Unlocking the Secrets of High-Quality Auto Polishing Pads
By:Admin
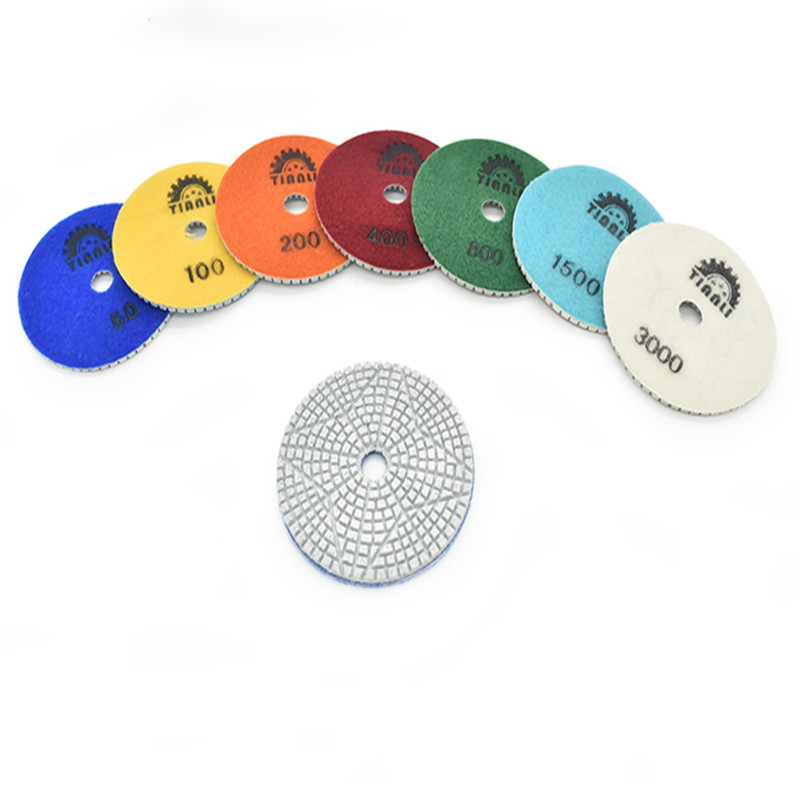
Introduction:
In the ever-evolving world of automobile care and maintenance, the brand-new auto polishing pads by an industry-leading company are set to transform the way cars are polished and restored. These groundbreaking pads promise to provide car enthusiasts with an unparalleled level of convenience, efficiency, and quality in achieving a flawless finish. This article will unravel the innovative features and benefits of these auto polishing pads, highlighting their superior performance and highlighting their potential impact on the automotive care industry.
Advanced Technology and Design:
The recently launched auto polishing pads incorporate state-of-the-art technology and cutting-edge design elements to ensure exceptional results. Featuring a proprietary blend of micro-abrasive particles and high-quality foam, these pads are engineered to deliver remarkable polishing capabilities while minimizing the risk of scratches or swirl marks on the vehicle's surface.
Eliminating the need for multiple pad changes during the polishing process, these revolutionary pads are equipped with a unique open-cell structure. This design allows for efficient dispersion of heat, preventing pad clogging and extending the pad's lifespan. Furthermore, the pads' velcro attachment system ensures easy installation and removal, facilitating a hassle-free polishing experience.
Superb Performance and Versatility:
One of the standout features of these auto polishing pads is their remarkable performance on various surfaces. Whether working on painted surfaces, clear coats, plastic trims, or even headlights, these pads excel in restoring the original shine and removing imperfections. This versatility makes them suitable for both professional detailers and car enthusiasts looking to achieve showroom-like results.
The advanced construction of these pads enables them to effectively remove oxidation, swirl marks, water spots, and light scratches, leaving a glossy finish on the vehicle's surface. Moreover, they can effortlessly tackle deeper scratches and marks, reducing the need for extensive and costly paint correction procedures. This not only saves time and effort but also contributes to the longevity of the vehicle's paint.
Environmental Consciousness:
In line with the company's commitment to sustainability, these auto polishing pads are designed with eco-friendly materials. The use of foam pads significantly reduces waste generation compared to traditional foam cutting and manufacturing techniques. Additionally, the pads can be easily cleaned and reused multiple times, promoting a greener approach to car maintenance.
