Improve Your Carbide Tool Sharpening with Quality Grinding Wheels
By:Admin
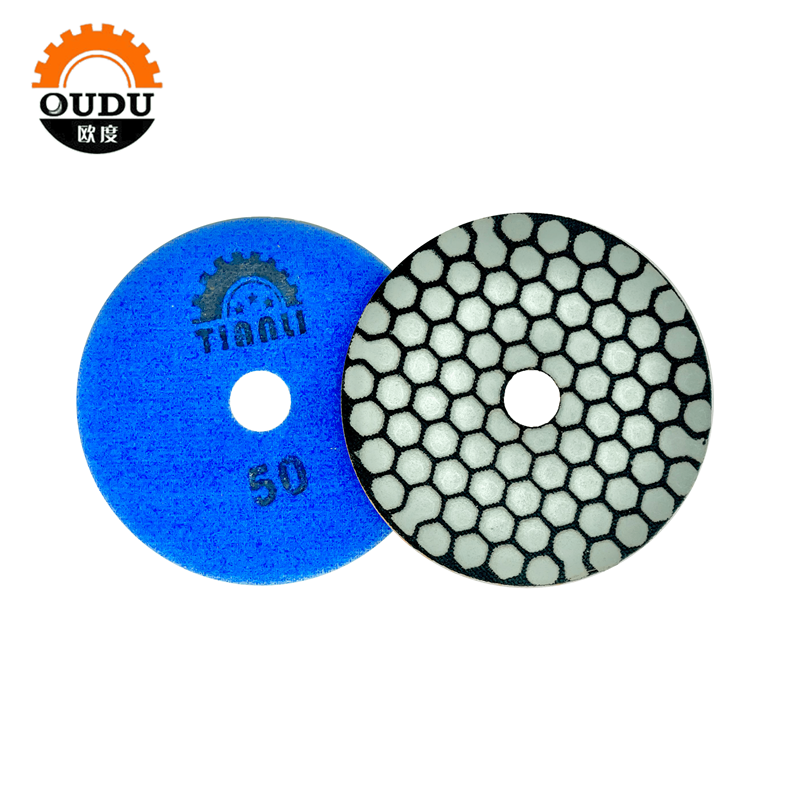
With the constant advancements in technology and engineering practices utilized in various industries worldwide, modern tool manufacturers constantly explore new possibilities and ways to meet cutting needs. As a result, various cutting tools are produced using carbide, which boasts high durability, extended service life, and a high-quality finishing. However, like all cutting tools, carbide tools are susceptible to losing their edges and thus require effective sharpening techniques. One of the most effective methods of sharpening carbide tooling is through the use of carbide tool grinding wheels.
Carbide tool grinding wheels are essential equipment for manufacturing industries that rely on carbide cutting tools. The grinding wheel comprises abrasive material fused to a wheel's surface, and the abrasive materials used in the manufacture of these grinding wheels include aluminum oxide, silicon carbide, and diamond. The wheels vary in type and design, and each one serves a unique purpose necessary for sharpening carbide tools with precision.
Carbide tooling manufacturers require a grinding wheel that is rigid, durable, and able to provide an unmatched high level of grinding accuracy. To deliver precise cuts to carbide cutting tools, manufacturers must use the most effective grinding wheel to provide optimal results.
Carbide tool grinding wheels of varying grades are available for a wide range of industrial applications. The wheels are specifically designed to meet various grit and hardness specifications in the manufacture of carbide cutting tools. The grinding wheel's hardness is identified using specific letters of the alphabet, with the letter "D" being the hardest gamma identified – each grade ranging from A to Z.
To attain precision in grinding tools using carbide grinding wheels, various factors must be considered. These include abrasive grit size, bond type, wheel hardness, and structure. Diamond is the hardest abrasive material and is ideal for grinding carbide tools, cast iron, and nonferrous metals. Furthermore, it's used in applications that require a smooth finish with sharp edges. Silicon carbide is an abrasive material used when grinding harder metals, and aluminum oxide is versatile in that it can be used to grind almost all metals. The bond type is also an essential factor, and resin bonds work well for preventing heat damage and improving productivity.
At the forefront of the carbide tool grinding wheel industry is a Taiwanese manufacturer (). The company specializes in producing diamond and CBN abrasives tools for a wide range of industrial applications. According to the company's website, they have committed to producing quality abrasive products that exceed customer requirements and expectations.
The company produces a wide range of grinding wheels for industrial applications. These include diamond grinding wheels, CBN grinding wheels, resin bond diamond grinding wheels, metal bond diamond grinding wheels, electroplated diamond grinding wheels, and vitrified bond CBN wheels. Their products are suitable for applications in the automotive, aerospace, and cutting tool industries, among others.
