Discover the Many Uses and Benefits of an 800 Grit Polishing Pad
By:Admin
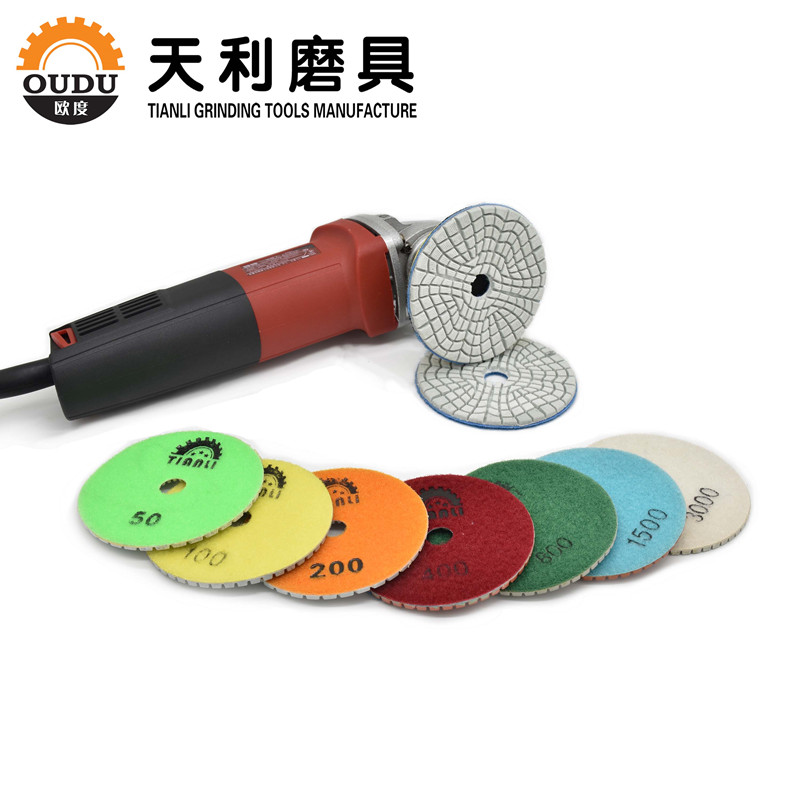
Introduction:
In today's fast-paced world, where appearances matter immensely, maintaining the shine and luster of our prized possessions has become crucial. In this regard, the introduction of the remarkable 800 Grit Polishing Pad brings a revolutionary change to the polishing industry. This cutting-edge product, developed by a leading technology company, promises to redefine the way we approach polishing, delivering impeccable results and unleashing the potential to transform the appearance of various surfaces.
Product Features and Benefits:
The 800 Grit Polishing Pad is a state-of-the-art product that leverages advanced technology and superior materials to revolutionize the polishing process. This pad has been meticulously designed to withstand the rigors of multi-surface polishing, making it ideal for use on automobiles, boats, and household items.
1. High-Quality Materials:
The 800 Grit Polishing Pad is constructed using the finest materials available, ensuring durability and long-lasting effectiveness. The pad's premium quality delivers outstanding results, leaving surfaces with a remarkable shine.
2. Efficiency and Versatility:
This polishing pad showcases exceptional efficiency, allowing users to achieve flawlessly shiny surfaces with ease. Its versatility extends to various applications, making it suitable for polishing plastic, wood, metal, and even glass.
3. Unique Grit Size:
The 800 grit represents the pad's abrasiveness, striking the perfect balance between coarseness and effectiveness. This proprietary grit size ensures optimal polishing, removing defects and imperfections without causing damage to the surface material.
4. Easy to Use:
To facilitate user convenience, the 800 Grit Polishing Pad is designed for effortless attachment to a variety of polishing tools. Its lightweight design allows for comfortable handling, ensuring a seamless polishing experience for both professionals and hobbyists.
Company Overview:
Committed to delivering groundbreaking technological solutions, the company behind the development of the 800 Grit Polishing Pad has an illustrious track record. As an industry leader in manufacturing and innovation, they have consistently pushed boundaries and delivered products that transform the way we approach polishing and surface maintenance.
With a team of dedicated engineers and product designers, the company aims to revolutionize the industry by constantly staying ahead of the curve. Their commitment to research and development ensures that end-users benefit from cutting-edge advancements in surface care technology.
Environmental Responsibility:
The company takes pride in its commitment to environmental sustainability. It follows stringent sustainability practices and regulations throughout the production process, ensuring that the 800 Grit Polishing Pad is eco-friendly. Minimizing waste, reducing energy consumption, and utilizing recyclable materials are just a few examples of the company's dedication to preserving the planet.