Customer Satisfaction and Reviews:
Since their release, these auto polishing pads have received overwhelmingly positive feedback from users worldwide. Car detailing professionals and enthusiasts have praised the pads' outstanding performance, durability, and ease of use. Many have reported achieving flawless, high-gloss finishes, often surpassing their previous results with other polishing pads in the market.
The pads have also garnered accolades for their versatility, as they apply equally well with rotary, dual action, or random orbital polishers, accommodating a wide range of user preferences and equipment compatibility. Some customers have even considered these pads a game-changer in the car care industry, revolutionizing the way they approach vehicle restoration.
Conclusion:
With their advanced technology, superior performance, and dedication to environmental sustainability, the brand's auto polishing pads are undoubtedly setting new standards in the car care and maintenance sector. They offer a remarkable solution for car owners and professionals seeking highly effective and user-friendly tools to achieve an impeccable finish.
As these revolutionary pads continue to gain recognition and rave reviews, it is clear that they have the potential to reshape the automotive care industry, revolutionizing the way vehicles are polished and restored. Whether for personal use or professional applications, these auto polishing pads are undoubtedly a game-changer, promising to deliver unparalleled results and elevate the overall car ownership experience.
Company News & Blog
Borazon Grinding Wheels: A Comprehensive GuideWhen it comes to high-performance grinding, it's essential to use the right tools for the job. That's where Borazon grinding wheels come in. These wheels are made from cubic boron nitride (CBN), a material that is second only to diamond in terms of hardness. In this blog, we'll explore everything you need to know about Borazon grinding wheels, including their advantages, applications, and how to choose the right one for your needs.Advantages of Borazon Grinding WheelsThe main advantage of Borazon grinding wheels is their exceptional hardness. This makes them ideal for grinding hard materials that are difficult to process with traditional grinding wheels. Borazon wheels also have high abrasive resistance, which means they last longer and require less frequent replacement. Other advantages of these wheels include:• Excellent heat resistance: Borazon wheels can withstand high temperatures without cracking or degrading, making them ideal for applications that generate a lot of heat.• Superior surface finish: Borazon wheels create a smooth, precise surface finish that is free from burrs and other imperfections.• Versatile applications: Borazon wheels can be used to grind a wide range of materials, including hardened steels, cast iron, and superalloys.Applications of Borazon Grinding WheelsBorazon grinding wheels are used in a variety of applications, including:• Aerospace: Borazon wheels are used to grind turbine blades, engine parts, and other components used in the aerospace industry.• Automotive: These wheels are also used in the automotive industry to grind crankshafts, camshafts, and other engine components.• Medical: Borazon wheels are used to grind medical implants, such as hip replacements and dental implants, to ensure a precise fit.• Tool and die: These wheels can be used to grind cutting tools, such as drill bits, taps, and end mills, as well as dies and molds.Choosing the Right Borazon Grinding WheelChoosing the right Borazon grinding wheel depends on several factors, including the material you're grinding, the desired finish, and the type of machine you're using. Here are some tips to help you choose the right wheel:• Determine the hardness of the material you're grinding: Borazon wheels are best suited for grinding hard materials, so if you're grinding a soft material, you may want to consider a different type of wheel.• Consider the grit size: Borazon wheels come in a range of grit sizes, which determine how coarse or fine the abrasive particles are. Choose a finer grit for a smoother finish and a coarser grit for a more aggressive cut.• Check the compatibility with your machine: Make sure that the wheel you choose is compatible with your grinding machine. This includes checking the wheel diameter, arbor size, and maximum RPM.• Consult with a supplier: If you're unsure which wheel to choose, consult with a supplier who specializes in Borazon grinding wheels. They can help you determine the best option based on your specific needs.ConclusionBorazon grinding wheels are an essential tool for grinding hard materials to a precise finish. With their exceptional hardness, heat resistance, and abrasive resistance, these wheels offer many advantages over traditional grinding wheels. When choosing a Borazon wheel, consider the material you're grinding, the desired finish, and the compatibility with your machine. With the right wheel, you can achieve superior results and increase productivity in your grinding operations.
