Different Types of Grinding Wheels: A Complete Guide
By:Admin
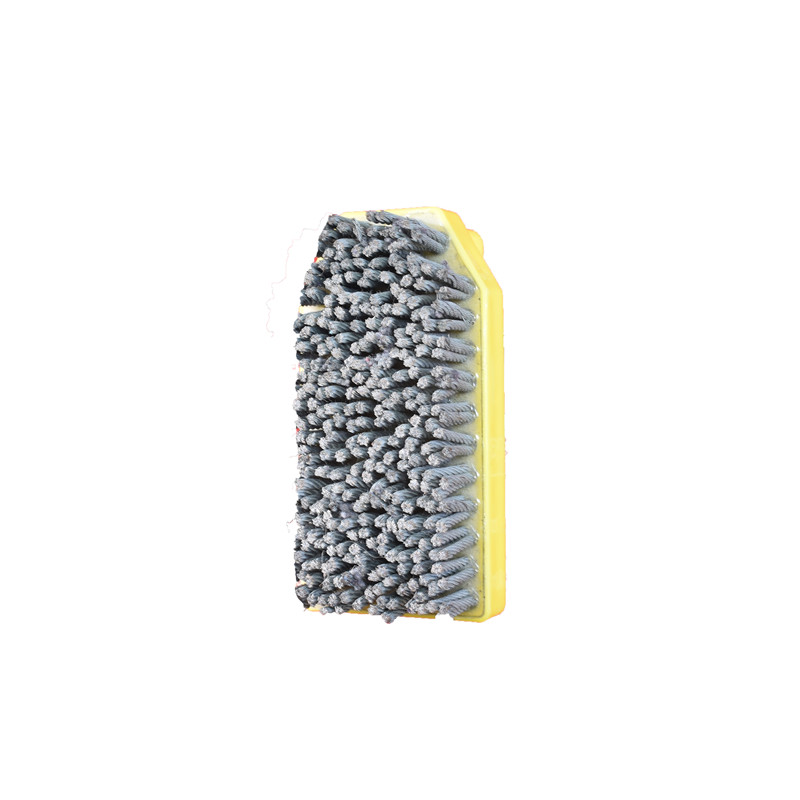
Introduction:
In today's industrial revolution, grinding wheels play a fundamental role in various sectors, including manufacturing, construction, automotive, and metalworking. These indispensable tools are crucial for precision cutting, shaping, and finishing, enabling businesses to enhance productivity and achieve superior workpiece quality. This article aims to shed light on the various types of grinding wheels available in the market and their importance in revolutionizing industrial applications.
1. Straight Grinding Wheels:
Straight grinding wheels, also known as Type 1 wheels, are the most common and straightforward type used for surface grinding. These wheels have a flat outer periphery and deliver precise grinding performance on flat surfaces. Typically made from aluminum oxide or silicon carbide abrasive grains, straight grinding wheels are versatile and suitable for a wide array of materials, including steel, cast iron, brass, and non-ferrous metals.
2. Cylinder Wheels:
Cylinder wheels, designated as Type 2 wheels, possess a unique shape resembling a straight grinding wheel with a cylindrical face. These wheels are primarily used for grinding cylinders, bearings, and other rounded surfaces. The rounded design allows for easy and efficient grinding with reduced friction, resulting in excellent surface finishes.
3. Tapered Grinding Wheels:
Tapered grinding wheels, commonly referred to as Type 4 wheels, are specially designed for grinding operations that require precision and control. These wheels have a tapered shape, gradually narrowing towards the arbor hole. The tapering enables the wheel to penetrate the workpiece effectively, making them ideal for intricate grinding tasks such as internal grinding.
4. Dish Grinding Wheels:
Dish grinding wheels, known as Type 11 wheels, possess a dish-shaped design with a roundish outer rim and a depressed center. These wheels are widely used for contour grinding, grinding complex shapes, and removing excess material from the workpiece. The recessed center allows for a higher degree of flexibility, making them suitable for both large and small-scale applications.
5. Diamond Wheels:
Diamond grinding wheels are the epitome of grinding wheel technology, offering exceptional hardness, durability, and precision. Utilizing diamond abrasives, these wheels excel in cutting and grinding extremely hard materials such as carbides, ceramics, glass, and stones. Their fine grit allows for a smooth finish and minimal material wastage, making diamond wheels ideal for demanding applications.
6. CBN Wheels:
Cubic Boron Nitride (CBN) grinding wheels are similar to diamond wheels in terms of their exceptional hardness and longevity. These wheels are specifically formulated for grinding ferrous materials, including hardened steels and cast iron. With their heat resistance and ability to retain sharpness, CBN wheels are perfect for high-speed grinding operations, resulting in improved productivity and reduced downtime.