Market Response and Industry Impact:
Since its introduction to the market, the 800 Grit Polishing Pad has garnered considerable attention from professionals and enthusiasts alike. The product's exceptional performance and unparalleled results have quickly solidified its reputation as a game-changer in the polishing industry.
Polishing professionals praise the ease of use and the pad's ability to deliver consistent, top-tier results across various surfaces. Enthusiasts find its versatility appealing, as they can achieve professional-grade shine from the comfort of their own homes. Consequently, demand for the 800 Grit Polishing Pad is soaring, and the industry is taking notice.
Looking Ahead:
As the 800 Grit Polishing Pad continues to make waves in the market, the company is already working on expanding the product line and introducing new polishing solutions to meet growing consumer demand. Further advancements in their cutting-edge technology are expected to push the boundaries of what is possible, ultimately transforming the way we approach surface polishing.
Conclusion:
The revolutionary 800 Grit Polishing Pad has emerged as a game-changer in the industry, providing professionals and enthusiasts with a groundbreaking solution for achieving impeccable shine. With its advanced technology, unparalleled efficiency, and commitment to environmental sustainability, this product marks a turning point in the world of polishing. As the company behind it continues to innovate, the future looks bright for both the industry and those seeking to enhance the appearance of their prized possessions.
Company News & Blog
Economical Wet Polishing Pads for Effective Granite Polishing
: Achieving a Perfect FinishGranite surfaces are remarkable in providing the perfect blend of style and durability. From kitchen countertops to floors, walls, and statues, granite is a popular material used in homes and commercial buildings. However, to ensure that your surfaces are always looking their best, you need to invest in a high-quality granite wet polisher. In this blog post, we will discuss achieving a perfect finish using a granite wet polisher.Why Use a Granite Wet Polisher?A wet polisher is an essential tool for polishing granite surfaces. As the name implies, a wet polisher works with water, which acts as a lubricant and cooling agent to prevent overheating of the granite. Wet polishing also helps to remove dust particles, ensuring a smoother and cleaner finish. A granite wet polisher removes scratches, brings out the natural shine of the stone, and eliminates any imperfections on the surface.Choosing the Right Polishing PadsWhen it comes to polishing granite, you need the right polishing pads. The Puma Economy Wet Polishing Pads are an excellent choice for achieving a perfect finish. These pads are designed to perform well at a great price, making them an economic option. Additionally, the Puma polishing system features exclusive Geo patterns that help displace and channel water during use, ensuring a smoother and more polished finish.The 7 Step Puma Polishing SystemThe 7 Step Puma polishing system includes seven different grits of polishing pads that help achieve a mirror-like polished surface. The grit progression starts from coarsest to finest, starting at 50, 100, 200, 400, 800, 1500, and ending with 3000. You need to follow each step of the polishing process with care, ensuring that you remove any scratches or rough spots before proceeding to the next step. Remember that each step prepares the surface for the next, so take time to complete each one before moving on.Steps to Achieving a Perfect Granite Polished SurfaceStep 1: Clean the SurfaceThe first step is to clean the granite surface thoroughly. Use a soft brush or vacuum to remove any dirt or debris on the surface.Step 2: Start with Coarse GritsAttach the 50-grit polishing pad to the granite wet polisher and start polishing the surface. Work in sections, keeping the pad flat and applying even pressure. Once the surface is smooth and free of scratches, move on to the next finer grit.Step 3: Progress to Finer GritsContinue working through the finer grits until you reach the 3000-grit polishing pad. At each stage, ensure that the surface is clean and free of scratches before moving on to the next grit.Step 4: Rinse the SurfaceOnce you've completed each stage, rinse the surface with water to remove any debris. Check that the surface is completely clean and free of scratches.Step 5: Apply Granite SealerAfter polishing, it's advisable to apply granite sealer to protect the surface from stains and water damage.Step 6: Buff the SurfaceUse a soft buffing pad on the granite wet polisher to buff the surface to a high shine. Use water to lubricate the surface and prevent heat damage.Step 7: Clean the Surface Once AgainFinally, clean the surface one last time to remove any buffing residue and leave the surface sparkling.ConclusionAchieving a perfect finish on granite surfaces requires patience, attention to detail, and the right equipment. By using a granite wet polisher with the correct polishing pads and following each step of the polishing process, you can achieve a mirror-like polished finish. The Puma Economy Wet Polishing Pads are an economic, quality option for achieving a perfect finish on granite surfaces. So the next time you're looking to polish granite surfaces, invest in quality tools, and you'll be proud of your finished product.