Discover the Latest Dry Grinding Disc for Granite: Achieve Optimal Results from 0 to 6
Granite is a type of stone that is renowned for its durability and strength. As a result, it is widely used in construction, architecture, and decorative purposes. However, working with granite can be a daunting task as it is extremely hard and requires specialized tools and techniques. In order to achieve the perfect finish on granite surfaces, it is important to use the right grinding discs. The Granite Dry Grinding Disc 0 To 6 is a product that promises to deliver exceptional results in grinding and polishing granite surfaces.The Granite Dry Grinding Disc 0 To 6 is specifically designed for dry grinding applications. Unlike traditional grinding discs, this product does not require water or other liquid to provide lubrication when grinding. This makes it an ideal choice for outdoor applications or areas where water access is limited. The product comes in various sizes, ranging from 4 inches to 7 inches in diameter. The 0 to 6 grit size of this product is perfect for grinding and smoothing out rough edges or uneven surfaces on granite.The primary benefit of the Granite Dry Grinding Disc 0 To 6 is its ability to grind and polish granite surfaces without any messy or wet residue. This helps to maintain a clean and tidy workspace, increasing efficiency and reducing the potential for slips and falls. Additionally, the product is designed to produce minimal dust, creating a healthier work environment for operators. The disc is made from high-quality materials that are durable and long-lasting, making it a cost-effective solution for grinding and polishing granite surfaces.Moreover, the company that produces the Granite Dry Grinding Disc 0 To 6 is a trusted and reputable manufacturer in the industry. Drawing on decades of experience, they have developed a range of high-quality tools and equipment for the construction and maintenance industries. The company prides itself on delivering products that offer superior performance, reliability, and durability. The Granite Dry Grinding Disc 0 To 6 is no exception, with its innovative design and high-quality materials making it the perfect tool for grinding and polishing granite surfaces.The company uses a state-of-the-art manufacturing process to produce the Granite Dry Grinding Disc 0 To 6. This involves the use of advanced technology and machinery, ensuring that each disc meets the highest standard of quality. The product is rigorously tested to ensure it can withstand the demands of the toughest job sites. Additionally, the company provides excellent customer service, offering expert advice and technical support to help customers get the best results from their products.In conclusion, the Granite Dry Grinding Disc 0 To 6 is an innovative and efficient tool for grinding and polishing granite surfaces. Its dry grinding capabilities make it an ideal choice for outdoor or limited water access areas. The product's ability to produce minimal dust and residue helps to maintain a clean and safe work environment. Furthermore, the quality of materials used and the company's commitment to excellence make this product a reliable and cost-effective solution for all your granite grinding needs. Whether you are a professional contractor or a DIY enthusiast, the Granite Dry Grinding Disc 0 To 6 is a must-have tool in your toolbox.
Resin Bonded Diamond Floor Polishing Pads for Granite, Marble, Terrazzo and Concrete
Title: Innovative Frankfurt Velcro Backed Resin-Bonded Diamond Floor Polishing Pads Revolutionize Floor FinishingIntroduction (100 words):Frankfurt Diamond Pads, a renowned name in the construction industry, has introduced a game-changing solution for floor finishing - Frankfurt Velcro Backed Resin Bonded Diamond Floor Polishing Pads. These innovative pads, suitable for granite, marble, terrazzo, stonework, and concrete, are set to redefine the standards of floor polishing. With specific application conditions and exceptional quality, these pads guarantee superior polishing results, further establishing Frankfurt Diamond Pads as a leading provider of cutting-edge solutions for the flooring market.The Frankfurt Velcro Backed Resin Bonded Diamond Floor Polishing Pads are designed to address the growing demand for efficient and cost-effective floor finishing options. Offering a remarkable combination of speed, pressure requirements, and a wet application method, it promises to transform the way floors are polished across various industries. Frankfurt Pads has left no stone unturned in ensuring that this innovative product delivers outstanding results while meeting the diverse needs of its customers.Advanced Features and Specifications (200 words):The Frankfurt Velcro Backed Resin Bonded Diamond Floor Polishing Pads boast a range of advanced features that distinguish them from traditional floor polishing options. With a recommended speed range of 500-800 RPM, these pads provide optimal performance, significantly reducing the time required for floor polishing projects. Additionally, the recommended pressure range of 5-10 kg/cm2 ensures consistent and even polishing results, resulting in floors that shine with a captivating luster.Incorporating a wet polishing method, these pads require the use of water during the polishing process, which not only enhances the performance of the pads but also helps in dust suppression. This is especially beneficial in environments where minimizing dust is critical, such as hospitals, commercial spaces, and residential areas. This capability ensures a cleaner and healthier work environment, reducing the risk of respiratory ailments.The Frankfurt Velcro Backed Resin Bonded Diamond Floor Polishing Pads come in a convenient size of 99mm x 75mm x 5mm, making them suitable for