Essential Tools for Achieving a Perfect Granite Finish
By:Admin
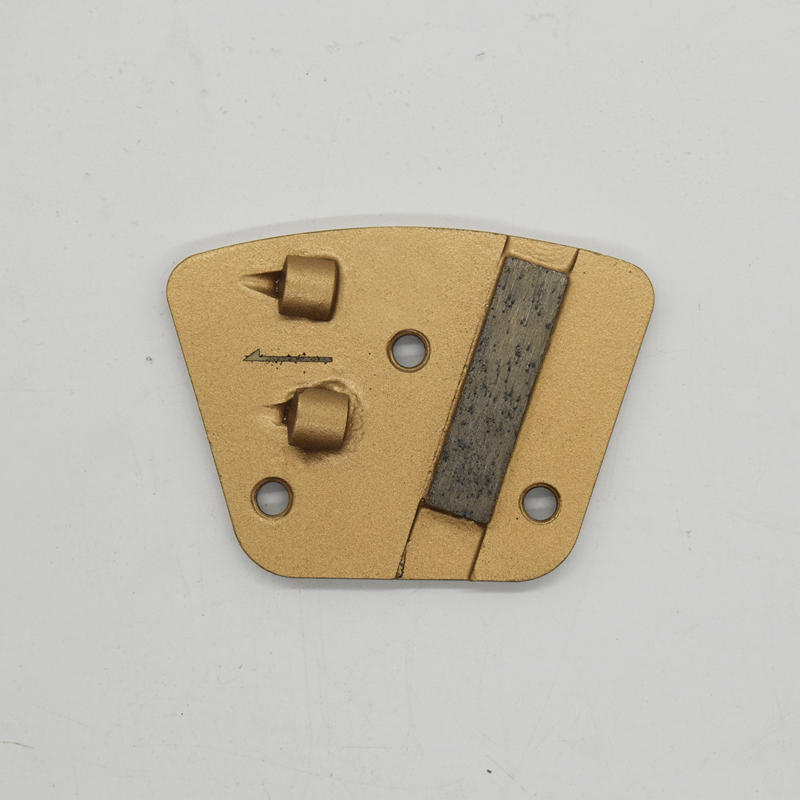
[City, Date] – Granite Finishing Tools, a leading provider of high-quality stone finishing equipment, is transforming the stone industry with its innovative range of products. With a focus on efficiency, precision, and durability, Granite Finishing Tools has emerged as the go-to solution for professionals working with granite and other natural stones.
Within a highly competitive market, Granite Finishing Tools has quickly gained recognition for its commitment to delivering top-notch tools that cater to the demanding needs of stone fabricators and craftsmen. The company's dedication to continuous research and development has allowed it to stay at the forefront of technological advancements in the industry.
With an extensive product line covering every aspect of stone finishing, Granite Finishing Tools offers a comprehensive solution for all stone fabrication processes. From cutting, grinding, polishing, to edge profiling, the company provides an array of tools designed to enhance productivity while achieving exceptional quality results.
One of the standout products in their range is the state-of-the-art diamond cutting blade. Known for its exceptional cutting speed and longevity, this blade transforms the cutting process, saving craftsmen time and effort. Furthermore, its superior performance ensures clean cuts with minimal chipping, resulting in a more efficient fabrication process.
Granite Finishing Tools has also revolutionized the polishing stage with its highly specialized line of diamond polishing pads. These pads are engineered to deliver an unmatched level of shine while minimizing heat generation. The company's innovative pad design allows for reduced polishing time, resulting in increased productivity and cost savings for fabricators.
Additionally, Granite Finishing Tools places a strong emphasis on safety in its product development. The company's range includes effective dust control systems that efficiently capture and remove harmful dust particles generated during stone processing. These systems not only protect the health of workers but also ensure a cleaner work environment, enhancing overall efficiency.
Recognizing the diverse needs of its customers, Granite Finishing Tools offers personalized toolkits tailored to specific requirements. This customer-centric approach allows fabricators to optimize their processes, resulting in improved outcomes and increased customer satisfaction.
With a commitment to customer support and satisfaction, Granite Finishing Tools provides comprehensive after-sales services, including technical assistance and training. By partnering with experienced professionals in the stone industry, the company ensures that fabricators can fully harness the potential of their tools and achieve outstanding results.