Discover Laser and Water Cutting: How It Works and Its Uses in Manufacturing and Engineering
Cutting is a widely used process in the manufacturing industry that involves the separation of materials into smaller pieces. There are several methods of cutting available, including sawing, milling, and drilling, but perhaps the most popular and efficient processes are laser cutting and water cutting.Both laser cutting and water cutting are computer-controlled methods that utilize high-tech systems to slice through materials with precision and speed. Here’s a closer look at how each of these processes works:Laser CuttingLaser cutting uses a high-powered laser beam to cut through materials such as metals, plastic, wood, and ceramics. The laser beam is directed by computer-controlled mirrors onto the material to be cut. The beam creates a localized area of intense heat that melts or vaporizes the material. The laser beam is then moved across the material to create the desired pattern or shape.One of the advantages of laser cutting is its high precision. Laser cutters are capable of cutting complex shapes with ultra-fine details. They can create sharp corners and intricate designs with minimal burring. Laser cutting is also faster and more efficient than traditional cutting methods.Laser cutting is used in a variety of applications, including industrial manufacturing, aerospace, automotive, medical, and electronics. It is ideal for cutting thin materials, and it can cut through a wide range of thicknesses, from a few micrometers to several centimeters. Laser cutting is also great for cutting reflective materials such as metals, which can be difficult to cut with traditional methods.Water CuttingWater cutting, also known as waterjet cutting, is a process that uses a high-pressure water stream to cut through materials. The water is pressurized to between 30,000 and 90,000 psi and then accelerated through a small orifice. The fast-moving water stream is then directed onto the material to be cut, typically through a nozzle.Waterjet cutting does not generate heat, making it ideal for cutting materials that are sensitive to heat, such as plastic, rubber, and foam. It can also cut through thick materials, up to several inches thick, with ease. Waterjet cutting is versatile and can be used with a variety of materials, including metals, stone, glass, and composites.One of the benefits of water cutting is its ability to cut through a wide range of materials without distorting or changing their properties. It can also cut through materials with irregular shapes and sizes. Water cutting is an environmentally-friendly process and does not generate any hazardous waste.ConclusionCutting is a crucial process in the manufacturing industry, and laser cutting and water cutting are two of the most efficient and versatile methods of cutting available today. Laser cutting uses a high-powered laser beam to cut through materials, while water cutting uses a high-pressure water stream. Both methods are computer-controlled and are ideal for cutting a wide range of materials and thicknesses. Cutting saw and other traditional cutting methods are still in use but these two advanced methods offer greater precision and speed for modern manufacturing needs.
New Polishing Pad Provides Exceptional Results for Auto Detailing
Hard Polishing Pad: The Ultimate Solution for Exceptional Polishing PerformanceHong Kong - Hard Polishing Pad is the latest revolutionary product from one of the leading manufacturers and suppliers of polishing pads. With proven track records in producing high-quality products, the company has continued to strive hard to meet the ever-increasing demands of the market. The company is dedicated to providing customers with a wide range of innovative polishing pads that can offer optimal performance and durability. The new hard polishing pad is no exception. For customers who are looking for perfectly polished surfaces of various materials, Hard Polishing Pad is the ultimate solution that they can trust. The product is designed using the latest and most advanced technology to offer the best performance. The pad is manufactured using a unique process that makes it highly effective in polishing a wide range of surfaces, including granite, quartz, concrete, and marble. Hard Polishing Pad is a must-have for anyone who desires a smooth, polished, and mirror-like finish.The product is made from high-quality materials that are highly durable and long-lasting. The company has invested a considerable amount of time and resources in research and development to ensure that the product is of the highest quality. The result is a product that is not only highly effective but also very reliable. Hard Polishing Pad is designed to last a long time, which makes it ideal for both commercial and residential use.One of the unique features of Hard Polishing Pad is its superior performance. It has a much higher polishing ability compared to other polishing pads in the market. Using Hard Polishing Pad guarantees an exceptional polish, leaving the surface looking brand new. With the pad's superior performance, users can achieve impressive results in a shorter time than using traditional polishing methods.Another benefit of Hard Polishing Pad is its versatility. The product can polish a variety of surfaces, making it a perfect tool for professionals in the stone and concrete industry. Hard Polishing Pad can be used with different types of machines, including grinding machines, polishing machines, and floor machines. The pad is designed to work seamlessly with these machines, providing users with the flexibility they need.Hard Polishing Pad is also very user-friendly and easy to use. The product is made with a user-friendly design that can be used by both professionals and beginners. The pad is straightforward to attach and remove, and its design allows professionals to work on surfaces of different shapes and sizes. The product also comes with a detailed user manual that guides users on how to use it properly.In conclusion, Hard Polishing Pad is an exceptional product that offers the best performance and durability in the market. The product is perfect for anyone who desires a high-quality polish on various surfaces. Hard Polishing Pad is made from high-quality materials that assure users of its long-lasting performance. The pad's versatility gives users the flexibility they need to polish different surfaces, making it ideal for professionals in the stone and concrete industry. The product is also very user-friendly and easy to use, perfect for both beginners and professionals. Get your Hard Polishing Pad today and get to experience perfection in polishing surfaces.
