment of $340 million, the facility aims to refine metal scraps through an innovative secondary smelting process, effectively minimizing the environmental footprint associated with traditional metal production.
Benefits of Metal Secondary Recycling (approx. 300 words)
1. Environmental Impact: Metal recycling significantly reduces energy consumption, greenhouse gas emissions, and the extraction of natural resources. By utilizing secondary smelting, this facility will effectively minimize carbon emissions, deforestation, and water pollution, while preserving valuable natural resources for future generations.
2. Economic Growth: The establishment of such a facility generates employment opportunities, stimulating local economies and ensuring long-term sustainable growth. Additionally, increased recycling rates not only reduce waste management costs but also provide a reliable and affordable source of raw materials for various industries.
3. Energy Conservation: Secondary smelting facilities contribute to energy conservation by requiring significantly less energy compared to primary metal production. By utilizing advanced technological processes and efficient energy management systems, this facility will play a crucial role in mitigating the energy crisis and advancing sustainable development.
4. Resource Conservation: Metal recycling and secondary smelting mitigate the need for extracting and processing new ores. This, in turn, helps preserve our finite natural resources, lessens environmental degradation caused by mining activities, and reduces our dependence on foreign sources of raw materials.
Conclusion (approx. 150 words)
The authorization of $760 million in bonds for the Augusta metal plant signifies a promising step towards establishing a sustainable metal recycling and secondary smelting facility. By embracing advanced technologies and innovative practices, secondary smelting operations demonstrate the potential to achieve both environmental and economic sustainability. From reducing carbon emissions and conserving natural resources to supporting local economies and generating employment opportunities, such facilities can spearhead the transformation towards a circular economy.
However, it is crucial to address the concerns raised by local communities, such as the Savannah Riverkeeper, regarding air permit issuance. Striking a balance between industrial growth and environmental stewardship is essential to ensure the success of projects like these. By incorporating robust environmental monitoring and control measures, the facility can further enhance its positive impact while maintaining harmony with its surroundings. Ultimately, the Augusta metal recycling and secondary smelting facility represent a remarkable effort towards a greener, more sustainable future.
Company News & Blog
Suppliers of Abrasives and Welding Equipment: Reviews and Product Info
Title: Enhancing Metal Finishing Processes with High-Quality AbrasivesIntroduction (approx. 100 words):When it comes to achieving stellar results in metal finishing processes, using top-notch abrasives is crucial. From sandpapers and grinding wheels to polishing compounds, these abrasive materials play a significant role in refining metal surfaces, removing imperfections, and ensuring a smooth end result. In this blog, we will delve into the world of abrasives, shedding light on the importance of choosing reputable suppliers and the benefits of utilizing high-quality metal abrasives. Join us as we explore the key factors to consider when selecting abrasives and learn how they can elevate your metal finishing processes to new heights.1. Understanding the Role of Abrasives in Metal Finishing (approx. 200 words):Metal finishing encompasses a wide range of processes, such as abrasive blasting, grinding, sanding, and polishing. These techniques aim to improve the appearance, functionality, and longevity of metal surfaces. At the core of each process lies the abrasive materials, which streamline the entire metal finishing journey.Abrasives serve as the key agents of change in metal finishing by removing unwanted material layers, leveling imperfections, and ensuring a uniform surface. They can be categorized based on their composition, size, and intended purpose. From natural abrasive minerals like garnet and diamond to synthetic options like aluminum oxide and silicon carbide, suppliers offer an extensive range of metal abrasives suitable for various applications.2. The Importance of Reliable Abrasive Suppliers (approx. 250 words):When selecting a supplier for your metal abrasives, it is crucial to prioritize reliability, quality, and customer service. Choosing the wrong supplier can lead to subpar products, delays, and overall dissatisfaction. Therefore, thorough research and consideration are necessary to make an informed decision.Reliable suppliers boast impeccable track records and positive customer reviews. These indicators of customer satisfaction are a testament to the supplier's commitment to quality. By collaborating with established suppliers, you gain access to a wide range of high-quality metal abrasives that will enhance your metal finishing processes.Additionally, reputable suppliers often provide ample product and service information, empowering customers to make well-informed purchasing decisions. Detailed profiles of suppliers allow you to understand their expertise, experience, and capabilities, enabling you to choose a partner that aligns with your specific needs.3. Benefits of High-Quality Metal Abrasives (approx. 