different types of floor polishing machines. Designed with the brand name removed, these pads offer a professional appearance, ensuring a seamless integration into any floor polishing process. Their durability and long-lasting performance make them a cost-effective choice for flooring professionals who seek to enhance productivity and achieve exceptional results.The Impact on the Industry (200 words):The introduction of Frankfurt Velcro Backed Resin Bonded Diamond Floor Polishing Pads marks a significant development in the field of floor finishing. Their exceptional performance, coupled with the ease of use and durability, has garnered considerable attention from professionals in the construction and flooring industries.The efficiency of these pads enables flooring companies to complete projects in a shorter timeframe while maintaining superior quality. Construction firms benefit from reduced labor costs and increased customer satisfaction, as the Frankfurt Pads ensure a refined finish that significantly enhances the aesthetic appeal of floors. Moreover, the wet polishing method and dust suppression capabilities address environmental concerns and occupational health risks associated with traditional dry polishing methods.The versatility of Frankfurt Velcro Backed Resin Bonded Diamond Floor Polishing Pads allows them to cater to a wide array of flooring materials, including granite, marble, terrazzo, stonework, and concrete, making them a valuable tool for businesses engaged in various sectors. Whether it is renovating a residential space or transforming a commercial establishment, these pads offer consistent results that exceed customer expectations.Conclusion (100 words):Frankfurt Diamond Pads has once again showcased its commitment to innovation with the introduction of Frankfurt Velcro Backed Resin Bonded Diamond Floor Polishing Pads. Delivering exceptional results on various flooring materials, these pads offer a seamless and efficient solution to the floor finishing challenges faced by professionals in the construction industry. Their advanced features, including speed and pressure requirements, combined with the benefits of wet polishing and dust suppression capabilities, make them a game-changer for the flooring market. By revolutionizing the art of floor polishing, Frankfurt Pads continues to establish itself as a leading provider of cutting-edge solutions that meet the evolving needs of the industry.
New Heavy Duty Deck Brush for Efficient Cleaning
Diamond Deck Brush: The Ultimate Solution for Efficient CleaningAre you tired of having to scrub your deck for hours and still experiencing an unsatisfactory job, or worse, having to replace your deck frequently because of damage caused by improper cleaning techniques? The Diamond Deck Brush (brand name removed), developed through years of research and innovation by our company, is the ultimate solution to all your deck cleaning woes. Read on to find out more about how our product can transform your cleaning process.At our company, we understand the importance of having not only a clean deck but also one that is well-maintained and long-lasting. We have therefore invested time and resources to develop a product that not only saves time and money but also provides the most efficient cleaning solution on the market. The Diamond Deck Brush is a product of this investment and our commitment to providing top-quality cleaning solutions.The Diamond Deck Brush features a unique diamond-patterned bristle design that ensures that no spot on your deck is left untouched during the cleaning process. This design also ensures that the bristles are gentle on your deck while still effectively removing dirt, grime, and any other stubborn stains. The brush is suitable for use on all types of decks, including wood, PVC, composite, and concrete, making it a versatile solution for all your cleaning needs.The design of the Diamond Deck Brush ensures that it can be used with any standard broom handle, allowing you to reach all areas of your deck with ease. Its lightweight design also ensures that you can use it for extended periods without experiencing fatigue.One of the best features of the Diamond Deck Brush is its ability to clean not only the surface of your deck but also the gaps between the deck boards. The bristles can get in between the gaps, removing any dirt or debris that may have accumulated. This feature is especially essential for wooden decks, where debris accumulation between boards can cause rotting and decay.At our company, we understand that cleaning your deck can often be tiring and time-consuming, which is why we have developed the Diamond Deck Brush to save you time and effort. The brush's design ensures that it requires minimal effort to remove even the most stubborn stains while still providing excellent results. You can clean your deck effortlessly and quickly, leaving you with ample time to engage in other activities.The Diamond Deck Brush is also a sustainable solution for all your cleaning needs. Its durable design ensures that you can use it for extended periods without having to replace it frequently, saving you money in the long run. The brush is also easy to clean, ensuring that it requires minimal maintenance and is always ready for use.In conclusion, the Diamond Deck Brush is the ultimate solution to all your deck cleaning needs. Its unique diamond-patterned bristle design ensures that you get maximum cleaning efficiency while still protecting your deck from damage during the cleaning process. Its lightweight design makes it easy to use, and its ability to clean the gaps between boards ensures that your deck is well-maintained. If you want a sustainable, efficient, and affordable solution for your deck cleaning needs, the Diamond Deck Brush is the product for you.