Granite Finishing Tools' dedication to quality is reflected in the materials used for manufacturing its products. With a meticulous selection process, the company sources only premium-grade raw materials, ensuring the durability and longevity of its tools. This commitment to quality is in alignment with the company's mission to provide professionals with reliable equipment that guarantees superior performance and longevity.
As Granite Finishing Tools expands its reach domestically and internationally, the company envisions a future where stone fabricators can maximize their efficiency and quality outputs with the aid of advanced tools. With a constant drive for innovation and excellence, Granite Finishing Tools remains at the forefront of the stone industry, empowering craftsmen to turn ordinary stone into remarkable works of art.
About Granite Finishing Tools:
Granite Finishing Tools is a leading provider of high-quality stone finishing equipment, offering a comprehensive range of tools designed to enhance productivity and deliver exceptional quality results. With a focus on innovation and customer satisfaction, Granite Finishing Tools aims to revolutionize the stone industry through cutting-edge technology and personalized solutions. For more information, please visit [company website].
Company News & Blog
Why customised cricket bats are gaining popularity among professional players
Title: Industry-Leading Sanding Solution Enhances Efficiency and Precision in Surface PreparationIntroduction:In an ever-evolving manufacturing landscape, companies are constantly on the lookout for innovative solutions to enhance their operations. As surface preparation continues to play a crucial role in various industries, renowned manufacturer has revolutionized the market with their cutting-edge sanding solution. Developed through years of research and technological expertise, this industry-leading product promises to deliver exceptional efficiency and precision in surface preparation processes.Paragraph 1:Surface preparation is a critical step in numerous industries, including woodworking, metalworking, automotive, and construction. Regardless of the application, achieving a flawless finish often involves sanding. Traditionally, sanding has been a time-consuming and labor-intensive process. However, the introduction of the revolutionary sanding solution by is set to change the game. Incorporating advanced materials and technology, their product offers a perfect balance of efficiency, effectiveness, and durability.Paragraph 2:One of the key distinguishing features of this sanding solution lies in its unique composition. Developed using a blend of high-quality abrasives and adhesive materials, the sandpaper exhibits exceptional durability and longevity. This ensures that the abrasive particles stay firmly attached to the backing material for extended periods, minimizing the need for frequent replacement. Customers can thus enjoy prolonged usage and cost savings, making it a highly sought-after choice in the market.Paragraph 3:Furthermore, the sandpaper's abrasive composition is designed to maximize efficiency in surface preparation. Each abrasive particle is precisely engineered to provide consistent and uniform sanding results. This results in an even removal of material and reduces the occurrence of imperfections such as scratches or uneven surfaces. Whether used for sanding wooden surfaces, smoothing metal edges, or preparing automotive parts, this solution guarantees superior outcomes.Paragraph 4:Additionally, the sandpaper's backing material is carefully selected to complement its abrasive capabilities. Constructed from a durable yet flexible material, it ensures optimal conformability to different surface contours. This feature is particularly crucial when working with intricate or curved surfaces, as it allows for efficient sanding without compromising precision. As a result, users can achieve consistent and professional finishes on a wide range of projects.Paragraph 5:In response to evolving customer needs and preferences, offers their sanding solution in a variety of grit options. Ranging from coarse to fine, these grits cater to different sanding requirements, ensuring versatility across industries. Whether it's initial surface removal, intermediate smoothing, or final finishing, users have the flexibility to choose the ideal grit for their intended application, maximizing time and efficiency.Paragraph 6:To enhance the user experience further, the sandpaper comes with a hook and loop (Velcro) backing system. This feature simplifies the sandpaper attachment and removal process, eliminating the need for adhesives or cumbersome setups. It enables quick and effortless exchanges between different grits or replacement of worn-out sandpaper, saving valuable time during projects.Paragraph 7:To meet the diverse demands of global markets, the sanding solution by is available in various sizes, allowing it to align with different tools and equipment. From handheld sanders to power sanders and even machine sanders, compatibility is ensured, enabling seamless integration into existing setups. This positions the product as an industry-standard for surface preparation across numerous sectors.Conclusion:As surface preparation continues to be a crucial aspect of manufacturing processes, the introduction of sanding solution revolutionizes efficiency, accuracy, and durability. With its advanced composition, superior abrasive performance, and innovation in backing material, this product sets new benchmarks in the industry. By catering to a wide range of grit options and offering a user-friendly hook and loop system, the solution ensures versatility and seamless integration across various tools. In conclusion, the sanding solution by proves to be a game-changer, providing companies across industries with an unparalleled surface preparation solution.