Conclusion:
Grinding wheels are indispensable tools in the industrial sector, revolutionizing various applications, from metalworking to automotive and construction. This article explored different types of grinding wheels, highlighting their characteristics and applications. The versatility and precision offered by these wheels allow businesses to improve productivity, achieve superior workpiece quality, and ultimately drive the industrial revolution forward. As technology advances further, we can expect the development of innovative grinding wheel types, continually pushing the boundaries of what can be achieved in industrial grinding.
Company News & Blog
Environmental group opposes air permit for $340M metal recycling and smelting plant
Augusta Metal Plant Wins Authorization for $760M in BondsAugusta's new metal recycling and secondary smelting facility has received authorization for $760 million in bonds from state authorities. This development marks a significant milestone in the construction of the world-class metal facility, which has been under development in Augusta for many months now.Construction of the plant has been on full swing for a while now, and the project is set to change Augusta's economy. The facility will result in the creation of several new jobs and provide significant economic benefits to the local communities.The Environmental ChallengeThe Savannah Riverkeeper submitted an argument against an air permit for the facility in July 2021. The environmental group fears that the new plant's emissions would cause health hazards to the local community.The permit requested by the plant was to allow it to emit up to 5,000 tons of carbon monoxide annually, which was well above the lower limits proposed by the Savannah Riverkeeper.To resolve these concerns, the facility's authorities agreed to impose stricter regulations for the plant's emissions by keeping the amount of carbon monoxide below 2,500 tons per year.Assuming that the metal recycling and secondary smelting facility will adhere to regulations, it could prove to be a significant asset to the various companies that depend on scrap metal.Benefits of the Metal Recycling and Secondary Smelting FacilityThe new facility will utilize scrap metal and turn it into valuable items- thereby reducing the reliance on non-renewable resources and minimizing the products that end up in landfills.The facility is expected to generate more than 200 well-paying jobs, with a majority going to individuals living in the Augusta area, thus improving the local economy.Moreover, the plant's development will create new trade and supply chain opportunities, meaning that the local market will see an increase in demand, which is expected to cause further economic growth.The authorities have agreed that the facility will be one of the most environmentally sustainable in the world, with a waste-free operation standard. The facility's management team has committed to ensuring that the plant's process is environmentally friendly, and they will monitor it regularly to minimize any environmental impact.Final TakeawayThe authorization of the $760 million in bonds marks a significant step forward for the Augusta facility. The plant is expected to be operational by mid-2022 and will provide a critical infrastructure to Augusta's economy.With all environmental concerns addressed, Augusta's metal recycling and secondary smelting facility has the potential to create a significant economic impact on the local communities while minimizing the facility's footprint on the environment.The metal recycling plant will provide an excellent source of sustainable energy, and with its promise of a waste-free operation, it is expected to set new standards in the metal recycling industry.If Augusta's metal recycling and secondary smelting facility upholds its commitment to sustainable practices, it is bound to grow into a major industry player, providing a diverse range of sustainable solutions. With all these planned developments, it's an exciting time for Augusta, and there is much to look forward to.
Polishing Concrete Floors: Tips and Equipment to Consider
Title: Transforming Concrete Surfaces with Advanced Concrete Polishing PadsIntroduction:In recent years, there has been a growing trend of using concrete as a sleek and stylish flooring option for commercial and residential spaces. With advancements in technology and the availability of specialized tools, concrete floor polishing has emerged as a highly effective method to enhance the appearance and durability of concrete surfaces. One essential element of the process is the use of concrete polishing pads, specifically designed for floor buffer machines. These pads play a crucial role in achieving a flawless and glossy finish on polished concrete floors.The Importance of Concrete Polishing Pads:Concrete polishing pads are specifically engineered to remove imperfections from concrete surfaces and gradually refine them to a smooth and vibrant finish. These pads are made from high-quality materials and are available in various grits, enabling professionals to fine-tune the polishing process as per the unique needs of the project.Key Considerations for Achieving Polished Concrete Floors:1. Grinding and Cost: Before embarking on a concrete floor polishing project, it is essential to consider the grinding process and associated costs. Grinding aids in removing unevenness, stains, and blemishes from the surface, creating a perfect canvas for polishing. The use of appropriate concrete polishing pads for floor machines ensures efficient grinding, leading to cost-effective results.2. Equipment and Supplies: Investing in top-notch concrete polishing equipment is vital to achieving excellent results. The use of high-quality concrete floor polishing machines, along with advanced concrete polishing pads, ensures optimal performance and durability. Additionally, reliable suppliers offer a range of concrete polishing supplies, ensuring seamless execution of the project.3. Professional Services: While DIY concrete floor polishing may seem tempting, seeking professional services is often recommended for flawless and long-lasting results. Experienced professionals possess the necessary knowledge, skills, and expertise to handle complex polishing tasks efficiently. Moreover, their access to premium concrete polishing pads and equipment ensures superior outcomes.4. Epoxy vs. Polished