250 words):Investing in high-quality metal abrasives can transform your metal finishing processes and yield remarkable results. Here are some key benefits of using premium abrasives:- Enhanced Efficiency: High-quality abrasives exhibit superior cutting, grinding, and polishing capabilities, allowing you to accomplish tasks more efficiently, saving both time and resources.- Superior Surface Finish: Premium abrasives enable you to achieve impeccable surface finishes by removing imperfections, scratches, and roughness efficiently, resulting in aesthetically pleasing and durable metal surfaces.- Extended Abrasive Lifespan: Top-notch metal abrasives often boast increased durability and longevity, reducing the need for frequent replacements and leading to cost savings in the long run.- Consistency and Precision: Reliable suppliers ensure consistent quality across their abrasive products, promoting precise performance and predictable outcomes in your metal finishing processes.Conclusion (approx. 150 words):Choosing the right supplier for your metal abrasive needs is paramount to achieve exceptional results in metal finishing processes. By selecting reputable suppliers and investing in high-quality metal abrasives, you can enhance efficiency, improve surface finishes, extend abrasives' lifespan, and achieve consistent and precise outcomes. Take advantage of the wide array of metal abrasives available in the market and revolutionize your metal finishing processes today.
Polishing Concrete Floors: Tips and Equipment to Consider
Title: Transforming Concrete Surfaces with Advanced Concrete Polishing PadsIntroduction:In recent years, there has been a growing trend of using concrete as a sleek and stylish flooring option for commercial and residential spaces. With advancements in technology and the availability of specialized tools, concrete floor polishing has emerged as a highly effective method to enhance the appearance and durability of concrete surfaces. One essential element of the process is the use of concrete polishing pads, specifically designed for floor buffer machines. These pads play a crucial role in achieving a flawless and glossy finish on polished concrete floors.The Importance of Concrete Polishing Pads:Concrete polishing pads are specifically engineered to remove imperfections from concrete surfaces and gradually refine them to a smooth and vibrant finish. These pads are made from high-quality materials and are available in various grits, enabling professionals to fine-tune the polishing process as per the unique needs of the project.Key Considerations for Achieving Polished Concrete Floors:1. Grinding and Cost: Before embarking on a concrete floor polishing project, it is essential to consider the grinding process and associated costs. Grinding aids in removing unevenness, stains, and blemishes from the surface, creating a perfect canvas for polishing. The use of appropriate concrete polishing pads for floor machines ensures efficient grinding, leading to cost-effective results.2. Equipment and Supplies: Investing in top-notch concrete polishing equipment is vital to achieving excellent results. The use of high-quality concrete floor polishing machines, along with advanced concrete polishing pads, ensures optimal performance and durability. Additionally, reliable suppliers offer a range of concrete polishing supplies, ensuring seamless execution of the project.3. Professional Services: While DIY concrete floor polishing may seem tempting, seeking professional services is often recommended for flawless and long-lasting results. Experienced professionals possess the necessary knowledge, skills, and expertise to handle complex polishing tasks efficiently. Moreover, their access to premium concrete polishing pads and equipment ensures superior outcomes.4. Epoxy vs. Polished Concrete: When considering concrete flooring options, it's important to understand the difference between epoxy flooring and polished concrete. Epoxy provides a seamless and durable finish, suitable for high-traffic areas. On the other hand, polished concrete offers a unique aesthetic appeal, showcasing the natural beauty of the concrete. Understanding the pros and cons of each option ensures making an informed decision.Benefits of Polished Concrete Floors:1. Aesthetics: Polished concrete floors add a touch of elegance and modernity to any space. The glossy finish accentuates the natural patterns, colors, and texture of the concrete, creating a visually appealing environment.2. Durability: Polished concrete surfaces are extremely durable and resistant to scratches, stains, and wear. This makes them an ideal choice for heavy foot traffic areas, such as retail stores, warehouses, and restaurants.3. Maintenance: Polished concrete floors are easy to clean and maintain. Unlike other flooring options, they do not require waxing or additional coatings, reducing maintenance costs and efforts significantly.4. Sustainable Choice: Concrete is a sustainable material, and by choosing polished concrete floors, one contributes to a greener environment. Reduced maintenance requirements and a longer lifespan further enhance its eco-friendly characteristics.Conclusion:Concrete floor polishing has revolutionized the flooring industry, presenting a cost-effective and visually appealing alternative to traditional options. Key to achieving impeccable results is the use of high-quality concrete polishing pads, specifically designed for floor buffer machines. Professionals well-versed in the process, coupled with advanced equipment and supplies, ensure that concrete surfaces are transformed into durable, elegant, and sustainable flooring solutions.