Versatile Grinding Wheels for Industrial Metal Work and Deburring Applications
s, Bonded Grinding Wheels, Industrial Applications, Metal Work, Deburring, Bench Mounted Applications, Surface Grinding Wheels, Carbide BurrsGrinding Wheels and Tooling for Industrial ApplicationsGrinding wheels are essential tools for metalworking, deburring, and machine-mounted works. They come in various shapes and sizes and are known to be one of the most versatile abrasive tools available in the market. They are made of abrasive grains, bonding materials, and fillers, and can be used for a wide range of tasks. In this article, we will discuss the different types of grinding wheels and tooling for industrial applications.Bonded Grinding WheelsBonded grinding wheels are the most commonly used type of grinding wheel. They are made of a composite material that consists of abrasive grains held together by a bonding material. The abrasive grains are usually made of aluminum oxide, silicon carbide, or diamond, depending on the type of material being ground and the desired finish. The bonding material can be resin, metal, or vitrified.Resin-bonded wheels are commonly used for precision grinding, surface grinding, and tool and cutter grinding. They are versatile and affordable, making them suitable for most applications. Metal-bonded wheels are used for grinding harder materials, such as high-speed steel and carbide. They are also used for rough grinding and form grinding. Vitrified-bonded wheels are used for precision grinding and sharpening of carbide tools.Wire BrushesWire brushes are another type of abrasive tool that is used for cleaning, deburring, and finishing metal surfaces. They are made of metal wire bristles that are mounted on a rotating shaft. The wire bristles can be made of different materials, including steel, brass, and stainless steel. Wire brushes are used for removing rust, paint, and other surface contaminants from metal surfaces. They are also used for cleaning welds and deburring edges.Bench Mounted ApplicationsBench-mounted grinding wheels are used for precision grinding, sharpening, and polishing of metal parts. They are mounted on a bench or pedestal and can be used for a wide range of tasks, such as grinding, deburring, and sanding. Bench-mounted wheels are available in various sizes and materials, depending on the application.Surface Grinding WheelsSurface grinding wheels are used for precision grinding of flat surfaces. They are typically used on a reciprocating table, where the workpiece is moved back and forth against the grinding wheel. Surface grinding wheels are available in different sizes and materials, depending on the type of material being ground and the desired finish.Carbide BurrsCarbide burrs are used for shaping, deburring, and finishing metal surfaces. They are made of carbide, a hard and brittle material that is ideal for grinding and cutting. Carbide burrs are available in various shapes and sizes, depending on the application. They can be used on a variety of materials, including steel, aluminum, and cast iron.In conclusion, grinding wheels and tooling for industrial applications are essential tools for metalworking, deburring, and machine-mounted works. Bonded grinding wheels, wire brushes, bench-mounted applications, surface grinding wheels, and carbide burrs are just some of the available options. When choosing a grinding wheel or tool, it is important to consider the type of material being ground, the desired finish, and the application.