Concrete: When considering concrete flooring options, it's important to understand the difference between epoxy flooring and polished concrete. Epoxy provides a seamless and durable finish, suitable for high-traffic areas. On the other hand, polished concrete offers a unique aesthetic appeal, showcasing the natural beauty of the concrete. Understanding the pros and cons of each option ensures making an informed decision.Benefits of Polished Concrete Floors:1. Aesthetics: Polished concrete floors add a touch of elegance and modernity to any space. The glossy finish accentuates the natural patterns, colors, and texture of the concrete, creating a visually appealing environment.2. Durability: Polished concrete surfaces are extremely durable and resistant to scratches, stains, and wear. This makes them an ideal choice for heavy foot traffic areas, such as retail stores, warehouses, and restaurants.3. Maintenance: Polished concrete floors are easy to clean and maintain. Unlike other flooring options, they do not require waxing or additional coatings, reducing maintenance costs and efforts significantly.4. Sustainable Choice: Concrete is a sustainable material, and by choosing polished concrete floors, one contributes to a greener environment. Reduced maintenance requirements and a longer lifespan further enhance its eco-friendly characteristics.Conclusion:Concrete floor polishing has revolutionized the flooring industry, presenting a cost-effective and visually appealing alternative to traditional options. Key to achieving impeccable results is the use of high-quality concrete polishing pads, specifically designed for floor buffer machines. Professionals well-versed in the process, coupled with advanced equipment and supplies, ensure that concrete surfaces are transformed into durable, elegant, and sustainable flooring solutions.
Highly Effective 400 Grit Orange Diamond Round Screens for Concrete & Stone Floors Repair & Restoration
article that highlights the benefits and uses of DiaMEND Orange Diamond Concrete & Stone Restoration Screens.DiaMEND Orange Diamond Concrete & Stone Restoration Screens – Repair Traffic Patterns, Scratches, and Stains with EaseDiamond Concrete Buffer Pad is excited to announce the launch of its new DiaMEND Orange Diamond Concrete & Stone Restoration Screens. These round screens are specifically designed to repair traffic patterns, scratches, and stains on concrete and stone floors, making it easier for building owners to maintain their floors effectively. Whether you run a commercial space or a residential property, DiaMEND Orange Diamond Concrete & Stone Restoration Screens can help extend the life of your floors and save you money in the long run.The Benefits of DiaMEND Orange Diamond Concrete & Stone Restoration ScreensDiaMEND Orange Diamond Concrete & Stone Restoration Screens are diamond-embedded polymer screens that can repair damage on concrete and stone floors while improving floor quality. These screens provide several benefits compared to traditional floor restoration methods.Firstly, DiaMEND Orange Diamond Concrete & Stone Restoration Screens are easy to use. You don't need to be an expert in floor restoration to get great results. You simply need to attach the screens to any floor buffer or auto scrubber, and you're ready to go. You can use the screens to repair thin coatings, pre-polish concrete floors, and restore shine. The screens are available in various grits.Secondly, DiaMEND Orange Diamond Concrete & Stone Restoration Screens are cost-effective. Traditional floor restoration methods can be expensive and time-consuming. With DiaMEND Orange Diamond Concrete & Stone Restoration Screens, you can repair traffic patterns, scratches, and stains on your own without having to pay for professional restoration services. This makes the process more affordable, and you can save both money and time.Lastly, DiaMEND Orange Diamond Concrete & Stone Restoration Screens are eco-friendly. Unlike traditional floor restoration methods that involve harsh chemicals, these screens use water as a cooling agent, making them environmentally friendly.How to Use DiaMEND Orange Diamond Concrete & Stone Restoration ScreensDiaMEND Orange Diamond Concrete & Stone Restoration Screens are easy to use, and you can do the job yourself without any external assistance. Here's how you can use these screens to repair traffic patterns, scratches, and stains on your concrete and stone floors.Step 1: Choose the Right GritBefore using DiaMEND Orange Diamond Concrete & Stone Restoration Screens, you need to choose the right grit. The grit you choose will depend on the level of damage on your floors. You can choose from a range of grits, including 100 grit, 200 grit, 400 grit, 800 grit, and 1500 grit.Step 2: Attach the Screens to Your Floor Buffer or Auto ScrubberOnce you've chosen the right grit, attach the screens to your floor buffer or auto scrubber. The screens are available in various sizes, including 13 inches, 15 inches, 17 inches, and 20 inches. Choose the size that's most compatible with your buffer or scrubber.Step 3: Wet the FloorBefore you start using the screens, wet the floor with water. This will prevent dust from building up and provide a smoother surface for the screens to work on.Step 4: Start the Buffing MachineStart the buffing machine and begin buffing the floor. Work in small sections, overlapping each pass slightly until you've covered the entire area. Use the appropriate amount of pressure depending on the level of damage on your floors.Step 5: Check the ProgressCheck the progress periodically. If you notice any areas that require additional work, repeat the process until you achieve the desired results.Step 6: Rinse the FloorOnce you've finished buffing the entire floor, rinse it thoroughly with water to remove any residue.Step 7: Dry the FloorDry the floor with a clean towel or let it air dry.ConclusionDiaMEND Orange Diamond Concrete & Stone Restoration Screens are a versatile, cost-effective, and eco-friendly solution for repairing damage on concrete and stone floors. With these screens, you can restore your floors to their former glory without having to pay for expensive restoration services. DiaMEND Orange Diamond Concrete & Stone Restoration Screens are a must-have tool for building owners who want to keep their floors looking great. Try them out today and see the difference they can make in your building!