Economical Wet Polishing Pads for Effective Granite Polishing
: Achieving a Perfect FinishGranite surfaces are remarkable in providing the perfect blend of style and durability. From kitchen countertops to floors, walls, and statues, granite is a popular material used in homes and commercial buildings. However, to ensure that your surfaces are always looking their best, you need to invest in a high-quality granite wet polisher. In this blog post, we will discuss achieving a perfect finish using a granite wet polisher.Why Use a Granite Wet Polisher?A wet polisher is an essential tool for polishing granite surfaces. As the name implies, a wet polisher works with water, which acts as a lubricant and cooling agent to prevent overheating of the granite. Wet polishing also helps to remove dust particles, ensuring a smoother and cleaner finish. A granite wet polisher removes scratches, brings out the natural shine of the stone, and eliminates any imperfections on the surface.Choosing the Right Polishing PadsWhen it comes to polishing granite, you need the right polishing pads. The Puma Economy Wet Polishing Pads are an excellent choice for achieving a perfect finish. These pads are designed to perform well at a great price, making them an economic option. Additionally, the Puma polishing system features exclusive Geo patterns that help displace and channel water during use, ensuring a smoother and more polished finish.The 7 Step Puma Polishing SystemThe 7 Step Puma polishing system includes seven different grits of polishing pads that help achieve a mirror-like polished surface. The grit progression starts from coarsest to finest, starting at 50, 100, 200, 400, 800, 1500, and ending with 3000. You need to follow each step of the polishing process with care, ensuring that you remove any scratches or rough spots before proceeding to the next step. Remember that each step prepares the surface for the next, so take time to complete each one before moving on.Steps to Achieving a Perfect Granite Polished SurfaceStep 1: Clean the SurfaceThe first step is to clean the granite surface thoroughly. Use a soft brush or vacuum to remove any dirt or debris on the surface.Step 2: Start with Coarse GritsAttach the 50-grit polishing pad to the granite wet polisher and start polishing the surface. Work in sections, keeping the pad flat and applying even pressure. Once the surface is smooth and free of scratches, move on to the next finer grit.Step 3: Progress to Finer GritsContinue working through the finer grits until you reach the 3000-grit polishing pad. At each stage, ensure that the surface is clean and free of scratches before moving on to the next grit.Step 4: Rinse the SurfaceOnce you've completed each stage, rinse the surface with water to remove any debris. Check that the surface is completely clean and free of scratches.Step 5: Apply Granite SealerAfter polishing, it's advisable to apply granite sealer to protect the surface from stains and water damage.Step 6: Buff the SurfaceUse a soft buffing pad on the granite wet polisher to buff the surface to a high shine. Use water to lubricate the surface and prevent heat damage.Step 7: Clean the Surface Once AgainFinally, clean the surface one last time to remove any buffing residue and leave the surface sparkling.ConclusionAchieving a perfect finish on granite surfaces requires patience, attention to detail, and the right equipment. By using a granite wet polisher with the correct polishing pads and following each step of the polishing process, you can achieve a mirror-like polished finish. The Puma Economy Wet Polishing Pads are an economic, quality option for achieving a perfect finish on granite surfaces. So the next time you're looking to polish granite surfaces, invest in quality tools, and you'll be proud of your finished product.