Revolutionary Floor Grinders that Mimic Manual Grinding Movements for Optimal Polishing
Title: Diamond Grinding Machine Floor: Revolutionizing Construction with Cutting-Edge TechnologyIntroduction Paragraph:In a bid to enhance efficiency and empower construction professionals, the groundbreaking Diamond Grinding Machine Floor presents a technological marvel that is set to redefine the industry standards. Its novel design effectively mimics the rocking sidetoside movements traditionally made manually by operators, making it a game-changer in the construction arena. Developed by Husqvarna, a globally recognized industry leader in providing construction solutions, the Diamond Grinding Machine Floor encompasses a wide range of machines and diamond tools, enabling professionals to leverage advanced technology for precision grinding and polishing.Body:1. Pioneering Technology for Enhanced Efficiency (100 words)The Diamond Grinding Machine Floor is equipped with cutting-edge technology, providing construction professionals with an unparalleled solution for their grinding and polishing needs. One of its standout features is its capability to seamlessly mimic the traditional sidetoside movements performed manually by operators. This unique feature eliminates the physical strain on operators, reducing fatigue and enhancing overall productivity. By automating this process, the Diamond Grinding Machine Floor ensures consistent and precise results, delivering a level of efficiency that was previously unattainable with traditional grinding machines.2. Three Main Benefits of Diamond Grinding Machine Floor (200 words)The Diamond Grinding Machine Floor offers three primary benefits that are set to revolutionize construction practices:a. Reduced Operator Fatigue: Traditional grinding machines require the operator to perform repetitive sidetoside movements manually. This repetitive motion can lead to fatigue and strain injuries. With the Diamond Grinding Machine Floor, operators can now experience reduced fatigue as the machine mimics the manual rocking movements, eliminating strain and optimizing overall operational efficiency.b. Superior Precision and Consistency: By automating the sidetoside movements, the Diamond Grinding Machine Floor ensures a consistently level and even grinding or polishing surface. This results in superior precision and a flawless finish, a crucial factor in meeting strict industry standards and client expectations.c. Increased Productivity: The automation of the rocking sidetoside movements provides an immense boost to productivity. Construction professionals can now accomplish more in less time, translating into improved profitability and quicker turnaround times for projects.3. The Support and Expertise of Husqvarna (150 words)The Diamond Grinding Machine Floor is an achievement brought to you by Husqvarna, a renowned name in the construction industry. Husqvarna has established itself as a leader in providing innovative solutions, including a diverse range of machines and diamond tools. Backed by decades of experience and a deep-rooted passion for excellence, Husqvarna offers complete support and service to construction professionals, helping them make the most of the Diamond Grinding Machine Floor. From consultation to training and ongoing assistance, Husqvarna stands as an unwavering partner for all construction needs. The company's commitment to delivering top-notch solutions, along with a focus on sustainable practices, has earned it a well-deserved reputation and the trust of professionals worldwide.4. Beyond Diamond Grinding Machine Floor: Husqvarna's Comprehensive Solutions (250 words)Husqvarna caters to a vast array of construction requirements, providing a comprehensive range of machines, diamond tools, and associated services. Their extensive portfolio encompasses cutting, grinding, and drilling equipment, along with advanced technologies for surface preparation and polishing. The company's commitment to pushing boundaries and meeting customer demands drives continuous innovation and elevates the industry standards. Husqvarna's diamond tools are designed to tackle all surfaces and materials, ensuring outstanding performance even in the most demanding conditions. With their relentless focus on research and development, Husqvarna consistently introduces groundbreaking designs, enabling professionals to achieve exceptional results.Additionally, Husqvarna's commitment towards sustainability is evident in their products. The Diamond Grinding Machine Floor, like many other machines, is designed to minimize energy consumption and reduce environmental impact. This environmentally conscious approach aligns with Husqvarna's vision of providing sustainable solutions that not only benefit the construction industry but also contribute to creating a greener future.Conclusion Paragraph:The Diamond Grinding Machine Floor by Husqvarna is a technological wonder that is set to reshape the construction landscape. With its ability to mimic sidetoside movements traditionally made manually, this innovative machine brings a newfound level of efficiency, precision, and productivity to the industry. Backed by Husqvarna's expertise, support, and comprehensive range of machines and diamond tools, construction professionals now have the means to achieve flawless results while reducing fatigue and maximizing their project's profitability. With the Diamond Grinding Machine Floor, Husqvarna continues to spearhead advancements in construction technology, revolutionizing the way professionals approach grinding and polishing tasks.