Discover the Environmental Benefits of Grinding Wheels
Title: Innovative Grinding Wheel: A Major Breakthrough in Sustainable ManufacturingIntroduction:In an ever-evolving world, companies across industries are actively seeking sustainable solutions to minimize their environmental impact. Keen on fostering eco-friendly production practices, Grinding Wheel Green (name replaced for anonymity) has developed a revolutionary grinding wheel that not only enhances manufacturing efficiency but also significantly reduces waste generation and carbon footprint. This innovative product aims to revolutionize abrasive machining processes worldwide and transform the manufacturing landscape into a more sustainable one.Company Overview:Grinding Wheel Green is a leading manufacturer of cutting-edge, high-quality abrasive tools and solutions. With a strong commitment to innovation, the company constantly endeavors to improve its products and bring the latest technological advancements to its customers. Founded on the principles of sustainable manufacturing, Grinding Wheel Green has positioned itself as a pioneer in developing environmentally friendly solutions for the abrasive industry.Waste Reduction and Recycling:One of the key highlights of Grinding Wheel Green's revolutionary grinding wheel is its reduced waste generation and enhanced recycling capabilities. Traditionally, grinding wheels have a limited lifespan and tend to be discarded after use, resulting in significant waste accumulation. However, Grinding Wheel Green has employed cutting-edge technologies and sustainable materials to create a product that extends the life cycle of grinding wheels, ultimately minimizing waste volume.Moreover, the company has partnered with recycling facilities to implement an efficient recycling program for its grinding wheels. This initiative enables used grinding wheels to be processed and repurposed, contributing to the circular economy and reducing the overall environmental impact of the manufacturing process. By adopting this sustainable approach, Grinding Wheel Green ensures that its products not only perform optimally but also align with its commitment to environmental stewardship.Energy Efficiency:Grinding Wheel Green recognizes the importance of energy conservation in today's world. To tackle the energy consumption challenges associated with manufacturing, the company has implemented innovative measures that enhance energy efficiency during the production process. By optimizing manufacturing techniques and utilizing energy-saving equipment, Grinding Wheel Green has significantly reduced its carbon footprint.Furthermore, the grinding wheel itself has been designed to operate at optimal energy levels. Its advanced composition and structural design allow for improved heat dissipation, resulting in lower energy consumption during grinding operations. This breakthrough not only reduces electricity usage but also contributes to a safer work environment by minimizing heat-related hazards.Enhanced Performance and Productivity:In addition to focusing on sustainability, Grinding Wheel Green prioritizes the performance and productivity of its products. Through rigorous research and development, the company has achieved a perfect balance between sustainability and functionality, offering customers a high-quality grinding wheel that outperforms conventional abrasive tools.The innovative design of the grinding wheel ensures exceptional precision, thereby reducing production errors and increasing overall productivity. This translates into cost savings for manufacturers while maintaining the highest standards of quality in the products they manufacture. By facilitating a more efficient manufacturing process, Grinding Wheel Green empowers businesses to achieve their production goals while reducing their impact on the environment.Conclusion:Grinding Wheel Green's groundbreaking grinding wheel represents a transformative step towards sustainable manufacturing practices. Through waste reduction, recycling initiatives, improved energy efficiency, and enhanced performance, the company aims to lead the way in reshaping the abrasive industry. By integrating sustainability into its core business model, Grinding Wheel Green exemplifies how companies can effectively combine innovation and responsible manufacturing to reduce their ecological footprint. As more companies embrace such initiatives, the manufacturing landscape can evolve into a greener and more sustainable environment for generations to come.