The company boasts an extensive range of carbide tool grinding wheels that offer manufacturers a superior option for manufacturing and sharpening carbide cutting tools. Amongst their range of specialized carbide tool grinding wheels is their resin bond diamond wheel, which offers exceptional results in sharpening carbide cutting tools while providing a more accurate finish. In addition, the company's grinding wheels comprise high-quality materials that are durable and able to withstand high grinding pressure.
In conclusion, carbide tooling has revolutionized the cutting and manufacturing industry worldwide, and manufacturers must sharpen their carbide cutting tools appropriately. Carbide tool grinding wheels are a necessary tool, and the quality and type of grinding wheel used significantly impact the quality of the sharpened tools. The company, (), is at the forefront of producing quality grinding wheels for industrial applications and offers manufacturers a superior option for manufacturing and sharpening carbide cutting tools. With their extensive range of products that meet various grinding requirements, the company has undoubtedly made it easier for manufacturers to find carbide tool grinding wheels that meet their needs.
Company News & Blog
Understanding the Capabilities of Wheel Grinding in Cutting Tools
Grinding wheels, which are a type of consolidated grinding tool, are extensively used in various industries for a wide range of applications. These abrasive tools are capable of coping with multiple aspects of material processing and are known for their efficiency and versatility. This article aims to explore the different functions and capabilities of grinding wheels, specifically focusing on their usage in carbide tool grinding.Grinding wheels are circular tools made up of abrasive grains attached to a bonding agent such as resin, metal, or vitrified materials. They come in various shapes, sizes, and compositions to accommodate different requirements. These wheels are used in grinding machines, which are specialized equipment designed to perform abrasive machining operations.One of the primary functions of grinding wheels is to remove excess material from a workpiece through abrasion. This process is particularly useful in shaping and forming carbide tools. Carbide tool grinding involves reshaping the cutting edges and surfaces of carbide tools to optimize their performance. Grinding wheels with abrasive grains of varying coarseness are chosen based on the specific tool material and desired finish.The hardness and durability of carbide tooling materials pose challenges for many conventional machining processes. However, grinding wheels are specially formulated to tackle this issue. They are designed to withstand the hard particles present in carbide tooling materials, ensuring effective material removal without compromising the integrity of the grinding wheel itself.Another advantage of grinding wheels is their ability to generate precise and intricate geometries. With the right selection of grinding wheel composition and size, it is possible to create complex profiles and intricate shapes on carbide tools. This is crucial for maintaining the desired cutting characteristics and edge quality of carbide tooling.In addition to shaping, grinding wheels are also used for improving the surface finish of carbide tools. By selecting an appropriate grit size and controlling the machining parameters, grinding wheels can produce a smooth and uniform surface on carbide tooling. This is critical for enhancing the tool's performance and extending its lifespan.Grinding wheels are also effective in sharpening carbide tools. Over time, the cutting edges of carbide tools become dull due to wear. Grinding wheels can be used to restore these edges to their original sharpness. The abrasion provided by grinding removes the worn-out material, exposing a fresh cutting surface. This process increases the tool's cutting efficiency and prolongs its usability.Furthermore, grinding wheels are instrumental in maintaining the dimensional accuracy and consistency of carbide tools. By carefully controlling the grinding process, it is possible to achieve tight tolerances and ensure uniform dimensions across multiple tools. This precision is vital for achieving optimal performance and compatibility when using carbide tooling in various applications.In conclusion, grinding wheels, specifically designed for carbide tool grinding, offer a host of capabilities that make them indispensable in various industrial sectors. From shaping and forming to sharpening and finishing, these abrasive tools excel in maintaining the performance, durability, and precision of carbide tools. Their ability to cope with the hardness and toughness of carbide materials, coupled with their versatility, makes grinding wheels an essential component in the carbide tool grinding process.