Versatile Grinding Wheels for Industrial Metal Work and Deburring Applications
s, Bonded Grinding Wheels, Industrial Applications, Metal Work, Deburring, Bench Mounted Applications, Surface Grinding Wheels, Carbide BurrsGrinding Wheels and Tooling for Industrial ApplicationsGrinding wheels are essential tools for metalworking, deburring, and machine-mounted works. They come in various shapes and sizes and are known to be one of the most versatile abrasive tools available in the market. They are made of abrasive grains, bonding materials, and fillers, and can be used for a wide range of tasks. In this article, we will discuss the different types of grinding wheels and tooling for industrial applications.Bonded Grinding WheelsBonded grinding wheels are the most commonly used type of grinding wheel. They are made of a composite material that consists of abrasive grains held together by a bonding material. The abrasive grains are usually made of aluminum oxide, silicon carbide, or diamond, depending on the type of material being ground and the desired finish. The bonding material can be resin, metal, or vitrified.Resin-bonded wheels are commonly used for precision grinding, surface grinding, and tool and cutter grinding. They are versatile and affordable, making them suitable for most applications. Metal-bonded wheels are used for grinding harder materials, such as high-speed steel and carbide. They are also used for rough grinding and form grinding. Vitrified-bonded wheels are used for precision grinding and sharpening of carbide tools.Wire BrushesWire brushes are another type of abrasive tool that is used for cleaning, deburring, and finishing metal surfaces. They are made of metal wire bristles that are mounted on a rotating shaft. The wire bristles can be made of different materials, including steel, brass, and stainless steel. Wire brushes are used for removing rust, paint, and other surface contaminants from metal surfaces. They are also used for cleaning welds and deburring edges.Bench Mounted ApplicationsBench-mounted grinding wheels are used for precision grinding, sharpening, and polishing of metal parts. They are mounted on a bench or pedestal and can be used for a wide range of tasks, such as grinding, deburring, and sanding. Bench-mounted wheels are available in various sizes and materials, depending on the application.Surface Grinding WheelsSurface grinding wheels are used for precision grinding of flat surfaces. They are typically used on a reciprocating table, where the workpiece is moved back and forth against the grinding wheel. Surface grinding wheels are available in different sizes and materials, depending on the type of material being ground and the desired finish.Carbide BurrsCarbide burrs are used for shaping, deburring, and finishing metal surfaces. They are made of carbide, a hard and brittle material that is ideal for grinding and cutting. Carbide burrs are available in various shapes and sizes, depending on the application. They can be used on a variety of materials, including steel, aluminum, and cast iron.In conclusion, grinding wheels and tooling for industrial applications are essential tools for metalworking, deburring, and machine-mounted works. Bonded grinding wheels, wire brushes, bench-mounted applications, surface grinding wheels, and carbide burrs are just some of the available options. When choosing a grinding wheel or tool, it is important to consider the type of material being ground, the desired finish, and the application.
How to Expertly Manufacture a Diamond Grinding Wheel for Top Performance and Longevity
Diamond CBN Grinding Wheels – The Key to Perfect Surface FinishingGrinding wheels are an integral part of the metalworking industry, used for surface finishing, cutting, and shaping abrasive materials. With advancements in technology, the use of diamond and CBN (cubic boron nitride) abrasive materials in grinding wheels has revolutionized the industrial grinding process.Diamond and CBN abrasive materials have superior hardness and wear resistance, making them ideal for grinding hard materials like steel, ceramics, and glass. They also have excellent thermal conductivity, enabling the grinding wheel to operate at high speeds without overheating.Eagle Superabrasives Inc has emerged as a leading manufacturer of diamond and CBN grinding wheels, catering to the diverse needs of the aerospace, automotive, and manufacturing industries. Their state-of-the-art manufacturing facility promises exceptional precision, longevity, and performance.Here’s how diamond and CBN grinding wheels can help you achieve perfect surface finishing:1. High-Quality Surface Finish - Diamond and CBN abrasive materials have a uniformly sharp edge that allows them to cut smoother than traditional abrasive materials. As a result, diamond and CBN grinding wheels deliver a higher-quality surface finish while minimizing surface damage and workpiece deformation.2. Precision Grinding - The hardness and wear resistance of diamond and CBN abrasive materials make them ideal for precision grinding applications. The ability to maintain sharp edges under high loads and at high speeds ensures superior dimensional accuracy, roundness, and form.3. Reduced Grinding Time - Diamond and CBN grinding wheels achieve higher material removal rates with less pressure, resulting in reduced grinding time, minimized workpiece deformation, and improved productivity.4. Cost-Effective - Diamond and CBN grinding wheels have a longer lifespan than traditional abrasive materials, making them more cost-effective over the long run. Moreover, diamond and CBN abrasive materials require less maintenance and dressing, further reducing the costs associated with frequent wheel replacement.ConclusionAs the metalworking industry continues to evolve, manufacturers are turning to diamond and CBN abrasive materials to achieve better surface finishing, precision grind, reduced grinding time, and cost savings. Eagle Superabrasives Inc has been at the forefront of this change, providing high-quality diamond and CBN grinding wheels that meet the diverse needs of the industry.So, if you want to achieve perfect surface finishing and high-quality precision grind, choose diamond and CBN grinding wheels from Eagle Superabrasives Inc.