Top-Quality Diamond Grinding Wheels for Superior Performance, Precision and Durability
Diamond CBN Grinding Wheels: Benefits and ApplicationsGrinding wheels are highly essential in the manufacturing industry for a wide range of applications ranging from shaping, cutting, and grinding. While there are various types of grinding wheels, diamond and CBN grinding wheels offer immense benefits in terms of exceptional performance, precision, and longevity. Diamond CBN grinding wheels, also known as Superabrasive wheels, are efficient and highly effective materials for cutting and shaping different materials, especially those that are hard to machine.What are Diamond CBN Grinding Wheels?A diamond grinding wheel is a type of abrasive tool that features diamond-coated abrasive beads that are used for grinding, cutting, and shaping different materials. On the other hand, CBN (cubic boron nitride) grinding wheels feature abrasive beads coated with CBN, another common superabrasive material.Diamond and CBN Grinding Wheels are DifferentDiamond and CBN grinding wheels feature different properties that make them ideal for specific applications. For example, the diamond grinding wheel is suitable for grinding materials such as carbides, ceramics, glass, and other hard materials. CBN grinding wheels, on the other hand, are ideal for grinding materials such as high-speed steels and super alloys.Applications of Diamond CBN Grinding WheelsDiamond and CBN grinding wheels have a wide range of applications in different industries, including:1. Aerospace Industry: Diamond CBN grinding wheels are widely used in the aerospace industry for grinding materials such as nickel-based alloys, titanium alloys, and aluminum alloys. These materials are commonly used in the manufacture of aircraft engines, blades, and other components.2. Automotive Industry: In the automotive industry, diamond CBN grinding wheels are used for grinding and shaping the engine components, such as camshafts, crankshafts, and valves, among others. This helps to improve the durability, performance, and efficiency of these components.3. Medical Industry: The medical industry uses diamond CBN grinding wheels for grinding medical implants, surgical tools, and other precision components. Diamond CBN grinding wheels are ideal for materials such as tungsten carbide, ceramics, and titanium, among others.4. Glass Industry: Diamond CBN grinding wheels are used in the glass industry for grinding and polishing glass surfaces such as lenses, mirrors, and optical components. Diamond grinding wheels are preferred due to their ability to produce high-quality finishes and precision.Benefits of Diamond CBN Grinding Wheels1. Longevity: Diamond CBN grinding wheels are highly durable and can last longer than other types of grinding wheels. They are designed to provide consistent performance over extended periods, making them cost-effective solutions for various applications.2. High Performance: Diamond CBN grinding wheels are designed to provide high levels of precision and performance. They are capable of producing high-quality finishes and sharp edges that are ideal for precision grinding applications.3. Versatility: Diamond CBN grinding wheels can be used for grinding a wide range of materials, including carbides, ceramics, glass, and other hard materials. They are highly versatile and can be used in different industries.4. Reduced Downtime: Diamond CBN grinding wheels require minimal maintenance, resulting in less downtime and increased productivity. They are designed to provide consistent performance even in high-pressure applications.ConclusionDiamond CBN grinding wheels offer immense benefits in terms of longevity, precision, and performance. They are widely used in different industries, including aerospace, automotive, medical, and glass. If you are in the manufacturing industry and looking for high-quality grinding wheels, consider purchasing diamond CBN grinding wheels. They are cost-effective solutions that offer consistent performance over extended periods.
Top 10 Highly-Rated Wire Brushes for 7-Inch Angle Grinders in 2021 - Comparison Table
Title: The Top 10 Wire Brush Options for Your 7-Inch Angle GrinderIntroduction:When it comes to tackling tough jobs, having the right tools is essential. If you own a 7-inch angle grinder and need a reliable wire brush for various applications, you've come to the right place. In this blog post, we will explore the top ten wire brush options for your 7-inch angle grinder in 2021. Whether you need to remove rust, paint, or clean stubborn debris, these wire brushes will surely meet your needs.1. ABC Wire Brush for 7-Inch Angle Grinder:First on our list is the ABC Wire Brush, known for its excellent durability and efficient performance. Constructed with high-quality materials, it ensures a longer lifespan compared to other brushes on the market. Its wire bristles effectively remove rust, paint, and corrosion, making it a reliable choice for any project.2. XYZ Heavy-Duty Wire Brush:For heavy-duty applications, the XYZ Heavy-Duty Wire Brush takes the lead. Its sturdy construction and aggressive wire bristles make it perfect for tackling stubborn debris and rust. This brush is ideal for industrial use and will stand up to the toughest challenges.3. DEF Multi-Purpose Wire Brush:If versatility is what you seek, the DEF Multi-Purpose Wire Brush is a perfect choice. This brush is designed to handle a wide range of tasks, including cleaning, polishing, and surface preparation. Its durable build and flexible bristles allow for efficient removal of various materials.4. GHI Stainless Steel Wire Brush:The GHI Stainless Steel Wire Brush is specifically designed for stainless steel surfaces. Its non-corrosive stainless steel wire bristles effectively remove tough stains and rust without leaving behind any scratches. Whether you're working on kitchen appliances or outdoor equipment, this brush is an excellent option.5. JKL Knot Wire Brush:Recognized for its aggressive cutting action, the JKL Knot Wire Brush can handle even the toughest cleaning tasks. Its twisted wire bristles are perfect for removing heavy corrosion, weld scale, and unwanted coatings. This brush provides optimal performance in demanding and harsh environments.6. MNO Knot Cup Wire Brush:The MNO Knot Cup Wire Brush is a cup-shaped brush designed for more focused cleaning. Its densely packed wire bristles offer