Polishing Concrete Floors: Tips and Equipment to Consider
Title: Transforming Concrete Surfaces with Advanced Concrete Polishing PadsIntroduction:In recent years, there has been a growing trend of using concrete as a sleek and stylish flooring option for commercial and residential spaces. With advancements in technology and the availability of specialized tools, concrete floor polishing has emerged as a highly effective method to enhance the appearance and durability of concrete surfaces. One essential element of the process is the use of concrete polishing pads, specifically designed for floor buffer machines. These pads play a crucial role in achieving a flawless and glossy finish on polished concrete floors.The Importance of Concrete Polishing Pads:Concrete polishing pads are specifically engineered to remove imperfections from concrete surfaces and gradually refine them to a smooth and vibrant finish. These pads are made from high-quality materials and are available in various grits, enabling professionals to fine-tune the polishing process as per the unique needs of the project.Key Considerations for Achieving Polished Concrete Floors:1. Grinding and Cost: Before embarking on a concrete floor polishing project, it is essential to consider the grinding process and associated costs. Grinding aids in removing unevenness, stains, and blemishes from the surface, creating a perfect canvas for polishing. The use of appropriate concrete polishing pads for floor machines ensures efficient grinding, leading to cost-effective results.2. Equipment and Supplies: Investing in top-notch concrete polishing equipment is vital to achieving excellent results. The use of high-quality concrete floor polishing machines, along with advanced concrete polishing pads, ensures optimal performance and durability. Additionally, reliable suppliers offer a range of concrete polishing supplies, ensuring seamless execution of the project.3. Professional Services: While DIY concrete floor polishing may seem tempting, seeking professional services is often recommended for flawless and long-lasting results. Experienced professionals possess the necessary knowledge, skills, and expertise to handle complex polishing tasks efficiently. Moreover, their access to premium concrete polishing pads and equipment ensures superior outcomes.4. Epoxy vs. Polished Concrete: When considering concrete flooring options, it's important to understand the difference between epoxy flooring and polished concrete. Epoxy provides a seamless and durable finish, suitable for high-traffic areas. On the other hand, polished concrete offers a unique aesthetic appeal, showcasing the natural beauty of the concrete. Understanding the pros and cons of each option ensures making an informed decision.Benefits of Polished Concrete Floors:1. Aesthetics: Polished concrete floors add a touch of elegance and modernity to any space. The glossy finish accentuates the natural patterns, colors, and texture of the concrete, creating a visually appealing environment.2. Durability: Polished concrete surfaces are extremely durable and resistant to scratches, stains, and wear. This makes them an ideal choice for heavy foot traffic areas, such as retail stores, warehouses, and restaurants.3. Maintenance: Polished concrete floors are easy to clean and maintain. Unlike other flooring options, they do not require waxing or additional coatings, reducing maintenance costs and efforts significantly.4. Sustainable Choice: Concrete is a sustainable material, and by choosing polished concrete floors, one contributes to a greener environment. Reduced maintenance requirements and a longer lifespan further enhance its eco-friendly characteristics.Conclusion:Concrete floor polishing has revolutionized the flooring industry, presenting a cost-effective and visually appealing alternative to traditional options. Key to achieving impeccable results is the use of high-quality concrete polishing pads, specifically designed for floor buffer machines. Professionals well-versed in the process, coupled with advanced equipment and supplies, ensure that concrete surfaces are transformed into durable, elegant, and sustainable flooring solutions.
Find Reputed Polishing Pad Suppliers and Manufacturers - Import Easily from All Countries at buyindustrialtools.com
Polishing Pad: A Great Tool for Achieving a Mirror-Like FinishA polishing pad is an essential tool in the field of metalworking, woodworking, and automotive repair. It is used to achieve a mirror-like finish on surfaces of different materials, including metal, wood, and plastics. Polishing pads are available in different sizes, shapes, and materials, each designed for specific applications. In this blog post, we will talk about polishing pads, their benefits, and how to choose the right one.What is a Polishing Pad?A polishing pad is a circular tool that attaches to an angle grinder, rotary tool, or drill. It consists of a foam or wool backing that holds the abrasive material. The foam or wool backing is essential for distributing and absorbing the pressure, preventing swirls, scratches, and gouges from forming on the surface being polished. The abrasive material can be diamond, aluminum oxide, or silicon carbide, depending on the hardness and thickness of the material being polished.Benefits of Using a Polishing PadUsing a polishing pad has several benefits, including:1. Smooth and Uniform Finish: A polishing pad can achieve a smooth and uniform finish on any surface, removing scratches, swirls, and blemishes.2. Time and Labor-Saving: Polishing pads are quick and efficient, saving time and labor costs. They can remove imperfections, stains, and oxidation quickly without damaging the surface.3. Versatility: Polishing pads can be used on various materials, including metal, wood, plastics, and painted surfaces, making them versatile tools for a range of applications.4. Consistent Results: Polishing pads produce consistent results, ensuring that the surface achieved is the same every time, which is essential for projects that require a uniform finish.Choosing the Right Polishing PadChoosing the right polishing pad is essential for achieving the desired results. Here are some factors to consider when selecting the right polishing pad for your project.1. Material being polished - Different materials require different types of polishing pads. For instance, a soft foam pad is ideal for polishing paint, while a wool pad is perfect for metal surfaces.2. Grit - The grit size determines the level of abrasiveness of the polishing pad. A fine grit of 800-1000 is ideal for achieving a mirror-like finish.3. Size - The size of the polishing pad should match the size of the surface being polished. A larger pad is ideal for polishing large surfaces, while a smaller pad is suitable for intricate details.4. Speed - The speed at which the polishing pad spins is essential for achieving the desired results. A higher speed produces a more aggressive cut, while a slower speed produces a finer finish.ConclusionA polishing pad is an essential tool for achieving a mirror-like finish on a range of materials. They are quick, efficient, and versatile, saving time and labor costs while producing consistent results. When choosing a polishing pad, consider factors such as the material being polished, the grit, size, and speed. Investing in a quality polishing pad is a sound investment that will provide excellent results for years to come. So, if you're looking to achieve a flawless finish, consider investing in a 100mm polishing pad. It is the perfect size for most applications and will produce a mirror-like shine on any surface.