Discover the Versatile Benefits of Lock Polishing Pads
article:Snail Lock Polishing Pad Revolutionizes Grinding and PolishingIn the world of grinding and polishing, efficiency and quality are two factors that cannot be compromised. Both are critical when it comes to achieving a perfect finish. One product that is quickly gaining traction in the industry is the Snail Lock Polishing Pad.Produced by a leading manufacturer of abrasives, the product is a game-changer in the world of grinding and polishing. It has been developed using the latest technology to ensure efficient and consistent grinding and polishing.The snail lock polishing pad is designed to work specifically with automatic edge polishing machines and bridge polishing machines equipped with the snail lock adapter. The pads are made from high-quality resin and diamond particles that make them durable and long-lasting. They are also easy to install and remove, making the grinding and polishing process quicker and more efficient.The unique design of the snail lock polishing pad consists of a double-layered resin and diamond grain structure that provides superior quality and consistent results. The single locking system ensures that the pad remains securely in place while in operation, reducing the risk of accidents and ensuring maximum safety for operators.According to the manufacturer, the snail lock polishing pad is suitable for use on a wide range of materials. These include natural stone, engineered stone, ceramics, and porcelain. This versatility makes it an indispensable tool for fabricators, contractors, and DIY enthusiasts.The snail lock polishing pad is also designed to reduce the need for multiple stages of grinding and polishing. Its superior quality means that it can deliver excellent results with minimal effort, time, and energy. This factor makes it a cost-effective solution for grinding and polishing professionals.The company behind the snail lock polishing pad has been in the business for over a decade and has built a strong reputation for producing high-quality abrasive products that meet the demands of the industry. Their team of experts includes experienced engineers, technicians, and customer service representatives who work tirelessly to ensure that their products are of superior quality and that they offer the best service to their clients.In addition to the snail lock polishing pad, the company produces a wide range of other abrasive products that cater to the needs of various industries. These products include diamond saw blades, diamond core bits, profiling wheels, and cup wheels, among others.The company believes that its success is driven by its commitment to quality and its willingness to go the extra mile to ensure customer satisfaction. This includes investing in research and development to improve its products' performance and quality continually.In conclusion, the snail lock polishing pad is a revolutionary product that is quickly gaining traction in the industry. Its unique design, efficiency, and durability make it a game-changer in the world of grinding and polishing. It is an indispensable tool for fabricators, contractors, and DIY enthusiasts looking for superior quality and consistent results. The manufacturer's commitment to quality and customer satisfaction make it a brand that customers can trust. With its continued investment in research and development, the company is poised to remain a leader in the abrasive products industry for years to come.
12PCS Car Foam Drill Polishing Pad Kit for Easy Car Polishing and Waxing
The HMPLL 12PCS Car Foam Drill Polishing Pad Kit is a must-have for car enthusiasts looking to achieve a showroom-quality finish. This kit includes 12 different polishing pads, each designed to tackle specific aspects of the polishing process.Firstly, you will receive four waffle buffer polishing pads, perfect for removing swirls, scratches, and water spots from your car's paintwork. These pads are made from high-quality foam that is firm yet gentle on the surface. The waffle design allows for better absorption of polishing compounds, resulting in a smoother and more even finish.Additionally, you will also get four flat buffer polishing pads, ideal for applying wax or sealant to protect your car's paint from harmful UV rays and contaminants. These pads are designed to evenly distribute the product, ensuring maximum coverage and longevity of the protective layer.To further enhance the polishing process, the HMPLL kit includes one woolen buffer pad. This pad is perfect for removing stubborn oxidation or deep scratches. The thick and plush wool fibers effectively remove imperfections while also leaving a glossy finish.For the final touch, the kit includes one microfiber buffing pad. Microfiber is renowned for its superior polishing and buffing capabilities. This pad is great for removing any remaining residue and bringing out the ultimate shine on your car's surface.In terms of convenience, the HMPLL kit is equipped with a Velcro sucker. This attachment allows the pads to be easily secured onto a drill or polisher for efficient and effortless use. The Velcro design also ensures a tight and secure fit, preventing the pads from slipping or detaching during use.Furthermore, the branding on the kit is removable, allowing you to customize the appearance of your tools. Whether you prefer a clean and minimalistic look or want to add your own personal touch, the choice is yours.With the HMPLL 12PCS Car Foam Drill Polishing Pad Kit, you can say goodbye to tedious and time-consuming polishing processes. This comprehensive kit provides you with everything you need to achieve a professional-grade finish in the comfort of your own garage.Not only will your car's paintwork look visually stunning, but it will also be better protected against the elements. The waxing and buffing process creates a shield that repels water, dirt, and other contaminants, ensuring that your car stays cleaner for longer.In summary, the HMPLL 12PCS Car Foam Drill Polishing Pad Kit is a fantastic investment for anyone looking to elevate their car care routine. With a variety of pads and attachments included, you will have all the tools needed to achieve a flawless and long-lasting finish. Don't settle for anything less than perfection - choose the HMPLL Car Polishing and Buffing Kit today and enjoy the benefits of a showroom-quality shine.