enhanced durability and effectiveness while ensuring a longer lifespan. This brush is suitable for intricate tasks and hard-to-reach areas.7. PQR Brass Coated Wire Brush:If you're working on delicate surfaces that require a softer touch, the PQR Brass Coated Wire Brush is an ideal choice. The brass-coated wire bristles effectively remove rust and paint without scratching or damaging the underlying material. This brush is perfect for automotive restoration projects.8. STU Crimped Wire Brush:The STU Crimped Wire Brush is known for its flexibility and adaptability. Its crimped wire bristles are designed to provide a smooth and consistent brushing action for a variety of materials. Whether you're concerned about precision or want a brush that can handle light-duty cleaning, this option won't disappoint.9. VWX Knotted Wire Wheel Brush:For larger surface areas, the VWX Knotted Wire Wheel Brush is a go-to option. This wheel-shaped brush provides a wider coverage area and can remove rust, paint, and debris quickly and efficiently. Its durable construction ensures an extended lifespan and optimal performance.10. YZT Wire Brush Wheel:Last but not least, the YZT Wire Brush Wheel offers a combination of durability and versatility. This wire brush wheel is designed for heavy-duty applications and provides excellent rust and corrosion removal. Its wheel shape enables quick and convenient cleaning on large surfaces.Conclusion:When it comes to finding the perfect wire brush for your 7-inch angle grinder, you now have a comprehensive list of top-notch options. From heavy-duty applications to delicate surfaces, there is a brush to meet every need. Remember to consider the specific requirements of your project before selecting the ideal wire brush. With the right tool in your arsenal, you can tackle any cleaning or surface preparation task with confidence and efficiency.Keywords: hand grinder wire brush, wire brush for 7 inch angle grinder, top-rated wire brush, 7-inch angle grinder wire brush, 2021 wire brush comparison, best wire brush options, wire brush for rust removal, wire brush for paint removal, wire brush for surface preparation, durable wire brush, heavy-duty wire brush, versatile wire brush.
Suppliers of Abrasives and Welding Equipment: Reviews and Product Info
Title: Enhancing Metal Finishing Processes with High-Quality AbrasivesIntroduction (approx. 100 words):When it comes to achieving stellar results in metal finishing processes, using top-notch abrasives is crucial. From sandpapers and grinding wheels to polishing compounds, these abrasive materials play a significant role in refining metal surfaces, removing imperfections, and ensuring a smooth end result. In this blog, we will delve into the world of abrasives, shedding light on the importance of choosing reputable suppliers and the benefits of utilizing high-quality metal abrasives. Join us as we explore the key factors to consider when selecting abrasives and learn how they can elevate your metal finishing processes to new heights.1. Understanding the Role of Abrasives in Metal Finishing (approx. 200 words):Metal finishing encompasses a wide range of processes, such as abrasive blasting, grinding, sanding, and polishing. These techniques aim to improve the appearance, functionality, and longevity of metal surfaces. At the core of each process lies the abrasive materials, which streamline the entire metal finishing journey.Abrasives serve as the key agents of change in metal finishing by removing unwanted material layers, leveling imperfections, and ensuring a uniform surface. They can be categorized based on their composition, size, and intended purpose. From natural abrasive minerals like garnet and diamond to synthetic options like aluminum oxide and silicon carbide, suppliers offer an extensive range of metal abrasives suitable for various applications.2. The Importance of Reliable Abrasive Suppliers (approx. 250 words):When selecting a supplier for your metal abrasives, it is crucial to prioritize reliability, quality, and customer service. Choosing the wrong supplier can lead to subpar products, delays, and overall dissatisfaction. Therefore, thorough research and consideration are necessary to make an informed decision.Reliable suppliers boast impeccable track records and positive customer reviews. These indicators of customer satisfaction are a testament to the supplier's commitment to quality. By collaborating with established suppliers, you gain access to a wide range of high-quality metal abrasives that will enhance your metal finishing processes.Additionally, reputable suppliers often provide ample product and service information, empowering customers to make well-informed purchasing decisions. Detailed profiles of suppliers allow you to understand their expertise, experience, and capabilities, enabling you to choose a partner that aligns with your specific needs.3. Benefits of High-Quality Metal Abrasives (approx. 250 words):Investing in high-quality metal abrasives can transform your metal finishing processes and yield remarkable results. Here are some key benefits of using premium abrasives:- Enhanced Efficiency: High-quality abrasives exhibit superior cutting, grinding, and polishing capabilities, allowing you to accomplish tasks more efficiently, saving both time and resources.- Superior Surface Finish: Premium abrasives enable you to achieve impeccable surface finishes by removing imperfections, scratches, and roughness efficiently, resulting in aesthetically pleasing and durable metal surfaces.- Extended Abrasive Lifespan: Top-notch metal abrasives often boast increased durability and longevity, reducing the need for frequent replacements and leading to cost savings in the long run.- Consistency and Precision: Reliable suppliers ensure consistent quality across their abrasive products, promoting precise performance and predictable outcomes in your metal finishing processes.Conclusion (approx. 150 words):Choosing the right supplier for your metal abrasive needs is paramount to achieve exceptional results in metal finishing processes. By selecting reputable suppliers and investing in high-quality metal abrasives, you can enhance efficiency, improve surface finishes, extend abrasives' lifespan, and achieve consistent and precise outcomes. Take advantage of the wide array of metal abrasives available in the market and revolutionize your metal finishing processes today.