Ultimate Guide to Powerful Cleaning with an Angle Grinder Cleaning Brush
Title: Innovative Angle Grinder Cleaning Brush Takes Home Maintenance to the Next LevelIntroduction:In an era where cleaning tools have become more advanced and user-friendly, one company has taken the initiative to introduce an innovative cleaning solution for angle grinders. Utilizing cutting-edge technology, this angle grinder cleaning brush promises to revolutionize the way users clean this essential tool. With its multitude of features and a user-centric design, this product is set to make cleaning angle grinders more efficient and convenient. In this article, we will delve into the details of this revolutionary cleaning brush and explore the benefits it offers to both professionals and DIY enthusiasts.Section 1: The Angle Grinder Cleaning Brush - Revolutionizing Cleaning Methods (150 words)The angle grinder cleaning brush, developed by a leading provider of tools and equipment, seeks to address the longstanding challenges associated with cleaning this indispensable tool. The brush's unique design and advanced bristle technology make it an essential addition to any toolbox. Whether removing debris, rust, or stubborn dirt, this cleaning brush ensures thorough cleaning with minimal effort. The versatile brush is compatible with various angle grinder models, making it suitable for both professionals and home users. With a focus on innovation and quality, this cleaning brush is set to become a game-changer in the cleaning tool industry.Section 2: Features and Functionality (200 words)The angle grinder cleaning brush features an ergonomic design, providing users with comfort and ease of use. The handle is crafted for a secure grip, allowing for precise cleaning motions without slippage. The brush bristles are made from durable, high-quality materials, ensuring longevity even with frequent use.Furthermore, the bristles are strategically aligned to allow for optimal cleaning efficiency. The brush's engineered stiffness strikes the perfect balance between rigidity and flexibility, effortlessly removing dirt and grime from the angle grinder's surface. Additionally, the brush does not damage the grinder's delicate parts or paintwork, ensuring its longevity.Section 3: Simplifying Maintenance and Enhancing Performance (200 words)Regular maintenance of angle grinders is vital for optimal performance and longevity. However, the time-consuming and tedious task of cleaning often leads to neglect. With the introduction of this cleaning brush, maintaining an angle grinder is now easier and more convenient than ever.The brush's efficient cleaning mechanism reduces cleaning time significantly, enabling users to focus on their work rather than tackling a tedious cleaning process. By promptly removing debris and maintaining a clean surface, users can ensure that their angle grinder operates at its peak potential, enhancing performance and extending tool life.Section 4: Versatility and User-Friendliness (150 words)One of the standout features of this cleaning brush is its versatility. Regardless of the make or model of the angle grinder, this brush makes cleaning a hassle-free task. The universal fit design ensures compatibility, saving customers from the frustration of seeking a specific brush for their angle grinder.Moreover, the brush's user-friendly nature makes it accessible to both professionals and DIY enthusiasts. It requires no additional tools or knowledge, allowing anyone to efficiently clean their angle grinder without relying on external assistance. The lightweight and compact design make it highly portable, making it an essential companion for professionals working outside the workshop.Conclusion (100 words)With the introduction of the innovative angle grinder cleaning brush, users no longer have to endure the time-consuming task of manually cleaning their angle grinders. This advanced cleaning tool, with its ergonomic design and efficient bristle technology, simplifies the cleaning process while ensuring excellent results. Versatile and user-friendly, this cleaning brush will undoubtedly become a valuable addition to both professional toolkits and home workshops. Its ability to enhance maintenance, extend tool life, and improve performance makes it a must-have accessory for anyone relying on angle grinders for their work or DIY projects.