Advanced Holders for Cutting Tools, Diamond Tools, CBN Tools, and Laser Optics
Diamond Tool Holders: Revolutionizing the Industrial Cutting ProcessIn the realm of cutting tools, there is an ever-growing demand for increased efficiency and precision. Industries across the board, from automotive to aerospace, are constantly seeking innovative solutions to optimize their manufacturing processes. This pursuit has led to the development of diamond tool holders, a game-changing technology that has revolutionized industrial cutting.Diamond tool holders are essential components in cutting machinery, serving as the interface between the machine and the cutting tool. They are meticulously designed to provide stability, accuracy, and durability. The incorporation of diamonds in the tool holder material adds an extra layer of robustness, making it much more resistant to wear and tear compared to traditional tool holders.One of the key advantages of diamond tool holders is their exceptional hardness. Diamonds are known to be one of the hardest substances on Earth, surpassing all other materials commonly used in tool holders. This unique property allows diamond tool holders to withstand the extreme forces and temperatures experienced during cutting operations, resulting in a longer tool life. As a result, manufacturers can significantly reduce downtime and tool changeovers, leading to enhanced productivity and cost savings.Another noteworthy characteristic of diamond tool holders is their superior thermal conductivity. Heat generation is an inherent challenge in cutting processes, as excessive heat can negatively impact the tool's performance and lead to premature failure. However, diamond tool holders effectively dissipate heat due to their excellent thermal conductivity, ensuring the tool remains at an optimal temperature. This feature is particularly beneficial in high-speed cutting applications where heat buildup is a common concern.Furthermore, diamond tool holders minimize vibrations during machining operations. Vibrations can have a detrimental effect on the quality and precision of the final product. The inherent stiffness and rigidity of diamond give these tool holders remarkable dampening capabilities, reducing vibrations to negligible levels. By mitigating vibrations, diamond tool holders contribute to smoother cutting actions and improved surface finishes, meeting the stringent quality requirements of various industries.Diamond tool holders also excel in their ability to maintain dimensional accuracy. Precision is a critical factor in industries that demand tight tolerance in their manufacturing processes. Diamond's exceptional hardness and wear resistance ensure that the tool holder maintains its shape and size over extended periods of use. This consistent dimensional stability translates to consistent, high-quality products and eliminates the need for frequent adjustments or replacements.Moreover, the introduction of diamond tool holders has significantly expanded the scope of cutting tool applications. Diamond tool holders are compatible with a wide range of cutting tools, including both diamond and CBN (cubic boron nitride) tools. This versatility allows users to select the most suitable cutting tool for their specific application, optimizing performance and achieving desired outcomes. Industries such as automotive, aerospace, and medical device manufacturing have greatly benefited from this increased flexibility in tooling options.In conclusion, diamond tool holders have transformed the industrial cutting landscape. Their exceptional hardness, thermal conductivity, and dampening capabilities make them a superior choice for precise, efficient, and reliable cutting operations. By choosing diamond tool holders, manufacturers can improve productivity, achieve consistent and high-quality results, reduce downtime, and ultimately save costs. As the cutting tool industry continues to evolve, diamond tool holders remain at the forefront of innovation, empowering industries to push the boundaries of what is possible in the realm of cutting technology.