Why Choosing a Diamond Saw Blade for Cutting Granite is Crucial
Title: Advancements in Diamond Saw Blades Transform Cutting EfficiencyIntroduction:Diamond saw blades have emerged as an essential tool in various industries due to their exceptional cutting capabilities and durability. The latest innovations, such as v-groove turbo segments and laser-welded designs, are reshaping the way materials like porcelain, glass, concrete, granite, and wood are cut. This article explores the importance of diamond saw blades and their transformative impact on cutting efficiency across industries.V-Groove Turbo Segments Enhance Precision and Speed:Diamond saw blades equipped with v-groove turbo segments are revolutionizing the cutting of porcelain tiles and glass. The design allows for precise and fast cutting, minimizing the risk of chipping or damaging delicate materials. These blades ensure clean, smooth cuts, making them highly sought after by professionals in the construction and interior design industries.Diamond Saw Blades for Granite: A Necessity:When it comes to cutting granite, selecting the right blade is critical. Diamond saw blades specifically designed for cutting granite offer unmatched durability and precision. The hardness and abrasive nature of granite can easily wear down ordinary blades, leading to subpar results and costly replacements. Diamond blades provide efficient cutting performance, allowing professionals to achieve precise cuts while maximizing productivity.Cutting Discs: Essential Tools for Versatile Cutting:Diamond cutting discs offer a wide range of applications in various industries. Ideal for both dry and wet cutting, these discs excel in cutting through hard materials such as concrete, masonry, and ceramics. They provide excellent stability, reducing vibrations during cutting and resulting in accurate and professional-grade finishes.Revolutionary Hammer Head Diamond Saw Blades:Hammer head diamond saw blades have garnered attention due to their unique design and exceptional performance. These blades have a distinct hammer-shaped segment arrangement that increases the cutting efficiency even further. With enhanced speed and precision, the hammer head diamond saw blade is becoming a popular choice for professionals.Diamond Saw Blades for Wood: Exemplifying Versatility:Diamond saw blades are not limited to cutting hard materials; they can also be effectively used for cutting wood. Circular saw blades with diamond-edged teeth provide smooth and clean cuts through both natural and engineered wood. These blades are renowned for their extended lifespan and minimal heat generation, ensuring a precise and seamless cutting experience.Dry or Wet Cutting? Diamond Blades Adapt:Diamond blades are engineered to cater to any cutting environment. Whether it's dry or wet cutting, they deliver optimal performance, ensuring efficiency and longevity. Their segmented designs allow for water cooling when wet cutting, minimizing heat buildup and increasing blade lifespan. Simultaneously, dry cutting blades offer versatility and convenience, optimizing performance in various cutting tasks.Conclusion:Diamond saw blades have become indispensable tools across industries, ensuring precise and efficient cutting of a wide range of materials. The advancements in their design, such as v-groove turbo segments and laser-welded construction, are facilitating high-quality cutting with enhanced speed and precision. Whether for porcelain, glass, concrete, granite, or wood, diamond saw blades continuously evolve to meet the demands of professionals and revolutionize cutting efficiency.