Cup Wheel Grinding Discs: Enhancing Precision and Efficiency in Grinding Tasks
Cup Wheel Grinding Discs are among the most popular and versatile tools in the grinding and cutting industry. These discs are used for a wide range of applications including shaping, grinding, and polishing various surfaces. The grinding disc is primarily designed for use on concrete surfaces, but it is also effective on other surfaces such as stone, masonry, and metal.Leading manufacturers of grinding discs produce high-quality products that cater to the needs of professionals in diverse industries, which means that the company behind it is critical to ensure that you are investing in the right product. One of the top manufacturers and suppliers of Cup Wheel Grinding Discs in the market is {}, a leading company in the abrasives industry.Beginnings of {}{} was founded in 1999 with a mission to provide quality abrasives for the machinery industry. {} has since established itself as a leading supplier of abrasives and industrial tools in the market. The company focuses on delivering the highest quality product to their customers. They invest heavily in research and development to ensure that their products are the best in the market.{} has a team of skilled engineers who work closely with the research and development team to ensure that their products meet the highest standards of quality. The company operates in modern facilities equipped with advanced machinery and tools. This ensures that they meet established industry regulations and are always one step ahead of their competitors.In addition to its manufacturing capabilities, {} has an efficient distribution network that ensures its products are readily available to customers worldwide. The company has established strong partnerships with various distributors globally who work closely with them to serve their customers and meet their needs efficiently.Product RangeThe company produces a variety of grinding discs, but the Cup Wheel Grinding Discs are one of their most popular products. The Cup Wheel Grinding Disc is available in different materials and sizes, and it comes with different grit levels depending on the needs of the user.The diamond cup wheel grinding disc is designed for heavy-duty applications such as grinding concrete, granite, and marble surfaces. The diamond cup wheel grinding disc is fitted with a diamond impregnated section that can cut through the toughest surfaces, making it the perfect tool for professionals in the concrete and stone cutting fields.Moreover, the diamond cup wheel grinding disc is available in different shapes such as the single row, double row, and turbo style cup wheel, giving professionals the freedom to choose the one that suits their specific needs.Another popular product is the silicon carbide cup wheel grinding disc, which is perfect for use on stone surfaces such as marble and granite. The silicon carbide cup wheel grinding disc is a versatile tool that is known for its fast cutting performance and durability.ConclusionAs a professional in any field, investing in quality tools is critical to ensuring that your work is not only efficient but also of the highest quality. The Cup Wheel Grinding Disc from {} is a must-have in your arsenal. By investing in the Cup Wheel Grinding Disc, you are assured of a tool that is made to the highest standards of quality and performance.
Highly Effective 400 Grit Orange Diamond Round Screens for Concrete & Stone Floors Repair & Restoration
article that highlights the benefits and uses of DiaMEND Orange Diamond Concrete & Stone Restoration Screens.DiaMEND Orange Diamond Concrete & Stone Restoration Screens – Repair Traffic Patterns, Scratches, and Stains with EaseDiamond Concrete Buffer Pad is excited to announce the launch of its new DiaMEND Orange Diamond Concrete & Stone Restoration Screens. These round screens are specifically designed to repair traffic patterns, scratches, and stains on concrete and stone floors, making it easier for building owners to maintain their floors effectively. Whether you run a commercial space or a residential property, DiaMEND Orange Diamond Concrete & Stone Restoration Screens can help extend the life of your floors and save you money in the long run.The Benefits of DiaMEND Orange Diamond Concrete & Stone Restoration ScreensDiaMEND Orange Diamond Concrete & Stone Restoration Screens are diamond-embedded polymer screens that can repair damage on concrete and stone floors while improving floor quality. These screens provide several benefits compared to traditional floor restoration methods.Firstly, DiaMEND Orange Diamond Concrete & Stone Restoration Screens are easy to use. You don't need to be an expert in floor restoration to get great results. You simply need to attach the screens to any floor buffer or auto scrubber, and you're ready to go. You can use the screens to repair thin coatings, pre-polish concrete floors, and restore shine. The screens are available in various grits.Secondly, DiaMEND Orange Diamond Concrete & Stone Restoration Screens are cost-effective. Traditional floor restoration methods can be expensive and time-consuming. With DiaMEND Orange Diamond Concrete & Stone Restoration Screens, you can repair traffic patterns, scratches, and stains on your own without having to pay for professional restoration services. This makes the process more affordable, and you can save both money and time.Lastly, DiaMEND Orange Diamond Concrete & Stone Restoration Screens are eco-friendly. Unlike traditional floor restoration methods that involve harsh chemicals, these screens use water as a cooling agent, making them environmentally friendly.How to Use DiaMEND Orange Diamond Concrete & Stone Restoration ScreensDiaMEND Orange Diamond Concrete & Stone Restoration Screens are easy