High-Quality Hybrid Floor Polishing Pad, Concrete Floor Pad, and Diamond Tools at Affordable Prices
: The Revolution in Polishing TechniquesPolishing floors was once a highly labor-intensive task that requires time, effort, and a plethora of technical skills. Plus, the traditional methods used to polish floors often lead to pesky issues, such as uneven surfaces, scratches, and long drying periods. Luckily, thanks to the inception of diamond floor pads, this laborious task can be accomplished with greater efficiency and in less time. So, what exactly are diamond floor pads?Diamond floor pads are a revolutionary new tool used in the process of polishing concrete, marble, and granite surfaces. These pads are made from diamond particles, which are skillfully combined with advanced bonding materials to form a highly effective and durable surface polishing tool. Additionally, the diamond floor pad has numerous benefits over earlier polishing techniques.One of the significant benefits of diamond floor pads is that they can be used for both dry and wet polishing. Unlike traditional methods that could only be executed after the surface had already dried, these new pads allow for an enhanced polishing experience. Dry polishing was previously used to tackle surface imperfections caused by uneven wear and tear. The diamond floor pads have now changed that scenario and polish the floor to a smooth, glossy finish.Another major advantage of diamond floor pads is their ability to create a more even finish across the entire floor's surface area. The pads are made with diamond particles of varying diameters that allow the operator to adjust the levels depending on the surface's texture. Additionally, diamond floor pads can be used to remove dirt, oil, and grime from the surface when used with the appropriate detergent.Diamond floor pads are also a more cost-effective option than traditional polishing surfaces. Since traditional polishing tools require a significant amount of equipment, such as special chemicals, machines, and additional labor, the overall expenses of the process can be quite expensive. Diamond floor pads make the process more cost-effective as it does not require extensive equipment, and it can be performed without rigorous training.The surfaces that diamond floor pads can polish are also diverse. These pads are effective in polishing various surfaces, including concrete, granite, marble, tiles, and porcelain. The advanced design and construction of diamond floor pads allow them to handle rough, bumpy surfaces and achieve the desired smooth surface finish with ease. It can be used for polishing indoors and outdoors, giving your floors a beautiful glossy appeal.Hybrid floor polishing pad is an extension of diamond floor pads. The hybrid floor pads typically have a grit range of 400-3000 and have diamond resin or metal segments embedded in them. These pads can quickly do the job of both metal and resin-bonded tools in one go, which is why there are becoming increasingly popular in the floor polishing world.The transition tools are used in the preparation phase, from grinding to polishing. The angle of the transition tools is precisely adjusted to avoid damaging the new surface while preparing it for the next stage. Proper use of the transition tool is essential to achieve the perfect floor finish.In conclusion, diamond floor pads have revolutionized floor polishing techniques. They're cost-effective, efficient, and versatile and can polish various surfaces to a beautiful gloss finish. The hybrid floor polishing pad and transition tools are beneficial in the overall process of polishing floors. By employing these innovative tools, we can finally say goodbye to the laborious, time-consuming, and costly process of polishing floors. Get your diamond floor pad today and experience the perfect floor finish.
Polishing Concrete Floors: Tips for Cost, Equipment, and a Successful Finish
Concrete Floor Polishing for a High-End FinishGone are the days when concrete floors were simply a utilitarian option for warehouses and industrial spaces. Today, concrete floors are used not only for their durability but also as a stylish feature for modern homes and commercial buildings. With the process of concrete floor polishing, you can make a concrete floor look and feel like a high-end finished product.Concrete floor polishing involves grinding, honing, and polishing the surface of a concrete floor to achieve a smooth, glossy finish. The process is carried out using specialized equipment, including concrete polishing pads for floor buffer.If you are considering polishing your concrete floor, here are some things to consider before you start:1. The condition of your floor: The first thing to consider before polishing your concrete floor is its condition. The surface must be free of cracks, holes, and other damages.2. The level of smoothness you want: Concrete floor polishing can be done to different levels of smoothness depending on your preference. The smoother the floor, the more reflective it will be.3. The color of the floor: Polishing brings out the natural color of your concrete floor. You can choose to have a natural look or enhance the color using dyes or stains.4. The level of maintenance required: Polished concrete floors are easy to maintain, but you need to keep them clean and free of debris to retain their glossy finish.5. The cost: The cost of concrete floor polishing varies depending on the size of the floor, the level of polishing, and other factors.To achieve success with concrete floor polishing, you need the right equipment. This includes concrete polishing pads for floor buffer, which play a crucial role in the process. These pads come in different grits, which determine the level of polishing. The higher the grit, the smoother the finish.When it comes to concrete floor polishing, you should consider hiring a professional contractor. They have the expertise, experience, and equipment needed to achieve a high-quality finish. However, if you want to do it yourself, you can rent the equipment and purchase the necessary materials, including concrete polishing pads for floor buffer.In conclusion, concrete floor polishing is an excellent way to improve the look and feel of your space. It is a durable, low-maintenance option that can last for many years. Make sure you consider all the factors before embarking on the project, and use the right equipment, including concrete polishing pads for floor buffer.