Revolutionary Floor Grinders that Mimic Manual Grinding Movements for Optimal Polishing
Title: Diamond Grinding Machine Floor: Revolutionizing Construction with Cutting-Edge TechnologyIntroduction Paragraph:In a bid to enhance efficiency and empower construction professionals, the groundbreaking Diamond Grinding Machine Floor presents a technological marvel that is set to redefine the industry standards. Its novel design effectively mimics the rocking sidetoside movements traditionally made manually by operators, making it a game-changer in the construction arena. Developed by Husqvarna, a globally recognized industry leader in providing construction solutions, the Diamond Grinding Machine Floor encompasses a wide range of machines and diamond tools, enabling professionals to leverage advanced technology for precision grinding and polishing.Body:1. Pioneering Technology for Enhanced Efficiency (100 words)The Diamond Grinding Machine Floor is equipped with cutting-edge technology, providing construction professionals with an unparalleled solution for their grinding and polishing needs. One of its standout features is its capability to seamlessly mimic the traditional sidetoside movements performed manually by operators. This unique feature eliminates the physical strain on operators, reducing fatigue and enhancing overall productivity. By automating this process, the Diamond Grinding Machine Floor ensures consistent and precise results, delivering a level of efficiency that was previously unattainable with traditional grinding machines.2. Three Main Benefits of Diamond Grinding Machine Floor (200 words)The Diamond Grinding Machine Floor offers three primary benefits that are set to revolutionize construction practices:a. Reduced Operator Fatigue: Traditional grinding machines require the operator to perform repetitive sidetoside movements manually. This repetitive motion can lead to fatigue and strain injuries. With the Diamond Grinding Machine Floor, operators can now experience reduced fatigue as the machine mimics the manual rocking movements, eliminating strain and optimizing overall operational efficiency.b. Superior Precision and Consistency: By automating the sidetoside movements, the Diamond Grinding Machine Floor ensures a consistently level and even grinding or polishing surface. This results in superior precision and a flawless finish, a crucial factor in meeting strict industry standards and client expectations.c. Increased Productivity: The automation of the rocking sidetoside movements provides an immense boost to productivity. Construction professionals can now accomplish more in less time, translating into improved profitability and quicker turnaround times for projects.3. The Support and Expertise of Husqvarna (150 words)The Diamond Grinding Machine Floor is an achievement brought to you by Husqvarna, a renowned name in the construction industry. Husqvarna has established itself as a leader in providing innovative solutions, including a diverse range of machines and diamond tools. Backed by decades of experience and a deep-rooted passion for excellence, Husqvarna offers complete support and service to construction professionals, helping them make the most of the Diamond Grinding Machine Floor. From consultation to training and ongoing assistance, Husqvarna stands as an unwavering partner for all construction needs. The company's commitment to delivering top-notch solutions, along with a focus on sustainable practices, has earned it a well-deserved reputation and the trust of professionals worldwide.4. Beyond Diamond Grinding Machine Floor: Husqvarna's Comprehensive Solutions (250 words)Husqvarna caters to a vast array of construction requirements, providing a comprehensive range of machines, diamond tools, and associated services. Their extensive portfolio encompasses cutting, grinding, and drilling equipment, along with advanced technologies for surface preparation and polishing. The company's commitment to pushing boundaries and meeting customer demands drives continuous innovation and elevates the industry standards. Husqvarna's diamond tools are designed to tackle all surfaces and materials, ensuring outstanding performance even in the most demanding conditions. With their relentless focus on research and development, Husqvarna consistently introduces groundbreaking designs, enabling professionals to achieve exceptional results.Additionally, Husqvarna's commitment towards sustainability is evident in their products. The Diamond Grinding Machine Floor, like many other machines, is designed to minimize energy consumption and reduce environmental impact. This environmentally conscious approach aligns with Husqvarna's vision of providing sustainable solutions that not only benefit the construction industry but also contribute to creating a greener future.Conclusion Paragraph:The Diamond Grinding Machine Floor by Husqvarna is a technological wonder that is set to reshape the construction landscape. With its ability to mimic sidetoside movements traditionally made manually, this innovative machine brings a newfound level of efficiency, precision, and productivity to the industry. Backed by Husqvarna's expertise, support, and comprehensive range of machines and diamond tools, construction professionals now have the means to achieve flawless results while reducing fatigue and maximizing their project's profitability. With the Diamond Grinding Machine Floor, Husqvarna continues to spearhead advancements in construction technology, revolutionizing the way professionals approach grinding and polishing tasks.