to use, and you can do the job yourself without any external assistance. Here's how you can use these screens to repair traffic patterns, scratches, and stains on your concrete and stone floors.Step 1: Choose the Right GritBefore using DiaMEND Orange Diamond Concrete & Stone Restoration Screens, you need to choose the right grit. The grit you choose will depend on the level of damage on your floors. You can choose from a range of grits, including 100 grit, 200 grit, 400 grit, 800 grit, and 1500 grit.Step 2: Attach the Screens to Your Floor Buffer or Auto ScrubberOnce you've chosen the right grit, attach the screens to your floor buffer or auto scrubber. The screens are available in various sizes, including 13 inches, 15 inches, 17 inches, and 20 inches. Choose the size that's most compatible with your buffer or scrubber.Step 3: Wet the FloorBefore you start using the screens, wet the floor with water. This will prevent dust from building up and provide a smoother surface for the screens to work on.Step 4: Start the Buffing MachineStart the buffing machine and begin buffing the floor. Work in small sections, overlapping each pass slightly until you've covered the entire area. Use the appropriate amount of pressure depending on the level of damage on your floors.Step 5: Check the ProgressCheck the progress periodically. If you notice any areas that require additional work, repeat the process until you achieve the desired results.Step 6: Rinse the FloorOnce you've finished buffing the entire floor, rinse it thoroughly with water to remove any residue.Step 7: Dry the FloorDry the floor with a clean towel or let it air dry.ConclusionDiaMEND Orange Diamond Concrete & Stone Restoration Screens are a versatile, cost-effective, and eco-friendly solution for repairing damage on concrete and stone floors. With these screens, you can restore your floors to their former glory without having to pay for expensive restoration services. DiaMEND Orange Diamond Concrete & Stone Restoration Screens are a must-have tool for building owners who want to keep their floors looking great. Try them out today and see the difference they can make in your building!
Understanding the Capabilities of Wheel Grinding in Cutting Tools
Grinding wheels, which are a type of consolidated grinding tool, are extensively used in various industries for a wide range of applications. These abrasive tools are capable of coping with multiple aspects of material processing and are known for their efficiency and versatility. This article aims to explore the different functions and capabilities of grinding wheels, specifically focusing on their usage in carbide tool grinding.Grinding wheels are circular tools made up of abrasive grains attached to a bonding agent such as resin, metal, or vitrified materials. They come in various shapes, sizes, and compositions to accommodate different requirements. These wheels are used in grinding machines, which are specialized equipment designed to perform abrasive machining operations.One of the primary functions of grinding wheels is to remove excess material from a workpiece through abrasion. This process is particularly useful in shaping and forming carbide tools. Carbide tool grinding involves reshaping the cutting edges and surfaces of carbide tools to optimize their performance. Grinding wheels with abrasive grains of varying coarseness are chosen based on the specific tool material and desired finish.The hardness and durability of carbide tooling materials pose challenges for many conventional machining processes. However, grinding wheels are specially formulated to tackle this issue. They are designed to withstand the hard particles present in carbide tooling materials, ensuring effective material removal without compromising the integrity of the grinding wheel itself.Another advantage of grinding wheels is their ability to generate precise and intricate geometries. With the right selection of grinding wheel composition and size, it is possible to create complex profiles and intricate shapes on carbide tools. This is crucial for maintaining the desired cutting characteristics and edge quality of carbide tooling.In addition to shaping, grinding wheels are also used for improving the surface finish of carbide tools. By selecting an appropriate grit size and controlling the machining parameters, grinding wheels can produce a smooth and uniform surface on carbide tooling. This is critical for enhancing the tool's performance and extending its lifespan.Grinding wheels are also effective in sharpening carbide tools. Over time, the cutting edges of carbide tools become dull due to wear. Grinding wheels can be used to restore these edges to their original sharpness. The abrasion provided by grinding removes the worn-out material, exposing a fresh cutting surface. This process increases the tool's cutting efficiency and prolongs its usability.Furthermore, grinding wheels are instrumental in maintaining the dimensional accuracy and consistency of carbide tools. By carefully controlling the grinding process, it is possible to achieve tight tolerances and ensure uniform dimensions across multiple tools. This precision is vital for achieving optimal performance and compatibility when using carbide tooling in various applications.In conclusion, grinding wheels, specifically designed for carbide tool grinding, offer a host of capabilities that make them indispensable in various industrial sectors. From shaping and forming to sharpening and finishing, these abrasive tools excel in maintaining the performance, durability, and precision of carbide tools. Their ability to cope with the hardness and toughness of carbide materials, coupled with their versatility, makes grinding wheels an essential component in the carbide tool grinding process.