Discover Laser and Water Cutting: How It Works and Its Uses in Manufacturing and Engineering
Cutting is a widely used process in the manufacturing industry that involves the separation of materials into smaller pieces. There are several methods of cutting available, including sawing, milling, and drilling, but perhaps the most popular and efficient processes are laser cutting and water cutting.Both laser cutting and water cutting are computer-controlled methods that utilize high-tech systems to slice through materials with precision and speed. Here’s a closer look at how each of these processes works:Laser CuttingLaser cutting uses a high-powered laser beam to cut through materials such as metals, plastic, wood, and ceramics. The laser beam is directed by computer-controlled mirrors onto the material to be cut. The beam creates a localized area of intense heat that melts or vaporizes the material. The laser beam is then moved across the material to create the desired pattern or shape.One of the advantages of laser cutting is its high precision. Laser cutters are capable of cutting complex shapes with ultra-fine details. They can create sharp corners and intricate designs with minimal burring. Laser cutting is also faster and more efficient than traditional cutting methods.Laser cutting is used in a variety of applications, including industrial manufacturing, aerospace, automotive, medical, and electronics. It is ideal for cutting thin materials, and it can cut through a wide range of thicknesses, from a few micrometers to several centimeters. Laser cutting is also great for cutting reflective materials such as metals, which can be difficult to cut with traditional methods.Water CuttingWater cutting, also known as waterjet cutting, is a process that uses a high-pressure water stream to cut through materials. The water is pressurized to between 30,000 and 90,000 psi and then accelerated through a small orifice. The fast-moving water stream is then directed onto the material to be cut, typically through a nozzle.Waterjet cutting does not generate heat, making it ideal for cutting materials that are sensitive to heat, such as plastic, rubber, and foam. It can also cut through thick materials, up to several inches thick, with ease. Waterjet cutting is versatile and can be used with a variety of materials, including metals, stone, glass, and composites.One of the benefits of water cutting is its ability to cut through a wide range of materials without distorting or changing their properties. It can also cut through materials with irregular shapes and sizes. Water cutting is an environmentally-friendly process and does not generate any hazardous waste.ConclusionCutting is a crucial process in the manufacturing industry, and laser cutting and water cutting are two of the most efficient and versatile methods of cutting available today. Laser cutting uses a high-powered laser beam to cut through materials, while water cutting uses a high-pressure water stream. Both methods are computer-controlled and are ideal for cutting a wide range of materials and thicknesses. Cutting saw and other traditional cutting methods are still in use but these two advanced methods offer greater precision and speed for modern manufacturing needs.
Rewrite for SEO optimization: Supplier for Wet Polishing Pads - Weihai Chengxun Import & Export Co., Ltd., offering a wide range of granite slabs, tombstones, granite countertops, vanity tops, monuments, slate and marble fireplaces, wooden shutters, film faced plywood, garden fountains, water pots, marble carvings, diamond tools, cutting blades, and polishing pads.