Borazon Grinding Wheels: A Comprehensive GuideWhen it comes to high-performance grinding, it's essential to use the right tools for the job. That's where Borazon grinding wheels come in. These wheels are made from cubic boron nitride (CBN), a material that is second only to diamond in terms of hardness. In this blog, we'll explore everything you need to know about Borazon grinding wheels, including their advantages, applications, and how to choose the right one for your needs.Advantages of Borazon Grinding WheelsThe main advantage of Borazon grinding wheels is their exceptional hardness. This makes them ideal for grinding hard materials that are difficult to process with traditional grinding wheels. Borazon wheels also have high abrasive resistance, which means they last longer and require less frequent replacement. Other advantages of these wheels include:• Excellent heat resistance: Borazon wheels can withstand high temperatures without cracking or degrading, making them ideal for applications that generate a lot of heat.• Superior surface finish: Borazon wheels create a smooth, precise surface finish that is free from burrs and other imperfections.• Versatile applications: Borazon wheels can be used to grind a wide range of materials, including hardened steels, cast iron, and superalloys.Applications of Borazon Grinding WheelsBorazon grinding wheels are used in a variety of applications, including:• Aerospace: Borazon wheels are used to grind turbine blades, engine parts, and other components used in the aerospace industry.• Automotive: These wheels are also used in the automotive industry to grind crankshafts, camshafts, and other engine components.• Medical: Borazon wheels are used to grind medical implants, such as hip replacements and dental implants, to ensure a precise fit.• Tool and die: These wheels can be used to grind cutting tools, such as drill bits, taps, and end mills, as well as dies and molds.Choosing the Right Borazon Grinding WheelChoosing the right Borazon grinding wheel depends on several factors, including the material you're grinding, the desired finish, and the type of machine you're using. Here are some tips to help you choose the right wheel:• Determine the hardness of the material you're grinding: Borazon wheels are best suited for grinding hard materials, so if you're grinding a soft material, you may want to consider a different type of wheel.• Consider the grit size: Borazon wheels come in a range of grit sizes, which determine how coarse or fine the abrasive particles are. Choose a finer grit for a smoother finish and a coarser grit for a more aggressive cut.• Check the compatibility with your machine: Make sure that the wheel you choose is compatible with your grinding machine. This includes checking the wheel diameter, arbor size, and maximum RPM.• Consult with a supplier: If you're unsure which wheel to choose, consult with a supplier who specializes in Borazon grinding wheels. They can help you determine the best option based on your specific needs.ConclusionBorazon grinding wheels are an essential tool for grinding hard materials to a precise finish. With their exceptional hardness, heat resistance, and abrasive resistance, these wheels offer many advantages over traditional grinding wheels. When choosing a Borazon wheel, consider the material you're grinding, the desired finish, and the compatibility with your machine. With the right wheel, you can achieve superior results and increase productivity in your grinding operations.
Discover the Strength of Metal Bonds: Which Alloys Are the Strongest?
Replace brand name with [Metal Manufacturer]Strongest Metal Bonds Combine with [Metal Manufacturer]'s Cutting-Edge Technology[City, Date] - [Metal Manufacturer], a leading global innovator in the field of metal engineering, announced today the development of a revolutionary technology that enables the creation of the strongest metal bonds ever seen. Leveraging their cutting-edge expertise, [Metal Manufacturer] has broken new ground, offering a game-changing solution for various industries that rely on durable metal structures. This groundbreaking achievement has the potential to redefine the way we think about metal bonds and revolutionize the world of engineering.[Metal Manufacturer] is renowned for its commitment to excellence and its relentless pursuit of technological advancement. With a highly experienced team of metallurgists and engineers, the company has continuously pushed the boundaries of what is possible in the field of metal fabrication. Now, they have taken a significant leap forward with their latest innovation: the creation of the strongest metal bonds to date.For decades, engineers and scientists have strived to develop metal bonds with unparalleled strength and durability. Existing bonding methods often fell short of meeting the demanding requirements of industries such as aerospace, automotive, and construction. [Metal Manufacturer]'s groundbreaking technology has changed the game entirely.The key to [Metal Manufacturer]'s success lies in their proprietary bonding process, which combines cutting-edge metallurgical techniques with state-of-the-art equipment. Through meticulous research and rigorous testing, their team has developed a method that enables the formation of incredibly strong metal-to-metal bonds. These bonds exhibit outstanding tensile strength, resistance to external forces, and long-term stability, surpassing anything previously achieved in the industry.The applications of this breakthrough technology are vast. In the aerospace industry, for instance, the ability to create reliable metal bonds is crucial. The newly developed bonds by [Metal Manufacturer] open doors for the production of lightweight yet robust components for aircraft and spacecraft, leading to enhanced fuel efficiency and improved performance. Similarly, the automotive sector can tap into this innovation to develop safer vehicles with strengthened