Discover Laser and Water Cutting: How It Works and Its Uses in Manufacturing and Engineering
Cutting is a widely used process in the manufacturing industry that involves the separation of materials into smaller pieces. There are several methods of cutting available, including sawing, milling, and drilling, but perhaps the most popular and efficient processes are laser cutting and water cutting.Both laser cutting and water cutting are computer-controlled methods that utilize high-tech systems to slice through materials with precision and speed. Here’s a closer look at how each of these processes works:Laser CuttingLaser cutting uses a high-powered laser beam to cut through materials such as metals, plastic, wood, and ceramics. The laser beam is directed by computer-controlled mirrors onto the material to be cut. The beam creates a localized area of intense heat that melts or vaporizes the material. The laser beam is then moved across the material to create the desired pattern or shape.One of the advantages of laser cutting is its high precision. Laser cutters are capable of cutting complex shapes with ultra-fine details. They can create sharp corners and intricate designs with minimal burring. Laser cutting is also faster and more efficient than traditional cutting methods.Laser cutting is used in a variety of applications, including industrial manufacturing, aerospace, automotive, medical, and electronics. It is ideal for cutting thin materials, and it can cut through a wide range of thicknesses, from a few micrometers to several centimeters. Laser cutting is also great for cutting reflective materials such as metals, which can be difficult to cut with traditional methods.Water CuttingWater cutting, also known as waterjet cutting, is a process that uses a high-pressure water stream to cut through materials. The water is pressurized to between 30,000 and 90,000 psi and then accelerated through a small orifice. The fast-moving water stream is then directed onto the material to be cut, typically through a nozzle.Waterjet cutting does not generate heat, making it ideal for cutting materials that are sensitive to heat, such as plastic, rubber, and foam. It can also cut through thick materials, up to several inches thick, with ease. Waterjet cutting is versatile and can be used with a variety of materials, including metals, stone, glass, and composites.One of the benefits of water cutting is its ability to cut through a wide range of materials without distorting or changing their properties. It can also cut through materials with irregular shapes and sizes. Water cutting is an environmentally-friendly process and does not generate any hazardous waste.ConclusionCutting is a crucial process in the manufacturing industry, and laser cutting and water cutting are two of the most efficient and versatile methods of cutting available today. Laser cutting uses a high-powered laser beam to cut through materials, while water cutting uses a high-pressure water stream. Both methods are computer-controlled and are ideal for cutting a wide range of materials and thicknesses. Cutting saw and other traditional cutting methods are still in use but these two advanced methods offer greater precision and speed for modern manufacturing needs.
Versatile Grinding Wheels for Industrial Metal Work and Deburring Applications
s, Bonded Grinding Wheels, Industrial Applications, Metal Work, Deburring, Bench Mounted Applications, Surface Grinding Wheels, Carbide BurrsGrinding Wheels and Tooling for Industrial ApplicationsGrinding wheels are essential tools for metalworking, deburring, and machine-mounted works. They come in various shapes and sizes and are known to be one of the most versatile abrasive tools available in the market. They are made of abrasive grains, bonding materials, and fillers, and can be used for a wide range of tasks. In this article, we will discuss the different types of grinding wheels and tooling for industrial applications.Bonded Grinding WheelsBonded grinding wheels are the most commonly used type of grinding wheel. They are made of a composite material that consists of abrasive grains held together by a bonding material. The abrasive grains are usually made of aluminum oxide, silicon carbide, or diamond, depending on the type of material being ground and the desired finish. The bonding material can be resin, metal, or vitrified.Resin-bonded wheels are commonly used for precision grinding, surface grinding, and tool and cutter grinding. They are versatile and affordable, making them suitable for most applications. Metal-bonded wheels are used for grinding harder materials, such as high-speed steel and carbide. They are also used for rough grinding and form grinding. Vitrified-bonded wheels are used for precision grinding and sharpening of carbide tools.Wire BrushesWire brushes are another type of abrasive tool that is used for cleaning, deburring, and finishing metal surfaces. They are made of metal wire bristles that are mounted on a rotating shaft. The wire bristles can be made of different materials, including steel, brass, and stainless steel. Wire brushes are used for removing rust, paint, and other surface contaminants from metal surfaces. They are also used for cleaning welds and deburring edges.Bench Mounted ApplicationsBench-mounted grinding wheels are used for precision grinding, sharpening, and polishing of metal parts. They are mounted on a bench or pedestal and can be used for a wide range of tasks, such as grinding, deburring, and sanding. Bench-mounted wheels are available in various sizes and materials, depending on the application.Surface Grinding WheelsSurface grinding wheels are used for precision grinding of flat surfaces. They are typically used on a reciprocating table, where the workpiece is moved back and forth against the grinding wheel. Surface grinding wheels are available in different sizes and materials, depending on the type of material being ground and the desired finish.Carbide BurrsCarbide burrs are used for shaping, deburring, and finishing metal surfaces. They are made of carbide, a hard and brittle material that is ideal for grinding and cutting. Carbide burrs are available in various shapes and sizes, depending on the application. They can be used on a variety of materials, including steel, aluminum, and cast iron.In conclusion, grinding wheels and tooling for industrial applications are essential tools for metalworking, deburring, and machine-mounted works. Bonded grinding wheels, wire brushes, bench-mounted applications, surface grinding wheels, and carbide burrs are just some of the available options. When choosing a grinding wheel or tool, it is important to consider the type of material being ground, the desired finish, and the application.