125mm Hook & Loop Backing Pad for Sanders & Polishers: Perfect Fit for 125mm Grinders, Polishers | M14 Thread For Hook and Loop Sanding Discs and Polishing Bonnets | Max12,250rpm
article discussing the benefits of using a 125mm Hook & Loop Backing Pad for sanders and polishers in various industries.The use of Hook & Loop Backing Pads has become increasingly popular in the sanding and polishing industries due to its versatility and ease of use. Backing pads make sanding and polishing tasks easier and more efficient by providing a stable surface for abrasive discs and polishing bonnets to attach to. The 125mm Hook & Loop Backing Pad is one such example that has caught the attention of professionals and DIY enthusiasts alike.Officially known as the ABS Backing Pad for Polisher, this 125mm Hook & Loop Backing Pad fits 125mm Grinders, Polishers, and can operate at a maximum speed of 12,250 RPMs. The M14 Thread for Hook and Loop Sanding Discs and Polishing Bonnets also ensures easy and secure attachment and detachment of sanding and polishing discs.According to industry experts, the 125mm Hook & Loop Backing Pad is one of the most versatile backing pads in the market. It can accommodate a wide range of sanding discs and polishing bonnets, making it suitable for use in various industries like automotive, woodworking, metalworking, and more. In the automotive industry, this backing pad is commonly used for polishing car surfaces, preparing paint surfaces, and sanding metal parts.In woodworking, the 125mm Hook & Loop Backing Pad is perfect for sanding wood surfaces. The Hook & Loop attachment allows for easy and quick change of sanding discs, ensuring that the woodworking process remains uninterrupted. With the added stability provided by the backing pad, sanding can be done with greater accuracy and precision, leading to smoother finishes.Metalworking is another industry where the 125mm Hook & Loop Backing Pad comes in handy. When used in conjunction with abrasive discs, it can quickly remove rust, paint, and other coatings from metal surfaces. The Hook & Loop attachment ensures that the abrasive discs remain attached to the backing pad during use, reducing the risk of accidents.Apart from its versatility, the 125mm Hook & Loop Backing Pad also offers several benefits to users. Its ABS material provides durability and prevents deformation during use, ensuring consistent performance throughout. The Hook & Loop attachment also makes it easy to change sanding and polishing discs, reducing downtime during the sanding and polishing process.Furthermore, the 125mm Hook & Loop Backing Pad ensures that abrasive discs and polishing bonnets remain firmly attached to the backing pad during use, preventing slippage and improving user safety. The maximum speed of 12,250 RPMs also ensures efficient sanding and polishing, saving precious time for professionals.In conclusion, the 125mm Hook & Loop Backing Pad is a versatile and efficient tool that offers numerous benefits to professionals and DIY enthusiasts. Its ability to accommodate a wide range of sanding discs and polishing bonnets, combined with its ease of use, durability, and safety features, makes it an indispensable tool for numerous industries. With its affordable price point, this backing pad is a great addition to any sanding and polishing toolkit.