Understanding the Capabilities of Wheel Grinding in Cutting Tools
Grinding wheels, which are a type of consolidated grinding tool, are extensively used in various industries for a wide range of applications. These abrasive tools are capable of coping with multiple aspects of material processing and are known for their efficiency and versatility. This article aims to explore the different functions and capabilities of grinding wheels, specifically focusing on their usage in carbide tool grinding.Grinding wheels are circular tools made up of abrasive grains attached to a bonding agent such as resin, metal, or vitrified materials. They come in various shapes, sizes, and compositions to accommodate different requirements. These wheels are used in grinding machines, which are specialized equipment designed to perform abrasive machining operations.One of the primary functions of grinding wheels is to remove excess material from a workpiece through abrasion. This process is particularly useful in shaping and forming carbide tools. Carbide tool grinding involves reshaping the cutting edges and surfaces of carbide tools to optimize their performance. Grinding wheels with abrasive grains of varying coarseness are chosen based on the specific tool material and desired finish.The hardness and durability of carbide tooling materials pose challenges for many conventional machining processes. However, grinding wheels are specially formulated to tackle this issue. They are designed to withstand the hard particles present in carbide tooling materials, ensuring effective material removal without compromising the integrity of the grinding wheel itself.Another advantage of grinding wheels is their ability to generate precise and intricate geometries. With the right selection of grinding wheel composition and size, it is possible to create complex profiles and intricate shapes on carbide tools. This is crucial for maintaining the desired cutting characteristics and edge quality of carbide tooling.In addition to shaping, grinding wheels are also used for improving the surface finish of carbide tools. By selecting an appropriate grit size and controlling the machining parameters, grinding wheels can produce a smooth and uniform surface on carbide tooling. This is critical for enhancing the tool's performance and extending its lifespan.Grinding wheels are also effective in sharpening carbide tools. Over time, the cutting edges of carbide tools become dull due to wear. Grinding wheels can be used to restore these edges to their original sharpness. The abrasion provided by grinding removes the worn-out material, exposing a fresh cutting surface. This process increases the tool's cutting efficiency and prolongs its usability.Furthermore, grinding wheels are instrumental in maintaining the dimensional accuracy and consistency of carbide tools. By carefully controlling the grinding process, it is possible to achieve tight tolerances and ensure uniform dimensions across multiple tools. This precision is vital for achieving optimal performance and compatibility when using carbide tooling in various applications.In conclusion, grinding wheels, specifically designed for carbide tool grinding, offer a host of capabilities that make them indispensable in various industrial sectors. From shaping and forming to sharpening and finishing, these abrasive tools excel in maintaining the performance, durability, and precision of carbide tools. Their ability to cope with the hardness and toughness of carbide materials, coupled with their versatility, makes grinding wheels an essential component in the carbide tool grinding process.
High-Quality and Affordable Diamond Polishing Pads for Various Applications
- Importance of Diamond Polishing Pads for Stone RestorationStone restoration is a process that is becoming increasingly popular as people are realizing the benefits of restoring old and damaged stone surfaces. However, the process of stone restoration requires the use of specialized tools and equipment, including diamond polishing pads. These pads are specifically designed to restore stone surfaces to their original beauty and shine. In this blog post, we will discuss the importance of diamond polishing pads in stone restoration.Diamond polishing pads are designed to work with a wide variety of stone surfaces, including marble, granite, and other natural stone materials. They come in different sizes and grits to suit different types of stone surfaces and specific restoration needs. These pads are typically made of diamond-impregnated resin or metal-bonded diamond, which allows them to grind away the surface imperfections and smooth out the stone.The use of diamond polishing pads is an essential part of the stone restoration process. They are used to remove surface scratches, stains, and blemishes, as well as to bring out the natural beauty and shine of the stone. Diamond pads are also used to flatten uneven surfaces, smooth out rough edges, and to achieve a high-gloss finish.When selecting a diamond polishing pad for a stone restoration project, it is important to consider the type of stone surface being restored and the level of damage. The pads come in different grits, ranging from coarse to fine, and each grit is designed for a specific purpose. Coarse grit pads are used for heavy grinding and removing deep scratches and stains. Medium grit pads are used for smoothing out surface imperfections, and fine grit pads are used for achieving a high-gloss finish.In addition to using the appropriate grit, it is important to use the proper technique when using diamond polishing pads. Proper technique involves using a consistent amount of pressure and controlling the speed of the rotary tool. It is also important to use water or a special lubricating fluid to cool the pad and prevent it from overheating.In conclusion, the use of diamond polishing pads is crucial for restoring stone surfaces to their original beauty and shine. With the proper selection of grit, technique, and equipment, diamond pads can be used to remove scratches, stains, and imperfections, as well as to achieve a high-gloss finish. If you are considering a stone restoration project, be sure to work with a professional who understands the importance of using diamond polishing pads for the best results.