Diamond Wet Polishing Pads: The Ultimate Guide to Achieving Perfect Stone FinishPolishing is an important process in the production of stone surfaces. It is the final step that helps improve the aesthetic value of the stone. Because of the huge demand for stone products, manufacturers are always looking for ways to improve their production processes to ensure they deliver top-quality products. This has led to the production of different types of polishing pads. Diamond wet polishing pads are currently the most popular type of polishing pads on the market. In this article, we’ll take a closer look at diamond wet polishing pads.What are diamond wet polishing pads?Diamond wet polishing pads are polishing tools used to polish stone surfaces, such as granite, marble, and concrete. They are called "diamond" wet polishing pads because they are made of diamond particles. This means that they are designed to handle tougher materials, unlike traditional polishing pads. They are called "wet" polishing pads because they are used in combination with water. The water acts as a lubricant and helps to reduce heat generated during the polishing process.What makes diamond wet polishing pads unique?Diamond wet polishing pads are unique because they are designed to last longer than traditional polishing pads. This is because they are made of diamond particles, which are durable and wear-resistant. This allows them to handle even the toughest materials, providing a consistent and flawless finish. They are also the best choice when it comes to polishing edges and corners, as they provide excellent precision, and leave no scratches or marks.What are the different types of diamond wet polishing pads?There are different types of diamond wet polishing pads available on the market. They vary in terms of their size, quality, and intended use. Some popular types include:1. Electroplated diamond polishing pads: These are diamond pads that are attached to the backing plate with an electroplating process. They are durable and provide excellent results when polishing granite and other hard materials.2. Resin diamond polishing pads: These are diamond pads that use a resin binder to hold the diamond particles together. They are suitable for use on softer stones, such as marble or travertine.3. Metal bond diamond polishing pads: These are diamond pads that are designed to handle the toughest materials, such as concrete. They are the most aggressive type of diamond polishing pad and will leave scratches that can be removed by finer grits.How to use diamond wet polishing pads?Using diamond wet polishing pads is a fairly simple process. Here are some steps to follow:1. Choose the right pad grit: Depending on the type of stone you are polishing, you will need to choose the correct grit. Start with a coarser grit and work your way up to finer grits until you achieve the desired finish.2. Attach the pad: Attach the diamond pad to a polisher. Ensure that the polisher is water-fed to keep the surface of the stone cool and to avoid dust.3. Begin polishing: Start polishing the surface of the stone, moving the polisher in a circular motion. Keep the surface wet at all times to prevent overheating.4. Change the pads: As you move from coarser to finer grits, change to a new pad. This is to avoid cross-contamination and to achieve the desired finish.ConclusionDiamond wet polishing pads are a must-have for anyone looking to achieve a perfect, polished finish on stone surfaces. They are durable and long-lasting, providing a consistent finish every time. With the right technique and grit sequence, you can achieve an excellent finish on any stone material. Make sure to always choose the right grit for the stone you are working on, and to keep the surface wet to avoid overheating. With diamond wet polishing pads, you can achieve a stunning, polished finish that will last for years to come.
High-Quality Polishing Pads for Angle Grinders - Perfect for Marble, Granite, Concrete, and Glass - Global Shipping Available
Polishing Pads for Angle Grinder: The Ultimate Guide for Polishing Various MaterialsAre you looking for a versatile and efficient way to polish materials such as marble, granite, concrete, or even glass? Look no further! In this comprehensive guide, we will explore the world of polishing pads for angle grinders, providing valuable insights and tips on how to achieve a flawless finish. Whether you are a professional stone fabricator or simply an avid DIY enthusiast, understanding the different types of grinder pads for polishing will undoubtedly take your polishing game to the next level.Before diving into the details of grinder pads for polishing, let's take a moment to appreciate the significance of the angle grinder itself. Owing to its compact size and high rotational speed, the angle grinder has become a popular choice among professionals and amateurs alike. Its versatile nature allows it to perform a plethora of tasks, including cutting, grinding, and, of course, polishing. Pairing this mighty tool with the right polishing pad can transform it into a powerful weapon for achieving spectacular results.Now, let's shift our focus to the star of our discussion – polishing pads. Polishing pads are essential tools used to refine and bring out the natural beauty of various materials. These pads consist of a base material with an abrasive surface designed to work effectively on different surfaces. There are several factors to consider when selecting the appropriate pad for a specific material, such as hardness, grit size, and pad composition.When it comes to hardness, it is crucial to match the pad to the material you are working on. For instance, softer pads are recommended for delicate surfaces like glass, while harder ones are more suitable for granite or concrete. This careful selection ensures optimal results without causing any damage to the material.Another crucial aspect to consider is the grit size of the pad. Grit size refers to the size of the abrasive particles embedded in the pad. The general rule of thumb is to start with larger grit sizes and progressively move to finer ones for a flawless finish. Coarser grit sizes, such as 50 or 100, are ideal for initial material removal or leveling uneven surfaces, while finer grit sizes like 400 or 800 are perfect for achieving a mirror-like shine.In terms of pad composition, there are several options available on the market. Diamond polishing pads, for example, are widely recognized for their durability and effectiveness. These pads use diamond particles bonded to the pad surface to perform efficient material removal and polishing. Their high quality ensures a longer lifespan and superior performance compared to traditional pads.Additionally, resin polishing pads are gaining popularity due to their versatility and user-friendliness. These pads utilize a combination of resin and diamond particles to provide excellent polishing results. Their flexible nature allows them to adapt to irregular surfaces, making them ideal for rounded edges or curved areas.One noteworthy feature of many polishing pads is the presence of water holes. These holes play a crucial role in cooling down the pad during the polishing process, reducing the risk of overheating and ensuring smoother operations. It is advisable to select pads with a suitable number and arrangement of water holes, depending on the intensity and duration of the polishing job at hand.Now that we have covered the essentials of polishing pads for angle grinders, it's time to highlight the significance of international shipping. If you are a professional stone fabricator or a passionate DIYer, sourcing high-quality grinder pads for polishing locally might not always be possible or financially feasible. Nevertheless, many reputable online platforms offer international shipping services, enabling you to access a wide range of polishing pads at competitive prices, irrespective of your geographic location.In conclusion, grinder pads for polishing are indispensable tools for achieving exceptional results when working with materials like marble, granite, concrete, and glass. By understanding the importance of hardness, grit size, and pad composition, you can select the perfect pad for your specific needs. Furthermore, considering the advantages of online marketplaces that offer international shipping, you can effortlessly access high-quality and affordable polishing pads from anywhere in the world. So, gear up your angle grinder, grab the appropriate polishing pads, and get ready to transform ordinary surfaces into stunning masterpieces!