structural integrity.Moreover, this advancement has the potential to revolutionize the construction industry. By implementing [Metal Manufacturer]'s technology, builders and architects could construct buildings, bridges, and other infrastructure with increased durability and resilience, ensuring their longevity even in harsh environmental conditions. This breakthrough can significantly reduce maintenance costs and increase the safety of critical structures."We are extremely proud of the progress we have made in creating the strongest metal bonds ever achieved," remarked [Spokesperson], a senior engineer at [Metal Manufacturer]. "This breakthrough is the result of years of dedicated research, and we believe it will have a transformative impact on various industries. From aerospace to automotive, our technology will enable engineers to push boundaries and usher in a new era of durability and reliability."The groundbreaking innovation by [Metal Manufacturer] also comes at a critical time of growing momentum in sustainable engineering. With a strong focus on environmental responsibility, [Metal Manufacturer]'s technology offers the potential to reduce waste and enhance resource efficiency. By creating stronger, more durable metal bonds, products built with this technology will have a longer life span, reducing the need for frequent replacements and, consequently, minimizing the environmental footprint.[Metal Manufacturer] plans to license this technology to industry partners across the globe, ensuring widespread access to this groundbreaking innovation. The company invites interested parties to get in touch to explore potential collaborations and discuss opportunities for adoption in a wide range of sectors.In conclusion, [Metal Manufacturer]'s breakthrough in creating the strongest metal bonds ever seen is set to revolutionize various industries. The technology's potential impact cannot be overstated, from creating safer aircraft and more durable cars to constructing resilient infrastructure. Moreover, the innovation aligns with the increasing focus on sustainability, offering a solution that reduces waste and enhances resource efficiency. [Metal Manufacturer] continues to push the boundaries of what is possible in metal engineering, setting new standards for durability and reliability in the process.
Understanding the Capabilities of Wheel Grinding in Cutting Tools
Grinding wheels, which are a type of consolidated grinding tool, are extensively used in various industries for a wide range of applications. These abrasive tools are capable of coping with multiple aspects of material processing and are known for their efficiency and versatility. This article aims to explore the different functions and capabilities of grinding wheels, specifically focusing on their usage in carbide tool grinding.Grinding wheels are circular tools made up of abrasive grains attached to a bonding agent such as resin, metal, or vitrified materials. They come in various shapes, sizes, and compositions to accommodate different requirements. These wheels are used in grinding machines, which are specialized equipment designed to perform abrasive machining operations.One of the primary functions of grinding wheels is to remove excess material from a workpiece through abrasion. This process is particularly useful in shaping and forming carbide tools. Carbide tool grinding involves reshaping the cutting edges and surfaces of carbide tools to optimize their performance. Grinding wheels with abrasive grains of varying coarseness are chosen based on the specific tool material and desired finish.The hardness and durability of carbide tooling materials pose challenges for many conventional machining processes. However, grinding wheels are specially formulated to tackle this issue. They are designed to withstand the hard particles present in carbide tooling materials, ensuring effective material removal without compromising the integrity of the grinding wheel itself.Another advantage of grinding wheels is their ability to generate precise and intricate geometries. With the right selection of grinding wheel composition and size, it is possible to create complex profiles and intricate shapes on carbide tools. This is crucial for maintaining the desired cutting characteristics and edge quality of carbide tooling.In addition to shaping, grinding wheels are also used for improving the surface finish of carbide tools. By selecting an appropriate grit size and controlling the machining parameters, grinding wheels can produce a smooth and uniform surface on carbide tooling. This is critical for enhancing the tool's performance and extending its lifespan.Grinding wheels are also effective in sharpening carbide tools. Over time, the cutting edges of carbide tools become dull due to wear. Grinding wheels can be used to restore these edges to their original sharpness. The abrasion provided by grinding removes the worn-out material, exposing a fresh cutting surface. This process increases the tool's cutting efficiency and prolongs its usability.Furthermore, grinding wheels are instrumental in maintaining the dimensional accuracy and consistency of carbide tools. By carefully controlling the grinding process, it is possible to achieve tight tolerances and ensure uniform dimensions across multiple tools. This precision is vital for achieving optimal performance and compatibility when using carbide tooling in various applications.In conclusion, grinding wheels, specifically designed for carbide tool grinding, offer a host of capabilities that make them indispensable in various industrial sectors. From shaping and forming to sharpening and finishing, these abrasive tools excel in maintaining the performance, durability, and precision of carbide tools. Their ability to cope with the hardness and toughness of carbide materials, coupled with their versatility, makes grinding wheels an essential component in the carbide tool grinding process.