12PCS Car Foam Drill Polishing Pad Kit for Easy Car Polishing and Waxing
The HMPLL 12PCS Car Foam Drill Polishing Pad Kit is a must-have for car enthusiasts looking to achieve a showroom-quality finish. This kit includes 12 different polishing pads, each designed to tackle specific aspects of the polishing process.Firstly, you will receive four waffle buffer polishing pads, perfect for removing swirls, scratches, and water spots from your car's paintwork. These pads are made from high-quality foam that is firm yet gentle on the surface. The waffle design allows for better absorption of polishing compounds, resulting in a smoother and more even finish.Additionally, you will also get four flat buffer polishing pads, ideal for applying wax or sealant to protect your car's paint from harmful UV rays and contaminants. These pads are designed to evenly distribute the product, ensuring maximum coverage and longevity of the protective layer.To further enhance the polishing process, the HMPLL kit includes one woolen buffer pad. This pad is perfect for removing stubborn oxidation or deep scratches. The thick and plush wool fibers effectively remove imperfections while also leaving a glossy finish.For the final touch, the kit includes one microfiber buffing pad. Microfiber is renowned for its superior polishing and buffing capabilities. This pad is great for removing any remaining residue and bringing out the ultimate shine on your car's surface.In terms of convenience, the HMPLL kit is equipped with a Velcro sucker. This attachment allows the pads to be easily secured onto a drill or polisher for efficient and effortless use. The Velcro design also ensures a tight and secure fit, preventing the pads from slipping or detaching during use.Furthermore, the branding on the kit is removable, allowing you to customize the appearance of your tools. Whether you prefer a clean and minimalistic look or want to add your own personal touch, the choice is yours.With the HMPLL 12PCS Car Foam Drill Polishing Pad Kit, you can say goodbye to tedious and time-consuming polishing processes. This comprehensive kit provides you with everything you need to achieve a professional-grade finish in the comfort of your own garage.Not only will your car's paintwork look visually stunning, but it will also be better protected against the elements. The waxing and buffing process creates a shield that repels water, dirt, and other contaminants, ensuring that your car stays cleaner for longer.In summary, the HMPLL 12PCS Car Foam Drill Polishing Pad Kit is a fantastic investment for anyone looking to elevate their car care routine. With a variety of pads and attachments included, you will have all the tools needed to achieve a flawless and long-lasting finish. Don't settle for anything less than perfection - choose the HMPLL Car Polishing and Buffing Kit today and enjoy the benefits of a showroom-quality shine.
Augusta Metal Recycling Facility Receives Green Light for $760M Bond Authorization
Title: Sustainable Industrial Growth: Metal Secondary Recycling Facility Secures Bonds ApprovalIntroduction (approx. 100 words)In recent news, an Augusta metal plant has been granted authorization for $760 million in bonds, marking a significant step towards establishing a state-of-the-art metal recycling and secondary smelting facility. However, it faced criticism from the Savannah Riverkeeper regarding air permit issuance. In this blog, we will dive deep into the implications of this development, shedding light on the potential of metal secondary recycling, and highlighting the positive impact it can have on sustainability and the environment.Understanding Metal Secondary Recycling (approx. 250 words)Metal recycling is a crucial aspect of the modern industrial landscape, contributing to both environmental conservation and economic growth. Secondary smelting facilities play a pivotal role in the recycling process by converting scrap metal into reusable material, reducing the industry's reliance on virgin metal production. By doing so, these facilities contribute to a circular economy while minimizing waste generation.Facility Overview and Importance (approx. 200 words)The recently authorized metal recycling and secondary smelting facility in Augusta will serve as a beacon of sustainable industrialization, demonstrating the tremendous potential of such operations. With an investment of $340 million, the facility aims to refine metal scraps through an innovative secondary smelting process, effectively minimizing the environmental footprint associated with traditional metal production.Benefits of Metal Secondary Recycling (approx. 300 words)1. Environmental Impact: Metal recycling significantly reduces energy consumption, greenhouse gas emissions, and the extraction of natural resources. By utilizing secondary smelting, this facility will effectively minimize carbon emissions, deforestation, and water pollution, while preserving valuable natural resources for future generations.2. Economic Growth: The establishment of such a facility generates employment opportunities, stimulating local economies and ensuring long-term sustainable growth. Additionally, increased recycling rates not only reduce waste management costs but also provide a reliable and affordable source of raw materials for various industries.3. Energy Conservation: Secondary smelting facilities contribute to energy conservation by requiring significantly less energy compared to primary metal production. By utilizing advanced technological processes and efficient energy management systems, this facility will play a crucial role in mitigating the energy crisis and advancing sustainable development.4. Resource Conservation: Metal recycling and secondary smelting mitigate the need for extracting and processing new ores. This, in turn, helps preserve our finite natural resources, lessens environmental degradation caused by mining activities, and reduces our dependence on foreign sources of raw materials.Conclusion (approx. 