High-Quality Wet Polishing Pads for Stone Polishing Needs
Flexibility is the key when it comes to achieving a flawless finish on various stones such as marble, granite, and concrete. And what better tool to use than wet polishing pads? Wet polishing pads are widely recognized and trusted in the industry for their exceptional performance in polishing different types of stones. In this blog post, we will take a closer look at these versatile tools and discover why they are an essential part of any polishing project.When it comes to polishing, one of the most important factors to consider is the type of pad being used. Wet polishing pads are designed to provide maximum flexibility, which allows them to conform to the contours of the stone being polished. This flexibility ensures that the pad can reach all areas of the stone, including those hard-to-reach corners and edges, ensuring a consistent and even polish.One of the main benefits of using wet polishing pads is their ability to prevent overheating during the polishing process. The water used during wet polishing helps to dissipate heat, preventing the pad from becoming too hot and damaging the stone. This not only ensures the longevity of the pad but also extends the life of the stone being polished.Additionally, using wet polishing pads significantly reduces the amount of dust generated during the polishing process. This is particularly important when working with materials such as concrete, as the dust can be harmful to both the operator and the surrounding environment. Wet polishing pads capture the dust particles, keeping the workspace clean and safe.Wet polishing pads are suitable for use on a variety of stones, including marble, granite, and concrete. Marble is a delicate stone that requires gentle polishing to reveal its natural beauty. Wet polishing pads are perfect for marble polishing as their flexible design allows for a soft touch while still providing excellent results. The pads won't cause any scratching or damage to the marble's surface, ensuring a polished finish that is both stunning and long-lasting.Granite, on the other hand, is a much harder stone and requires a more aggressive polishing approach. Wet polishing pads, with their various grit levels, are capable of tackling even the toughest of granite surfaces. Whether it's removing deep scratches or achieving a high-gloss shine, wet polishing pads have got you covered. Their flexibility allows for consistent and controlled abrasion, ensuring optimal results every time.Concrete polishing has gained immense popularity in recent years, especially in the world of interior design. Wet polishing pads are an excellent choice for concrete polishing due to their versatility and adaptability. They can be used for everything from rough grinding to fine polishing, allowing you to achieve the desired level of sheen and smoothness. With wet polishing pads, you can transform dull concrete floors into beautiful, polished surfaces that are not only visually appealing but also highly durable.In conclusion, wet polishing pads are an essential tool for any stone polishing project. Their flexibility, ability to prevent overheating, and dust-controlling properties make them the go-to choice for professionals and DIY enthusiasts alike. Whether you are working with marble, granite, or concrete, wet polishing pads provide exceptional results and ensure that the finished product is nothing short of perfection.So, when it comes to polishing your precious stones, don't forget to consider the wet polishing pads. They are the ultimate companion in achieving the beautiful, polished finish you desire. Open up a new world of possibilities and let your stones shine with the help of flexible diamond wet polishing pads.