Quality Diamond Tools for Granite: Order Online or Call Today 01452 751123
**Title: Revolutionizing Granite Cutting with Premium Diamond Tools**Introduction:Diamond Tool Granites, a leading player in the diamond tool industry, is set to transform the granite cutting landscape with its innovative range of Granite Blades tools. With a focus on delivering exceptional performance and unmatched precision, these diamond saw blades are essential for professionals and hobbyists alike. Offering a wide range of options and the convenience of online ordering, Diamond Tool Granites is revolutionizing the way granite is processed.Enhancing Cutting Efficiency:One of the primary challenges in granite cutting is finding tools that can effectively cut through the hard and abrasive nature of the material. Diamond Tool Granites’ Granite Blades have been engineered specifically to tackle this problem. By utilizing high-quality diamonds that are either embedded or welded into the blade, the cutting speed and efficiency are significantly enhanced. This allows professionals to complete their projects with greater ease, saving both time and effort.Precision and Durability:Apart from ensuring efficient cutting, Diamond Tool Granites understands the need for precision in the granite cutting industry. Imperfections during cutting not only affect the aesthetics but can also compromise the structural integrity of the final product. The company’s Granite Blades are designed with precision in mind, ensuring clean and accurate cuts every time. With their durability, these blades are built to withstand the rigors of daily use, maintaining their sharpness and effectiveness over extended periods.Versatility and Application:Diamond Tool Granites offers a diverse range of Granite Blades, each catering to specific applications. Whether it's cutting slabs for countertops or shaping intricate designs, their extensive product line has a solution for every requirement. With varying sizes, including diameters ranging from 4 inches to 14 inches, professionals can choose the ideal blade to match their project needs. Diamond Tool Granites takes pride in the versatility of its products, providing tools suitable for both wet and dry cutting, ensuring compatibility with different cutting machines and techniques.Expert Guidance and Online Ordering:Diamond Tool Granites understands that professionals and hobbyists alike may require expert guidance to select the appropriate tools for their projects. With a team of knowledgeable professionals, the company provides personalized assistance, guiding customers through the selection process based on their unique requirements. In addition to this, Diamond Tool Granites offers the convenience of online ordering, ensuring customers can quickly and easily purchase the necessary tools without leaving their workspace. Their user-friendly website allows customers to browse the product range, compare specifications, and place orders securely and efficiently.Customer Satisfaction and Support:Diamond Tool Granites prides itself on its unwavering commitment to customer satisfaction. With an emphasis on product quality and performance, the company has garnered a loyal customer base over the years. Alongside their exceptional products, they provide reliable after-sales support, including troubleshooting assistance and warranty coverage. Customers can reach out to Diamond Tool Granites via phone or email, where their dedicated customer service team is always ready to address any concerns or queries promptly.Conclusion:Diamond Tool Granites has redefined the standards of granite cutting with its range of Granite Blades. Combining efficiency, precision, versatility, and durability, these diamond tools provide professionals with an edge in their work. With the added convenience of online ordering and expert guidance, Diamond Tool Granites is bridging the gap between high-quality diamond tools and the needs of the market. As the industry continues to advance, Diamond Tool Granites remains at the forefront, setting new benchmarks for innovation and customer satisfaction.