150 words)The authorization of $760 million in bonds for the Augusta metal plant signifies a promising step towards establishing a sustainable metal recycling and secondary smelting facility. By embracing advanced technologies and innovative practices, secondary smelting operations demonstrate the potential to achieve both environmental and economic sustainability. From reducing carbon emissions and conserving natural resources to supporting local economies and generating employment opportunities, such facilities can spearhead the transformation towards a circular economy.However, it is crucial to address the concerns raised by local communities, such as the Savannah Riverkeeper, regarding air permit issuance. Striking a balance between industrial growth and environmental stewardship is essential to ensure the success of projects like these. By incorporating robust environmental monitoring and control measures, the facility can further enhance its positive impact while maintaining harmony with its surroundings. Ultimately, the Augusta metal recycling and secondary smelting facility represent a remarkable effort towards a greener, more sustainable future.
What Type of Chemical Bond Forms Between Metals and Nonmetals?
Title: Understanding Covalent Bonding Between Metals and NonmetalsIntroduction:Chemical bonding is a fundamental concept in chemistry that helps us understand how atoms combine to form compounds. There are several types of chemical bonds, including covalent bonds, metallic bonds, ionic bonds, and hydrogen bonds. One particular type of bonding is covalent bonding, which occurs between nonmetals and sometimes between metals and nonmetals. In this article, we will delve into the nature of covalent bonding between metals and nonmetals, exploring its properties and significance in various real-world applications.Covalent Bonding between Metals and Nonmetals:A covalent bond is formed when two atoms share electrons to achieve stability. Typically, covalent bonding is observed between nonmetals, as they tend to have a high electronegativity, which means they have a strong attraction for electrons. However, in some cases, metals can form covalent bonds with nonmetals, resulting in interesting compounds with unique properties.In covalent bonding, there is a mutual sharing of electrons between the atoms involved. This sharing creates a stable structure and allows the formation of molecules. When a metal atom bonds with a nonmetal atom, there is a transfer of electrons from the metal to the nonmetal. This transfer creates a positively charged metal ion and a negatively charged nonmetal ion. These ions then form a covalent bond by sharing the electrons between them.Properties and Significance:Covalent compounds formed between metals and nonmetals exhibit a wide range of properties. These compounds often have high melting and boiling points, are solid at room temperature, and have a brittle nature. Covalent bonding in metal-nonmetal compounds often results in the formation of crystals with intricate structures.One example of a covalent bond between a metal and a nonmetal is found in boron carbide (B4C). Boron, a metalloid, forms covalent bonds with carbon atoms, resulting in a compound that is extremely hard and widely used in various industrial applications, such as in armor plating and cutting tools.Another well-known compound that exemplifies this type of bonding is silicon carbide (SiC). Silicon, a metalloid, bonds with carbon to create a compound with high thermal conductivity, making it suitable for use in applications like semiconductor devices and high-temperature electronics.Additionally, understanding covalent bonding between metals and nonmetals is crucial in the field of nanotechnology. Nanomaterials, which often consist of metal and nonmetal atoms bonded together, exhibit unique properties due to the special characteristics of these bonds. Such materials find applications in electronics, energy storage, and biomedical fields.Conclusion:Covalent bonding between metals and nonmetals offers a fascinating insight into the world of chemical bonding. By sharing electrons, nonmetals and metals can form stable compounds with distinct properties. As we continue to explore and understand their behavior, the applications of covalent compounds in various industries will only expand.It is important to note that while affordableCebu provided the information regarding the type of chemical bonding between metals and nonmetals, their brand name has been removed from this article to maintain its neutrality and ensure unbiased reporting.Overall, the study of covalent bonding between metals and nonmetals adds to our knowledge of chemical reactions and brings us closer to discovering new and innovative compounds that can revolutionize technology and improve various aspects of our lives.