Different Types of Grinding Wheel Dressers: A Comprehensive Guide
Grinding Wheel Dresser Types: Enhancing Efficiency and Precision in ManufacturingIn today's rapidly advancing manufacturing industry, efficiency and precision are of paramount importance. One of the key tools used for achieving these goals is the grinding wheel dresser. A grinding wheel dresser is a vital device used to shape and clean abrasive wheels in order to maintain their optimal performance. With various types of grinding wheel dressers available in the market, companies are constantly seeking the most appropriate type to enhance productivity and quality. Grinding wheel dressers come in different forms and serve unique purposes. One popular type is the diamond dresser. Incorporating diamond grains on its surface, this dresser offers unparalleled hardness and durability. Diamonds are known for their exceptional strength in cutting, shaping, and cleaning abrasive materials, making them the ideal choice for grinding wheel dressers. By utilizing diamonds, the dresser is able to maintain its sharpness even after extensive use, resulting in consistent and precise grinding.Another commonly used grinding wheel dresser is the star dresser. This type features multiple hardened steel discs with raised points in a star-like pattern. These points, often made from either high-speed steel or carbide, are crucial for truing and straightening the grinding wheel. The star dresser works by cutting into the wheel surface, creating grooves and channels, which ultimately improve its cutting efficiency and provide a smoother grinding action. This type of dresser is highly effective for removing excess material on the grinding wheel and achieving the desired shape.Yet another important type of grinding wheel dresser is the dressing stick or block. This dresser is made of abrasive grains, typically silicon carbide or aluminum oxide, adhered together with a bonding agent. The dressing stick is primarily used for cleaning and reshaping the grinding wheel by removing any debris or unevenness. It is especially useful in removing built-up metal shavings, known as glazing, which can significantly decrease the wheel's effectiveness. The dressing stick is an economical option that ensures the grinding wheel remains in optimal condition for prolonged usage.In light of these various grinding wheel dresser types, manufacturers are constantly seeking the most suitable option for their specific needs. This is where the company {}, a renowned leader in manufacturing solutions, comes into play. With a wealth of experience and expertise in the field, {} offers a wide range of grinding wheel dressers that cater to diverse industrial requirements.For instance, {} specializes in producing diamond dressers that are not only highly durable but also available in different sizes and shapes to accommodate various grinding wheel specifications. With their diamond dressers, customers can expect improved grinding efficiency, reduced dressing times, and increased precision in their manufacturing processes. By adopting diamond dressers from {}, manufacturers can achieve higher productivity, prolonged tool life, and enhanced overall quality.Furthermore, {} also offers an extensive selection of star dressers that can effectively dress a wide range of abrasive wheels, including vitrified, resin-bonded, and diamond grinding wheels. The company's star dressers are made from premium-quality materials, ensuring long-lasting performance and excellent truing capabilities. By utilizing {}'s star dressers, manufacturers can achieve optimal wheel conditions, resulting in enhanced surface finishes and reduced cycle times in their operations.Additionally, {} provides a comprehensive range of dressing sticks that are tailor-made for different grinding wheel materials and applications. Through their selection of dressing sticks, manufacturers can maintain the sharpness and efficiency of their grinding wheels, leading to consistent and precise results. {}'s dressing sticks are known for their durability and cost-effectiveness, making them a reliable solution in the grinding industry.In conclusion, grinding wheel dressers play a crucial role in maintaining the effectiveness and precision of abrasive grinding wheels. With a variety of types available, ranging from diamond dressers to star dressers and dressing sticks, manufacturers have multiple options to choose from based on their specific needs. By utilizing high-quality grinding wheel dressers from {}, companies can significantly enhance their manufacturing efficiency, improve product quality, and stay at the forefront of the rapidly evolving industry.