Top-Quality Diamond Grinding Wheels for Superior Performance, Precision and Durability
Diamond CBN Grinding Wheels: Benefits and ApplicationsGrinding wheels are highly essential in the manufacturing industry for a wide range of applications ranging from shaping, cutting, and grinding. While there are various types of grinding wheels, diamond and CBN grinding wheels offer immense benefits in terms of exceptional performance, precision, and longevity. Diamond CBN grinding wheels, also known as Superabrasive wheels, are efficient and highly effective materials for cutting and shaping different materials, especially those that are hard to machine.What are Diamond CBN Grinding Wheels?A diamond grinding wheel is a type of abrasive tool that features diamond-coated abrasive beads that are used for grinding, cutting, and shaping different materials. On the other hand, CBN (cubic boron nitride) grinding wheels feature abrasive beads coated with CBN, another common superabrasive material.Diamond and CBN Grinding Wheels are DifferentDiamond and CBN grinding wheels feature different properties that make them ideal for specific applications. For example, the diamond grinding wheel is suitable for grinding materials such as carbides, ceramics, glass, and other hard materials. CBN grinding wheels, on the other hand, are ideal for grinding materials such as high-speed steels and super alloys.Applications of Diamond CBN Grinding WheelsDiamond and CBN grinding wheels have a wide range of applications in different industries, including:1. Aerospace Industry: Diamond CBN grinding wheels are widely used in the aerospace industry for grinding materials such as nickel-based alloys, titanium alloys, and aluminum alloys. These materials are commonly used in the manufacture of aircraft engines, blades, and other components.2. Automotive Industry: In the automotive industry, diamond CBN grinding wheels are used for grinding and shaping the engine components, such as camshafts, crankshafts, and valves, among others. This helps to improve the durability, performance, and efficiency of these components.3. Medical Industry: The medical industry uses diamond CBN grinding wheels for grinding medical implants, surgical tools, and other precision components. Diamond CBN grinding wheels are ideal for materials such as tungsten carbide, ceramics, and titanium, among others.4. Glass Industry: Diamond CBN grinding wheels are used in the glass industry for grinding and polishing glass surfaces such as lenses, mirrors, and optical components. Diamond grinding wheels are preferred due to their ability to produce high-quality finishes and precision.Benefits of Diamond CBN Grinding Wheels1. Longevity: Diamond CBN grinding wheels are highly durable and can last longer than other types of grinding wheels. They are designed to provide consistent performance over extended periods, making them cost-effective solutions for various applications.2. High Performance: Diamond CBN grinding wheels are designed to provide high levels of precision and performance. They are capable of producing high-quality finishes and sharp edges that are ideal for precision grinding applications.3. Versatility: Diamond CBN grinding wheels can be used for grinding a wide range of materials, including carbides, ceramics, glass, and other hard materials. They are highly versatile and can be used in different industries.4. Reduced Downtime: Diamond CBN grinding wheels require minimal maintenance, resulting in less downtime and increased productivity. They are designed to provide consistent performance even in high-pressure applications.ConclusionDiamond CBN grinding wheels offer immense benefits in terms of longevity, precision, and performance. They are widely used in different industries, including aerospace, automotive, medical, and glass. If you are in the manufacturing industry and looking for high-quality grinding wheels, consider purchasing diamond CBN grinding wheels. They are cost-effective solutions that offer consistent performance over extended periods.
Economical Wet Polishing Pads for Effective Granite Polishing
: Achieving a Perfect FinishGranite surfaces are remarkable in providing the perfect blend of style and durability. From kitchen countertops to floors, walls, and statues, granite is a popular material used in homes and commercial buildings. However, to ensure that your surfaces are always looking their best, you need to invest in a high-quality granite wet polisher. In this blog post, we will discuss achieving a perfect finish using a granite wet polisher.Why Use a Granite Wet Polisher?A wet polisher is an essential tool for polishing granite surfaces. As the name implies, a wet polisher works with water, which acts as a lubricant and cooling agent to prevent overheating of the granite. Wet polishing also helps to remove dust particles, ensuring a smoother and cleaner finish. A granite wet polisher removes scratches, brings out the natural shine of the stone, and eliminates any imperfections on the surface.Choosing the Right Polishing PadsWhen it comes to polishing granite, you need the right polishing pads. The Puma Economy Wet Polishing Pads are an excellent choice for achieving a perfect finish. These pads are designed to perform well at a great price, making them an economic option. Additionally, the Puma polishing system features exclusive Geo patterns that help displace and channel water during use, ensuring a smoother and more polished finish.The 7 Step Puma Polishing SystemThe 7 Step Puma polishing system includes seven different grits of polishing pads that help achieve a mirror-like polished surface. The grit progression starts from coarsest to finest, starting at 50, 100, 200, 400, 800, 1500, and ending with 3000. You need to follow each step of the polishing process with care, ensuring that you remove any scratches or rough spots before proceeding to the next step. Remember that each step prepares the surface for the