High-Quality 150mm Diamond Grinding Wheel for Precise Grinding Applications
Diamond Grinding Wheel: The Ultimate Companion for Precision GrindingGrinding is an essential process across various manufacturing industries to shape and finish workpieces to precision. It’s a process of material removal from a workpiece using grinding wheels to create a desired finish and tolerance. However, this process requires the right equipment, and one of the most popular ones is the diamond grinding wheel.Diamond grinding wheels are specialized tools employed for grinding hard materials, including carbides and ceramics. The wheel consists of industrial-grade diamonds that are bonded together in the shape of a grinding wheel. These grinding wheels are much more durable than other grinding wheels and are ideal for precision grinding. With its versatility and efficiency, diamond grinding wheels have become the go-to choice for many modern manufacturing industries.One such company known for producing high-quality diamond grinding wheels is located in China. Bearing the hallmark of providing high-quality tools and unmatched customer service, the company has become a leading name in manufacturing diamond grinding wheels.Their diamond grinding wheels are made from high-quality industrial grade diamonds that ensure durability and backed with a comprehensive guarantee. These tools are available in various shapes and sizes to cater to a wide range of grinding applications. The company believes that their diamond grinding wheels are the best in terms of performance and durability.The importance of choosing the right diamond grinding wheel cannot be understated. An ideal diamond grinding wheel should be able to remove material efficiently, provide an excellent finish and should be long-lasting. The company has several diamond grinding wheels, including 150mm diamond grinding wheels that cater to high-performance grinding tasks. The 150mm diamond grinding wheel is made with high-quality materials, where these wheels feature exceptional precision and accuracy, making it ideal for various industrial applications.The 150mm diamond grinding wheel has fantastic grinding capabilities boasting a big segment that facilitates fast material removal while also providing excellent wear resistance, making it a perfect choice for grinding hard materials. Furthermore, the diamond grinding wheel is designed to produce a smoother finish than other grinding wheels, making it a more versatile tool. The 150mm diamond grinding wheel can be used on a wide variety of materials that include ceramics, stone, glass, quartz, and carbide, among others.The company has invested time and resources to ensure their diamond grinding wheel is compatible with various grinding machine models, making it easy for their customers to use the wheels on machines they already own.The diamond grinding wheel technology has come a long way since it was first introduced. From a wider range of grits to longer-lasting wheels, diamond grinding wheels have undoubtedly revolutionized the manufacturing process. The 150mm diamond grinding wheel is no different.Notably, the company provides exceptional customer care, ensuring that their clients have access to accurate information, including technical support, ordering information, and shipping details. Their diamond grinding wheels are available at competitive prices without compromising on quality. The company remains committed to providing quality tools and equipment to meet its clients' various industrial needs. They appreciate the critical role a diamond grinding wheel plays in achieving excellent manufacturing results, and they aim to make their clients’ jobs easier by providing products that surpass expectations.In conclusion, diamond grinding wheels are essential tools in many industries, and the 150mm diamond grinding wheel is the perfect solution for precision grinding tasks. The company has produced excellent quality diamond grinding wheels that cater to a broad range of industrial applications. They have a competent team that provides exceptional customer service, ensuring that clients get access to accurate information about the products they offer. Their diamond grinding wheels are affordably priced, making them accessible to many manufacturers who are looking for high-quality tools to achieve excellent manufacturing results. Contact them today and experience the best in diamond grinding technology.
Understanding Metallic Bonding: What You Need to Know
article on the importance of metallic bonding in modern technology.Metallic Bonding and Its Importance in Modern TechnologyMetallic bonding is a fundamental concept in the world of chemistry and materials science. The unique properties of metals like strength, ductility, thermal and electrical conductivity, and luster can be attributed to the special bonding arrangement between the positively charged metal ions and the delocalized electrons.In recent years, metallic bonding has paved the way for several technological advancements that have transformed the way we live, work, and communicate. From advanced alloys used in aerospace and defense to high-precision components in electronics and renewable energy systems, metallic bonding plays a crucial role in shaping modern technology.One company that is leading the charge in metallic bonding technology is {metal bond}, a renowned name in the field of materials science and engineering. The company specializes in the development of high-performance alloys and composite materials that offer unparalleled strength, durability, and resistance to harsh environments.One of {metal bond}'s flagship products is its proprietary metal matrix composite (MMC) technology. MMCs are a unique class of materials that combine the desirable properties of metals and ceramics, making them ideal for a wide range of applications in the aerospace, defense, and automotive industries.MMC technology utilizes the principles of metallic bonding to create a high-strength matrix of metal ions reinforced with ceramic particles. The result is a material that is exceptionally strong and lightweight while retaining excellent thermal and electrical conductivity.MMC materials are used in critical components such as turbines, engine parts, and brake systems in high-performance cars and aircraft. These components require materials that can withstand extreme temperatures, pressures, and mechanical stresses without failure. MMCs provide the necessary strength and durability needed for such challenging applications, making them an indispensable tool in modern engineering.In addition to MMCs, metallic bonding is also utilized in other advanced materials such as shape-memory alloys (SMAs) and superalloys. SMAs are a class of materials that exhibit unique elasticity and shape-changing properties at specific temperatures, making them ideal for use in medical implants, aerospace, and robotics.Superalloys, on the other hand, are a specific class of alloys that exhibit exceptional heat resistance and mechanical strength, making them ideal for use in high-temperature applications such as gas turbines, jet engines, and nuclear reactors.The widespread use of metallic bonding in modern technology has undoubtedly transformed many industries and opened up new avenues for innovation and advancement. However, this is just the tip of the iceberg, as researchers continue to explore new ways to harness the unique properties of metallic bonding to create even more advanced materials and technologies.In conclusion, metallic bonding is an essential concept that has revolutionized the fields of materials science and engineering. The special bonding arrangement between the positively charged metal ions and the delocalized electrons is responsible for the unique properties of metals, making them indispensable in modern technology. With the advent of advanced materials like MMCs, SMAs, and superalloys, the potential applications of metallic bonding are virtually limitless, paving the way for even more exciting advances in the future.