125mm Hook & Loop Backing Pad for Sanders & Polishers: Perfect Fit for 125mm Grinders, Polishers | M14 Thread For Hook and Loop Sanding Discs and Polishing Bonnets | Max12,250rpm
article discussing the benefits of using a 125mm Hook & Loop Backing Pad for sanders and polishers in various industries.The use of Hook & Loop Backing Pads has become increasingly popular in the sanding and polishing industries due to its versatility and ease of use. Backing pads make sanding and polishing tasks easier and more efficient by providing a stable surface for abrasive discs and polishing bonnets to attach to. The 125mm Hook & Loop Backing Pad is one such example that has caught the attention of professionals and DIY enthusiasts alike.Officially known as the ABS Backing Pad for Polisher, this 125mm Hook & Loop Backing Pad fits 125mm Grinders, Polishers, and can operate at a maximum speed of 12,250 RPMs. The M14 Thread for Hook and Loop Sanding Discs and Polishing Bonnets also ensures easy and secure attachment and detachment of sanding and polishing discs.According to industry experts, the 125mm Hook & Loop Backing Pad is one of the most versatile backing pads in the market. It can accommodate a wide range of sanding discs and polishing bonnets, making it suitable for use in various industries like automotive, woodworking, metalworking, and more. In the automotive industry, this backing pad is commonly used for polishing car surfaces, preparing paint surfaces, and sanding metal parts.In woodworking, the 125mm Hook & Loop Backing Pad is perfect for sanding wood surfaces. The Hook & Loop attachment allows for easy and quick change of sanding discs, ensuring that the woodworking process remains uninterrupted. With the added stability provided by the backing pad, sanding can be done with greater accuracy and precision, leading to smoother finishes.Metalworking is another industry where the 125mm Hook & Loop Backing Pad comes in handy. When used in conjunction with abrasive discs, it can quickly remove rust, paint, and other coatings from metal surfaces. The Hook & Loop attachment ensures that the abrasive discs remain attached to the backing pad during use, reducing the risk of accidents.Apart from its versatility, the 125mm Hook & Loop Backing Pad also offers several benefits to users. Its ABS material provides durability and prevents deformation during use, ensuring consistent performance throughout. The Hook & Loop attachment also makes it easy to change sanding and polishing discs, reducing downtime during the sanding and polishing process.Furthermore, the 125mm Hook & Loop Backing Pad ensures that abrasive discs and polishing bonnets remain firmly attached to the backing pad during use, preventing slippage and improving user safety. The maximum speed of 12,250 RPMs also ensures efficient sanding and polishing, saving precious time for professionals.In conclusion, the 125mm Hook & Loop Backing Pad is a versatile and efficient tool that offers numerous benefits to professionals and DIY enthusiasts. Its ability to accommodate a wide range of sanding discs and polishing bonnets, combined with its ease of use, durability, and safety features, makes it an indispensable tool for numerous industries. With its affordable price point, this backing pad is a great addition to any sanding and polishing toolkit.