next, so take time to complete each one before moving on.Steps to Achieving a Perfect Granite Polished SurfaceStep 1: Clean the SurfaceThe first step is to clean the granite surface thoroughly. Use a soft brush or vacuum to remove any dirt or debris on the surface.Step 2: Start with Coarse GritsAttach the 50-grit polishing pad to the granite wet polisher and start polishing the surface. Work in sections, keeping the pad flat and applying even pressure. Once the surface is smooth and free of scratches, move on to the next finer grit.Step 3: Progress to Finer GritsContinue working through the finer grits until you reach the 3000-grit polishing pad. At each stage, ensure that the surface is clean and free of scratches before moving on to the next grit.Step 4: Rinse the SurfaceOnce you've completed each stage, rinse the surface with water to remove any debris. Check that the surface is completely clean and free of scratches.Step 5: Apply Granite SealerAfter polishing, it's advisable to apply granite sealer to protect the surface from stains and water damage.Step 6: Buff the SurfaceUse a soft buffing pad on the granite wet polisher to buff the surface to a high shine. Use water to lubricate the surface and prevent heat damage.Step 7: Clean the Surface Once AgainFinally, clean the surface one last time to remove any buffing residue and leave the surface sparkling.ConclusionAchieving a perfect finish on granite surfaces requires patience, attention to detail, and the right equipment. By using a granite wet polisher with the correct polishing pads and following each step of the polishing process, you can achieve a mirror-like polished finish. The Puma Economy Wet Polishing Pads are an economic, quality option for achieving a perfect finish on granite surfaces. So the next time you're looking to polish granite surfaces, invest in quality tools, and you'll be proud of your finished product.
Revolutionary New Grinding Disc Technology Unveiled: A Game Changer in Surface Preparation
Title: Innovative Grinding Disc Revolutionizes Metalworking IndustryIntroduction:In today's fast-paced industrial landscape, the search for innovative tools to enhance productivity and efficiency remains constant. This quest for advancement has led to the development of a groundbreaking grinding disc by an industry-leading company. Combining cutting-edge technology with unrivaled performance, this new grinding disc is poised to revolutionize the metalworking industry.Unleashing the Power of the Grind Disc:The newly unveiled grind disc, developed by a renowned manufacturing company, is set to transform metalworking processes by offering unmatched performance, durability, and efficiency. Through extensive research and advanced engineering, the company has successfully created a tool that vastly increases productivity while reducing costs for metalworkers across various sectors.Technical Innovation:The proprietary technology behind this grind disc incorporates state-of-the-art materials and an innovative design, resulting in a truly exceptional product. The disc's abrasive composition and unique shape contribute to its ability to remove material more efficiently, delivering fast and precise results. Furthermore, the disc's enhanced durability ensures prolonged usage, reducing the downtime associated with frequent replacement.Enhanced Performance and Versatility:The grind disc's cutting-edge design guarantees superior performance across a wide range of applications. From shaping and leveling to finishing and polishing, this multi-purpose tool offers versatility for a variety of metalworking tasks. Regardless of the desired outcome, this innovative grinding disc consistently delivers exceptional results, making it an essential addition to any metalworking arsenal.Ergonomic Design:Recognizing the importance of workplace ergonomics, the grind disc incorporates a user-friendly design. The disc's lightweight construction, combined with its ergonomic handle, ensures comfortable handling during extended periods of work. This feature reduces operator fatigue and increases overall efficiency, further maximizing productivity while prioritizing worker safety.Eco-Friendly Manufacturing:The company behind this groundbreaking grinding disc is committed to responsible manufacturing practices. With sustainability at the core of their operations, they have implemented stringent measures to minimize environmental impact. From the sourcing of raw materials to the disc's production process, every stage adheres to eco-friendly guidelines, ensuring a product that meets the demands of today's environmentally conscious metalworking industry.Driving Industry Innovation:The introduction of this revolutionary grind disc signifies a significant step toward reshaping the metalworking landscape. By combining cutting-edge technology with unparalleled performance, the company responsible for this groundbreaking tool is spearheading industry innovation. This development not only improves productivity for metalworkers but also inspires further advancements in tool design and manufacturing techniques.Collaborative Approach:To ensure continuous product improvement and customer satisfaction, the company has actively engaged with metalworking professionals throughout the development process. Collaborative feedback and input from industry experts have played a crucial role in refining the grind disc's performance, making it a truly reliable and user-friendly tool.Conclusion:The metalworking industry can look forward to a transformative shift with the introduction of this groundbreaking grind disc. Boasting unrivaled performance, cutting-edge technology, and a commitment to sustainability, this innovative tool is set to revolutionize metalworking processes worldwide. As the industry embraces this advancement, productivity, efficiency, and worker satisfaction are expected to reach unprecedented heights, paving the way for a brighter future in metalworking.